1. General Discussion
1.1 Background
1.1.1 History
This wipe sampling method was
developed to provide a uniform and practical means of taking wipe
samples for 1,6-hexamethylene diisocyanate (HDI). The sampling of HDI
on surfaces was performed using Ghost Wipes (Environmental Express).
The Ghost Wipe was chosen for its durability and its use in surface
sampling of other analytes. The samples are analyzed following the
procedure in OSHA Method 421,
using high performance liquid chromatography (HPLC). Glass plates were
used as the ideal surface to check the surface sampler removal
efficiency. The use of a surface that approximates an ideal surface
(extremely smooth and non-porous) minimizes the effect of the surface
on the evaluation of the media. No interactions between the glass
plate and HDI were found. In this evaluation, the media are pre-wetted
with a solution of 50:50 isopropanol:water. After sampling, the
samples were immediately placed in vials containing 5 mL of a
derivatizing reagent solution of 50:50 dimethyl sulfoxide (DMSO):ethyl
acetate and 0.025 M 1-(2-pyridyl) piperazine (1- 2PP). The
derivatizing reagent (1-2PP) reacts with HDI by attaching a
chromaphore to the molecule. This improves the analytical sensitivity
of the method. Also, without the derivatizing reagent, the HDI will
begin to hydrolyze or polymerize and the HDI on the sample will be
lost. A derivatizing reagent solution of 0.025 M 1-2PP in acetonitrile
was initially used. However, other isocyanates that were to be
evaluated did not go into solution in this reagent. To make this
method as uniform and practical as possible for other isocyanate
sampling methods, the derivatizing reagent with DMSO and ethyl acetate
as solvent was used. A study was conducted to investigate the reaction
of HDI with the alcohol and the water in the wetting solution prior to
being derivatized. It was determined that the time interval, from
beginning collection of the sample, until the sample is placed in
contact with the derivatizing reagent should not exceed three minutes.
(Section 4.9)
1.1.2 Toxic effects (This section is for
information only and should not be taken as the basis of OSHA
policy.)
Many dermal exposure studies on animals describe
the ability of HDI to cause contact sensitization or direct irritation
to the skin of laboratory animals.2
Respiratory hypersensitivity has been induced by exposure of
diisocyanates to the skin of laboratory animals.3,
4,
5,
6
Human skin exposure to diisocyanates has resulted in erythema,
eczematous dermatitis, contact eczema characterized by follicular
papules and dermal sensitization.7
A procedures for conducting urinalysis for 1,6-hexamethylene diamine
as an indicator of the biological metabolite of HDI has been
published.9
1.1.3
Workplace exposure
Occupations with the greatest
potential for exposure to HDI are painters and paint spraying machine
operators, aircraft engine mechanics, and aircraft machinists. Other
occupations with potential for exposure to HDI include construction
laborers, chemical technicians, mixing and blending machine operators
in the chemical industry, plumbers, pipe fitters, steam fitters, metal
plating machine operators, miscellaneous machine operators in the
aircraft equipment industry, and production workers and supervisors in
the fabricated structural metal industry.8
1.1.4
Physical properties and descriptive information10
CAS number: |
822-06-0 |
vapor pressure (mmHg): |
0.05 |
IMIS number: |
137711 |
molecular weight: |
168.20 |
flash point (OC): |
135ºC |
boiling point: |
255ºC |
melting point: |
-67ºC |
odor: |
pungent |
appearance: |
Pale yellow liquid |
synonyms: |
1,6-diisocyanatohexane, HDI |
molecular formula: |
OCN-(CH2)6-NCO |
solubility: |
poorly soluble in water, |
specific gravity: |
1.04 g/mL |
|
reacts slowly with water |
LD50, rabbit,
dermal: |
570 µg/kg12
|
|
|
SD50
(sensitization dose) mouse, dermal: 0.088 mg/kg |
LOAEL (Lowest
observable adverse effects level), guinea pig, dermal: 0.1
mg |
This method was evaluated according to the OSHA SLTC
"Evaluation Guidelines for Surface Sampling Methods".13
The Guidelines define analytical parameters, specify required laboratory
tests, statistical calculations and acceptance criteria. The analyte
surface concentrations throughout this method are based on the evaluated
sampling area and analytical concentration parameters.
1.2 Limit defining parameters
1.2.1 Detection limit of the overall procedure
The
detection limit of the overall procedure is 0.29 µg per sample. This
is the smallest amount of HDI spiked on the wipe sampler that will
give a detector response that is significantly different from the
response of the wipe sampler blank. (Section 4.1 )
1.2.2
Reliable quantitation limit
The reliable quantitation limit is
0.96 µg per sample. This is the amount of HDI spiked on the wipe
sampler that will give a detector response that is considered the
lower limit for a precise quantitative measurement. (Section
4.1)
1.2.3 Recovery effects of storage
The recovery of
HDI from spiked samples used in a 15-day storage test remained
above 88.6% when the samples were stored at 22 °C. (Section
4.2)
1.2.4 Surface sampler removal efficiency
The
removal efficiency of Ghost Wipe moistened with 0.5 mL of wetting
reagent for HDI spiked at the target concentration of 340.0
µg/100cm2 is 68.3%. This was the percentage of HDI that
was removed from a glass plate surface, spiked at the target
concentration. (Section 4.3)
1.2.5 Sampling
reproducibility and analytical reproducibility
Six glass plate
surfaces were spiked at the target concentration. Chemists, other than
the one developing the method, conducted sampling on the glass
plate surfaces as described in Section 2. The test was repeated
with a second chemist performing the sampling. The first chemist
was able to achieve a removal efficiency of 60.7%. The second chemist
was able to achieve a removal efficiency of 55.5%. (Section
4.5.1)
Six samples spiked at the target concentration by
liquid injection were submitted for analysis by the OSHA Salt Lake
Technical Center. The samples were analyzed according to a draft
copy of this procedure after 22 days of storage at 22 °C. The average
analytical result was 111% of theoretical. (Section
4.5.2) 2. Sampling
Procedure
All safety practices that apply to the work area being
sampled should be followed. The sampling should be conducted in such
a manner that it will not interfere with work performance or safety. The
derivatizing reagent solution contains DMSO. DMSO is readily absorbed by
the skin and is an excellent vehicle to transfer contaminants dissolved
in it through the skin barrier. Skin contact with the derivatizing
solution containing DMSO should be avoided.
2.1 Apparatus
2.1.1 Chemical resistant gloves; samples are collected
using firm hand pressure to wipe the sampling medium across a
surface. Wear a clean pair of gloves for each sample. The gloves
selected are to be resistant to penetration of the chemical being
sampled and any other chemicals expected to be present. Nitrile
gloves were used for sampling 1,6-hexamethylene diisocyanate based
on a review of glove manufacturer's chemical resistivity and
degradation information.
2.1.2 Labeled 20-mL scintillation
vials with PTFE lined caps, one for each sample, each containing 5
mL of derivatizing reagent solution.
2.1.3 Ghost Wipes, dry,
catalog number SC4050, Environmental Express, Mt. Pleasant,
S.C.
2.1.4 Disposable pipette and bulb, capable of delivering
0.5 mL. Non-sterile graduated pipette, catalog no. 13-711-9A,
Fisher Scientific, Fair Lawn, NJ.
2.1.5 Optional steel or
plastic measuring tape or disposable Sampling Template 10 × 10
cm, catalog number 1010, Environmental Express, Mt. Pleasant,
S.C. 2.2 Reagents
2.2.1 Water, HPLC grade. A Millipore Milli-Q system was
used to prepare the deionized water (DI water) for this
evaluation.
2.2.2 Isopropanol, HPLC grade, Lot No. 001456,
Fisher Scientific, Fair Lawn, NJ.
2.2.3 Ethyl acetate, HPLC
grade, Lot No. 924366, Fisher Scientific, Fair Lawn, NJ.
2.2.4
Dimethyl sulfoxide (DMSO), HPLC grade, Lot No. BB965, Baxter,
Muskegon, MI.
2.2.5 1-(2-Pyridyl) piperazine (1-2PP), Lot No.
09914JU, Aldrich, Milwaukee, WI.
2.2.6 Wetting reagent, 50:50
isopropanol:deionized water (DI) water.
2.2.7 Derivatizing
solution, 50:50 ethyl acetate:DMSO with 0.025 M 1-2PP. 2.3
Shipping media and reagents to the sampling site and reagent
preparation
The media are received from the supplier in packages
containing 100 wipes per package. Wear clean gloves and remove a
sufficient number of wipes to perform the sampling. Remember to include
extra wipes to serve as blanks. Place the wipes in a 5 × 7 in.
recloseable polyethylene zipper bag. Place the remaining wipes in a
large recloseable polyethylene zipper bag. The selected wipes can now be
shipped or taken to the workplace for sampling.
Place a
disposable pipette and bulb, capable of delivering 0.5 mL in a small
recloseable polyethylene zipper bag and ship with the wipe
media.
Prepare the 50:50 isopropanol:DI water wetting
reagent that is needed to moisten the wipe prior to sampling. Place 50.0
mL of the wetting reagent in a labeled bottle and cap
securely.
Prepare the derivatizing solution that is combined with
the wipe sample after sampling. The derivatizing solution consists of
50:50 ethyl acetate:DMSO with 0.025 M 1-2PP.
Place 5.0 mL of
derivatizing solution in each scintillation vial, one for each sample.
Cap the vials securely.
Following current Department of
Transportation (DOT) regulations. Pack the bottle containing the wetting
reagent and the vials containing the derivatizing solution in a shipping
container and label it.
2.4 Sampling technique
Label
a sufficient number of vials containing the derivatizing solution with a
unique number, for the projected sampling needs. Wear clean unpowered
gloves when handling the media.
Prepare a diagram of the area or
rooms to be wipe sampled along with the locations of key
surfaces.
Wear a new pair of clean gloves for each sample to
prevent contamination of future samples as well as oneself. The gloves
selected are to be resistant to penetration of the chemical being
sampled and any other chemicals expected to be present. Nitrile gloves
are recommended for sampling 1,6-hexamethylene diisocyanate based on a
review of glove manufacturer's chemical resistivity and degradation
information.
Record the sample vial number and the location where
the sample is taken. Withdraw a Ghost Wipe from the zipper bag with your
gloved fingers or clean tweezers. Use the disposable pipette to moisten
the medium with 0.5 mL of the wetting reagent.
Depending on the
purpose of the sample, it may be useful to determine the surface loading
of the contamination (e.g., in micrograms of analyte per area). For
these samples, it is necessary to determine the area of the surface
wiped (e.g., 100 cm2). To make this measurement, hold the
measuring tape above the surface (without touching) or place the
disposable sampling template on the surface before sampling. This would
not be necessary for samples taken to simply show the presence of the
contaminant.
The amount of time, from beginning to collect the
sample, until the sample is placed in the vial containing the
derivatizing reagent, should not exceed three minutes. (Section
4.9)
Firm pressure should be applied when wiping. Start at the
outside edge and progress toward the center making concentric squares of
decreasing size. Fold the medium with the contaminant side inward and
repeat.
Without allowing the medium to come into contact with any
other surface, fold the medium with the exposed side inward. Place the
medium in a sample vial containing the derivatizing solution, cap and
shake vigorously for one minute. Place a number corresponding the sample
to the location on the diagram. Include notes with the sketch giving any
further description that may prove useful when evaluating the sample
results (e.g., a description of the surface sampled, such as: pencil,
doorknob, safety glasses, lunch table, inside respirator, employee's
names, etc.).
Submit at least one blank wipe medium, treated in
the same fashion as the wipe samples, but without wiping.
Record
sample location, employees names, surface area (if pertinent), work
description, PPE, and any other necessary information, along with any
potential interferences on the OSHA-91A form.
Submit the samples
to the OSHA Salt Lake Technical Center together with OSHA-91A forms as
soon as possible after sampling. Ship any bulk samples separate from the
surface samples. Package, label, and ship samples according to
current DOT regulations.
2.5 Extraction efficiency (Section
4.4)
It is the responsibility of each analytical laboratory to
determine the surface sample extraction efficiency because the wipe
sampling media, reagents and laboratory techniques may be different than
the those listed in this evaluation and influence the results.
2.5.1 The mean extraction efficiency for 1,6-hexamethylene
diisocyanate from Ghost Wipes over the range of RQL to 10 times the
target concentration (0.99 to 3400 µg per sample) was
96.8%.
2.5.2 Extracted samples
remain stable for at least 24 h.2.6 Interferences,
sampling
Suspected interferences should be reported to the
laboratory with submitted samples.
Blank wipe sampling media was
moistened with the wetting reagent, placed in vials and analyzed.
Additional samples were prepared by wiping glass plates with wipe
sampling media moistened with the wetting reagent. The surfaces were not
spiked with HDI. The samples were analyzed. No significant interferences
were found. (Section 4.6)3.
Analytical Procedure
Adhere to the rules set down in your Chemical
Hygiene Plan14.
Avoid skin contact and inhalation of all chemicals and review all
appropriate MSDSs before beginning the analytical procedure.
This
analysis closely follows the analytical procedure in OSHA Method
42.15
3.1 Apparatus
3.1.1 A high performance liquid chromatograph (HPLC)
equipped with fluorescence (FL) and ultraviolet (UV) detectors,
liquid chromatograph pump, manual or automatic injector, and chart
recorder. A Hewlett-Packard Series 1050 HPLC equipped with a UV
detctor and a Kratos Spectroflow 980 FL detector was used in this
evaluation.
3.1.2 LC column capable of separating diisocyanate
derivatives. A 25-cm × 4.6-mm i.d. Alltech Econosphere CN (5-µm)
column was used during this evaluation.
3.1.3 An
electronic integrator, or some other suitable method of measuring
detector response. A Waters Corporation Millennium32
(version 3.20) data system was used in this evaluation.
3.1.4
Vials, 2-mL with PTFE-lined caps.
3.1.5 Volumetric flasks,
pipets, and syringes.
3.1.6 Micro-analytical balance used to
weigh standard preparations.
3.1.7 Centrifuge. 3.2
Reagents
3.2.1 Acetonitrile (ACN), HPLC grade, Lot No. 012683,
Fisher Scientific, Fair Lawn, NJ.
3.2.2 Water, HPLC grade. A
Millipore Milli-Q system was used to prepare the water for this
evaluation.
3.2.3 Ethyl acetate, HPLC grade, Lot No. 924366,
Fisher Scientific, Fair Lawn, NJ.
3.2.4 Dimethyl
sulfoxide (DMSO), HPLC grade, Lot No. BB965, Baxter, Muskegon,
MI.
3.2.5 1,6-Hexamethyl diisocyanate (HDI), Lot No.
01104EU, Aldrich, Milwaukee, WI.
3.2.6 1-(2-pyridyl) piperazine
(1-2PP), Lot No. 09914JU, Aldrich, Milwaukee, WI.
3.2.7
Ammonium acetate, Lot No. 897484, Fisher Scientific, Fair Lawn,
NJ.
3.2.8 Phosphoric acid, Lot No. 025821, Baker, Phillipsburg,
NJ.
3.2.9
N,N'-1,6-hexanediylbis[4-(2-pyridinyl)-1-piperazinecarboxyamide],
(1-(2-pyridyl)piperazine derivative of HDI), U. S. Department of Labor
OSHA Technical Center Salt Lake City, UT. (An external source
is: Product number 48146, Supelco, Bellefonte, PA.) 3.3
Standard preparation
3.3.1 All applicable Quality Assurance procedures and
accreditation requirements should be observed.
3.3.2 A stock
standard solution is prepared by dissolving derivatized HDI in DMSO.
The derivatized HDI may be purchased or prepared following Section
3.3.1 of OSHA Method 4216.
The ratio of the molecular weights of HDI to the HDI derivative is
0.340. Use this factor to express the mass of HDI derivative as the
mass of HDI. All dilutions of the stock solutions are made with 90:10
ACN:DMSO to arrive at the working range.
3.3.3 Bracket sample
concentrations with standard concentrations. If, upon analysis,
sample concentrations fall outside the range of prepared
standards, prepare and analyze additional standards to confirm
instrument response, or dilute high samples with the 90:10 ACN:DMSO
dilution solution. 3.4 Sample preparation
3.4.1 The surface samples are received in 20-mL vials
containing the wipe media and 5.0 mL of derivatizing reagent solution.
The vials are placed in a centrifuge that has been set at 2500 rpm for
4 min.
3.4.2 Remove an aliquot of approximately 1 mL and place
into an appropriate autosampler vial and seal with a PTFE-lined cap.
3.5 Analysis
3.5.1 HPLC conditions
column: |
25-cm × 4.6-mm i.d. Alltech
Econosphere CN (5 µm). |
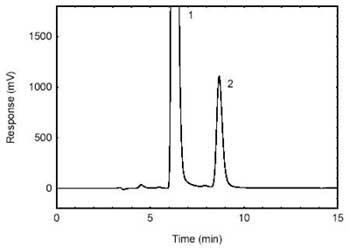 |
mobile phase: |
40:60 ACN:water, 0.02 M ammonium
acetate adjusted to pH 5.9 with phosphoric acid. |
flow rate: |
1.0 mL/min for 15 min |
FL detector: |
240 nm excitation, 370 nm
emission |
UV detector: |
254 nm |
injection size: |
10 µL |
Figure 3.5.1.
Chromatogram obtained from the samples spiked at the target
concentration and diluted 1/50. (1- excess 1-2PP (derivatizing
reagent); 2-HDI. |
retention time: |
9 min |
chromatogram: |
Figure
3.5.1 |
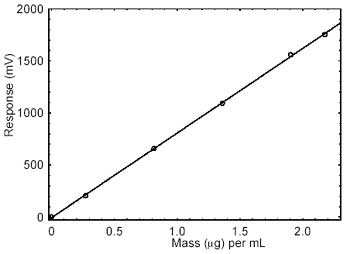 |
Figure 3.5.2. Calibration curve
of HDI. (Y=813X - 6.30) | 3.5.2 An external standard (ESTD) calibration procedure
is used to prepare a calibration curve using at least 2 stock
standards from which dilutions are made. The calibration curve is
prepared daily. The samples are bracketed with analytical
standards. 3.6 Interferences
(analytical)
3.6.1 Any compound that produces a fluorescence or UV
detector response and has a similar retention time as HDI is a
potential interference. If any potential interferences were reported,
they should be considered before samples are extracted. Generally,
chromatographic conditions can be altered to separate an interference
from the analyte. Material Safety Data Sheets (MSDS) identify solvents
prevalent in spray painting operations. Three solvents commonly found
were separately added to individual media that had been placed in
vials, moistened with the wetting reagent and spiked with HDI at the
target level. The samples were prepared and analyzed. Benzaldehyde and
2,4-toluene diisocyanate were also tested as potential interferences
in the same manner. Neither the solvents or the chemicals caused a
discernable interference. (Section 4.6)
3.6.2 When necessary,
the identity of an analyte peak may be confirmed with additional
analytical data. An absorbance response ratio of UV detector response
to fluorescence detector response is determined. The response ratio of
samples and standards of similar concentration are compared. (Section
4.8) 3.7 Calculations
The amount of HDI per sampler
is obtained from the appropriate calibration curve in terms of
micrograms per mL, uncorrected for extraction efficiency. This amount is
then adjusted by subtracting the amount (if any) found on the blank and
corrected for extraction efficiency. Correct for the 5.0 mL of
derivatizing solution that was present in the samples when they were
received and any dilutions performed. Perform the calculation using the
following formula.
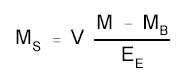 |
where |
MS is the mass
of HDI recovered from the sampled surface (µg) |
|
V is the volume of the derivatizing
solution and any dilutions (mL) |
|
M is micrograms per mL from the
sample derivatizing solution |
|
MB is micrograms per mL
from the blank derivatizing solution |
|
EE is the extraction
efficiency | The amount
may be expressed as micrograms HDI per 100 cm2 if the surface
area that was sampled was provided, by using the following
formula.
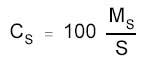 |
where |
MS is the mass
on the sampled surface (µg) |
|
CS is the mass (in µg) of
HDI per 100 cm2 |
|
S is the surface area sampled
(cm2) |
|
100 is 100
cm2 | The
surface that was sampled may be less ideal (more porous, less smooth)
than the surface that was used to evaluate the removal efficiency of the
sampling media. In this circumstance, the media will remove the surface
contaminant less effectively. There may be significant amounts of
contaminant remaining on the surface after sampling. Nevertheless, the
amount found in the sample indicates that at least this amount of HDI
was present on the surface.4.
Backup Data
General background information about the determination
of detection limits and reproducibility of the overall procedure is found
in the "Evaluation Guidelines for Surface Sampling Methods".17
4.1 Detection limit of the overall procedure (DLOP) and
reliable quantitation limit (RQL)
Table
4.1 Detection Limit of the Overall Procedure |
|
mass per
sample (µg) |
response (mV) |
|
0 |
35 |
0.66 |
102 |
1.32 |
193 |
1.98 |
304 |
2.64 |
400 |
3.30 |
506 |
| The DLOP is measured as
mass per sample. Five samplers were moistened with 0.5 mL wetting
solution and spiked with equal descending increments of analyte, such
that the highest sampler loading was 3.30 g/sample. 5.0 mL of
derivatizing reagent was added to these spiked samplers, and also a
sample blank. The samplers were analyzed with the recommended analytical
parameters, and the data obtained used to calculate the required
parameters (standard error of estimate and the slope) for the
calculation of the DLOP. The data is presented in Table 4.1.
Values of 145.5 and 14.0 were obtained for the slope and standard error
of estimate, respectively. The DLOP was calculated to be 0.29
µg/sample.
The RQL is considered the lower limit for precise
quantitative measurements. It is determined from the regression line
parameters obtained for the calculation of the DLOP, providing 75% to
125% of the analyte is recovered. The RQL is 0.962 µg/sample. Average
recovery at this level is 90.5%.
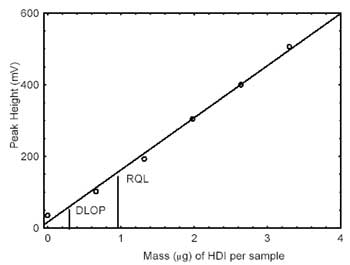 |
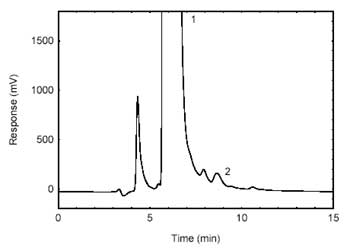 |
Figure 4.1.1. Plot of data to
determine the DLOP/RQL. (Y=146X + 16.7) |
Figure 4.1.2. Chromatogram of the
RQL. (1)- derivatizing reagent; (2)
-HDI. | 4.2 Storage
tests
Storage samples were prepared by spiking Ghost Wipes, that
had been moistened with the wetting solution, with HDI at the target
concentration. Samples were immediately placed in vials containing the
derivatizing reagent. Twenty-one storage samples were prepared. Three
samples were analyzed on the day prepared. Nine of the samples were
stored at reduced temperature (4 °C) and the other nine were stored in a
closed drawer at ambient temperature (about 22 °C). At about 5-day
intervals, three samples were selected from each of the two storage sets
and analyzed. Sample results were not corrected for extraction
efficiency.
Table
4.2 Storage Test for HDI |
|
time (days) |
ambient
storage recovery (%) |
refrigerated
storage recovery (%) |
|
0 |
93.1 |
69.7 |
92.4 |
93.1 |
96.7 |
92.4 |
5 |
92.3 |
91.1 |
92.9 |
94.3 |
92.7 |
93.9 |
11 |
85.1 |
85.9 |
87.4 |
87.4 |
91.5 |
89.4 |
15 |
90.6 |
90.9 |
90.7 |
90.7 |
92.3 |
89.4 |
|
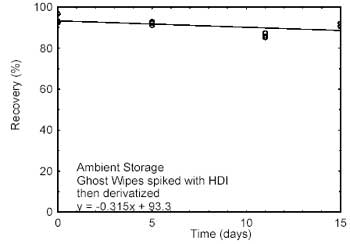 |
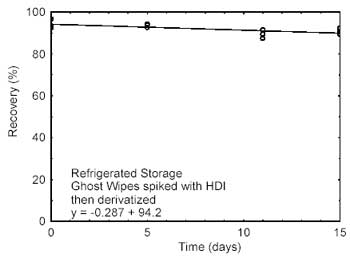 |
Figure 4.2.1. Ambient storage test
for HDI. |
Figure 4.2.2. Refrigerated Storage
test for HDI. | 4.3
Sampler removal efficiency
Table
4.3 Sampler Removal Efficiency Data for HDI on Ghost
Wipes |
|
theoretical (µg/surface) |
recovered (µg/sample) |
recovery (%) |
|
340 |
220 |
64.7 |
340 |
246 |
72.3 |
340 |
244 |
71.7 |
340 |
219 |
64.4 |
340 |
228 |
67.1 |
340 |
236 |
69.3 |
| Six glass surfaces
were spiked at the target concentration of HDI, 340 µg /100
cm2. Samples were collected from each surface using the
technique described in Section 2.4 and analyzed. Sample results were
corrected for extraction efficiency. The results are shown in Table
4.3.
4.4 Extraction efficiency and stability of extracted
samples
The extraction efficiency is dependent on the solvents
used in the derivatizing solution.
4.4.1 Extraction efficiency
The extraction
efficiencies of HDI were determined by liquid-spiking Ghost Wipes with
the HDI at concentrations ranging from the RQL to 10 times the target
concentration. The sample media was placed in vials and moistened with
the wetting solution. Each sampler was then spiked and the
derivatizing reagent solution was added. Four samplers at each
concentration were prepared. The samples were placed on a rotator for
an hour. These samples were stored overnight at ambient temperature
and then analyzed. The mean extraction efficiency over the working
range of the RQL to 10 times the target concentration is 96.8%. Note
that extraction efficiency also accounts for the additional volume of
the wetting reagent.
Table
4.4.1 Extraction Efficiency of HDI from Ghost Wipe |
|
level |
sample
number |
× target concn |
µg per sample |
1 |
2 |
3 |
4 |
mean |
|
RQL |
0.99 |
90.2 |
88.2 |
92.0 |
91.5 |
90.5 |
0.1 |
34.0 |
100.1 |
100.9 |
98.8 |
94.8 |
98.7 |
1.0 |
340 |
98.6 |
98.7 |
97.9 |
97.5 |
98.1 |
10.0 |
3400 |
99.2 |
100.9 |
100.1 |
99.2 |
99.9 |
| 4.4.2 Stability of
extracted samples
The stability of extracted samples was
investigated by re-analyzing the four target concentration samples 24
h after initial analysis. After the original analysis, two of the
auto- sampler vials were recapped with new septa, while the
remaining two retained their punctured septa. The samples were
re-analyzed with fresh standards. The average percent change was 1.1%
for the samples that were resealed and 1.2% for those that were stored
with their septa punctured. The septum was punctured 3 times for each
injection.
Table
4.4.2 Stability of Extracted Samples for HDI |
|
punctured
septa replaced |
punctured
septa retained |
initial (%) |
after one
day (%) |
difference (%) |
initial (%) |
after one
day (%) |
difference (%) |
|
98.6 |
100.4 |
1.8 |
97.9 |
98.7 |
0.8 |
98.7 |
98.3 |
0.4 |
97.5 |
99.1 |
1.6 |
| 4.5
Reproducibility
4.5.1 Six glass surfaces were spiked at the target level
of 340 µg. Two chemists, other than the one developing the method,
conducted sampling on the glass surfaces as described in Section
2. The test was repeated with a second chemist performing the
sampling. Sample results were corrected for extraction
efficiency.
Table
4.5.1.1 Sampling Reproducibility Data for HDI on Ghost
Wipe, 1st Chemist |
|
Table
4.5.1.2 Sampling Reproducibility Data for HDI on Ghost
Wipe, 2nd Chemist |
|
|
|
theoretical (µg/surface) |
recovered (µg/sample) |
recovery (%) |
|
theoretical (µg/surface) |
recovered (µg/sample) |
recovery (%) |
|
|
|
340 |
176 |
51.9 |
|
340 |
200 |
58.8 |
340 |
212 |
62.3 |
|
340 |
176 |
51.7 |
340 |
209 |
61.4 |
|
340 |
212 |
62.4 |
340 |
208 |
61.2 |
|
340 |
177 |
52.0 |
340 |
222 |
65.4 |
|
340 |
176 |
517 |
340 |
212 |
62.2 |
|
340 |
191 |
56.1 |
|
|
|
Table
4.5.2 Analytical Reproducibility Data for HDI on Ghost
Wipes |
|
theoretical (µg/surface) |
recovered (µg/sample) |
recovery (%) |
|
340 |
382 |
112 |
340 |
370 |
109 |
340 |
375 |
110 |
340 |
365 |
107 |
340 |
393 |
116 |
340 |
377 |
111 |
|
4.5.2 Six samples were prepared by spiking media in the
same manner that was used in the preparation of samples for the
storage study. The samples were submitted to the OSHA SLTC for
analysis. The samples were analyzed after being stored for 22
days at 22 °C. Sample results were corrected for extraction
efficiency.
4.6 Interferences
4.6.1 Media
Tests were conducted to determine
interference due to contamination of the prepared media. Two
blank wipe sampling media were placed in vials, moistened with the
recommended solvent. The derivatizing reagent solution was added and
the samples were processed and analyzed.
Table
4.6.1 Interference to the Analysis of HDI from the Media
or Surface (µg found) |
|
sample |
1 |
2 |
mean |
|
blank |
0.00 |
0.29 |
0.14 |
from surface |
0.00 |
0.00 |
0.00 |
| Two additional samples
were prepared by wiping the same type of surface that was used for the
removal efficiency test (glass plate) with media moistened with 50:50
isopropanol:DI water. The surfaces were not spiked with HDI. The
samples were placed in vials containing the derivatizing reagent
solution, processed and analyzed. The results are shown in Table
4.6.1.
4.6.2 Tests were conducted to determine the
effects of potential interference from three solvents that are
commonly found in auto-body repair shops (toluene, 2-heptanone and
petroleum distillate) and also, two additional chemicals (benzaldehyde
and 2,4-toluene diisocyanate). Three samplers were prepared for
each compound tested. The sample media was placed in vials and
moistened with 0.5 mL of the wetting solution. Each sampler was then
spiked with 340 µg HDI and 5.0 mL of the derivatizing reagent. A
potential interfering compound was then added. The samples were
processed and analyzed. The amounts of interfering compound added and
the results are shown in Table 4.6.2. None of the compounds tested
caused a significant interference.
Table
4.6.2 Interference to the Analysis of HDI, with an
interferant compound added. (µg found, not corrected for
extraction efficiency) |
|
potential
interferant |
amount
of interferant spiked (µg) |
amount of
HDI spiked (µg) |
amount of
HDI recovered |
1 |
2 |
3 |
mean |
|
toluene |
173400 |
340 |
319 |
320 |
315 |
318 |
2-heptanone |
164000 |
340 |
305 |
307 |
305 |
306 |
petroleum
distillate |
145300 |
340 |
309 |
307 |
311 |
309 |
benzaldehyde |
650 |
340 |
297 |
318 |
313 |
309 |
2,4-TDI |
650 |
340 |
312 |
320 |
318 |
317 |
| 4.7 Analyte
confirmation or qualitative analysis
Diisocyanate qualitative
analysis confirmation is not performed by GC/MS because the derivatized
diisocyanate is not sufficiently volatile for gas chromatography.
Diisocyanate may be confirmed by a peak ratio technique. The analysis is
conducted with fluorescence and UV detectors in series. A ratio is
established between fluorescence detector response and UV detector
response of a standard that is the approximate concentration of the
sample. A similar ratio is established between fluorescence detector
response and UV detector response of the sample. The ratio of the sample
is compared to the ratio of the standard for diisocyanate confirmation.
Any required laboratory confirmation criteria must be met before the
analyte confirmation is reported.
4.8 Derivatizing reagent
storage test
Table
4.8 Derivatizing Reagent Storage Test (60 days) |
|
×
target concn |
ambient
storage recovery (%) |
refrigerated
storage recovery (%) |
|
0.1 |
93.4 |
88.4 |
1.0 |
96.4 |
97.4 |
10.0 |
99.2 |
99.6 |
| Derivatizing reagent
solution was prepared as in Section 2.3 and divided into two portions.
One portion was placed in a refrigerator. The other portion was placed
in a fire cabinet at ambient temperature. After sixty days fresh
derivatizing reagent was also prepared. Standards were prepared at 0.1,
1.0, and 10 times the target concentration using fresh derivatizing
reagent. Spiked samples were prepared at 0.1, 1.0, and 10 times the
target concentration using the ambient and refrigerated derivatizing
reagent solutions. Excess derivatizing reagent peak was noted on the
chromatograms for all samples and standards. Samples prepared with the
derivatizing reagent solution that was stored at ambient temperatures
for sixty days gave average results that were 93.4%, 96.4%, 99.2% of the
0.1, 1.0, and 10 times the target concentration, respectively. Samples
prepared with the derivatizing reagent solution that was stored at
refrigerated temperatures for sixty days gave average results that were
88.4%, 97.4%, 99.6% of the 0.1, 1.0, and 10 times the target
concentration, respectively. The results are shown in Table 4.8. The
effect of light on the derivatizing solution was not tested. The
derivatizing reagent solution may be stored in a dark place with
adequate ventilation, at room temperature for at least two months. No
refrigeration is required for storage.
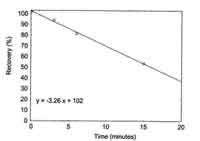 |
Figure 4.9. Average recovery of HDI
at timed reaction intervals with wetting
solution. | 4.9
Reaction time study
Many texts
and articles indicate that water and alcohols will react with
isocyanates. One published study determined that the reaction rate of
water with isocyanates was at least 5 orders of magnitude (100,000)
times slower than the reaction rate of the derivatizing reagent,
1,2-pyridyl piperazine with isocyanates.18
The use of a wetting solution consisting of 50:50 isopropanol:water in
this method required a reaction rate test to be performed. The test was
to determine whether the water and isopropanol in the wetting reagent
reacts with HDI rapidly enough to be a concern, relative to the amount
of time it takes to collect a sample and deposit it into a vial
containing the derivatizing reagent. Vials containing 0.5 mL 50:50
isopropanol:water (wetting solution) were spiked with HDI at 1.0, 0.5
and 0.1 times the target concentration. Two vial at each concentration
were prepared. Five milliliters of derivatizing reagent was added as
quickly as possible. The vials were capped and agitated to insure
mixing. The procedure was repeated three more times, except intervals of
3, 6 and 15 minutes were allowed to pass before adding the derivatizing
reagent. Standards bracketing the concentrations were prepared with the
same spiking solution in a similar manner, with no wetting solution, but
in 5.5 mL of derivatizing reagent. Analysis was conducted and the result
are presented in Table 4.9. The concentration of the spike did not
appear to effect the recovery but the amount of time the spike was
allowed to remain in the wetting reagent before being derivatized did
effect the recovery. The percent recovery for all concentrations was
averaged for each reaction time interval and plotted against time in
minutes (Figure 4.9). Using the equation of the line, the recovery can
be predicted for a given reaction time. The average recovery at 3.5
minutes is 90.6%. Based on this information, the amount of time it takes
to collect a sample is important. The time interval, from beginning to
collect the sample, until the sample is placed in the vial containing
the derivatizing reagent, should not exceed three minutes.
Table
4.9 Percent Recovery of HDI After Timed Reaction Intervals With
the Wetting Solution |
|
µg spiked |
"Immediate" |
3 minutes |
6 minutes |
15 minutes |
|
34.0 |
105.4 |
97.7 |
89.0 |
62.5 |
34.0 |
105.6 |
100.3 |
87.2 |
59.2 |
170.0 |
99.7 |
92.2 |
78.3 |
49.8 |
170.0 |
97.9 |
88.9 |
77.3 |
50.4 |
340.0 |
101.6 |
92.5 |
79.5 |
50.4 |
340.0 |
101.7 |
92.4 |
77.9 |
49.5 |
Average |
101.9 |
94.0 |
81.5 |
53.7 |
|
References:
1.
Diisocyanates, 1,6-Hexamethylene Diisocyanate (HDI),
Tolune-2,6-Diisocyanate, Tolune-2,4-Diisocyanate, Method 42, 1989; org042/org042.html,
(accessed May 2000).
2. Toxicological Profile for Hexamethylene Diisocyanate,
U.S. Department of Health and Human Services, Public Health Service,
Agency for Toxic Substances and Disease Registry, Atlanta, GA, 1998, pp
59-67.
3. Rattray, N., et al. Induction of
Respiratory Hypersensitivity to Diphenylmethane-4-4' diisocyanate (MDI) in
Guinea Pigs. Influence of Route Exposure. Toxicology 1994, 88, pp 15-30.
4. Karol, M. H., et
al. Dermal Contact with Tolune Diisocyanate (TDI) Procedures Respiratory
Tract Hypersensitivity in Guinea Pigs, Toxicology and
Applied Pharmacology 1981, 58, pp 221-230.
5. Kimber, I. The
Role of the Skin in the Development of Chemical Respiratory
Hypersensitivity, Toxicology Letters 1996, 86, pp 89-92.
6. Bickis, U. Investigation of Dermally Induced Airway
Hyperreactivity to Tolune Diisocyanates in Guinea Pigs. Ph.D. thesis,
Queen's University, Kingston, Canada, 1994.
7. Criteria for a Recommended Standard... Occupational Exposure
to Diisocyanate; DHEW (NIOSH) Publ. No. 78-215; U.S. Department if
Health, Education and Welfare, Public Health Service, Center for Disease
Control, National Institute for Occupational Safety and Health, U.S.
Government Printing Office: Washington DC, 1978, pp 35-36.
8. Maitre A., et al. Urinary Hexane Diamine as an Indicator of
Occupational Exposure to Hexamethylene Diisocyanate, International Archives of Occupational and Environmental
Health 1996, 69,
pp 65-68.
9. National Occupational Exposure Survey;
U.S. Department of Health, Education and Welfare, Public Health Service,
Center for Disease Control, National Institute for Occupational Safety and
Health, Cincinnati, OH, 1989.
10. Toxicological Profile for Hexamethylene Diisocyanate,
U.S. Department of Health and Human Services, Public Health Service,
Agency for Toxic Substances and Disease Registry, Atlanta, GA, 1998, pp
100-102.
11. Chemical Sampling Information,
Hexamethylene Diisocyanate, http://www.osha-slc.gov/dts/chemicalsampling/data/CH_245198.html,
(accessed May 2001).
12. RTECS 2000,
1,6-Diisocyanate Hexane, Registry of Toxic Effects of Chemical Substances,
U.S. Department of Health and Human Services, National Institute for
Occupational Safety and Health, Washington, DC, December 2000.
13. Lawrence, R. Evaluation Guidelines for
Surface Sampling Methods; OSHA Salt Lake Technical Center, U.S.
Department of Labor: Salt Lake City , UT, 2001 (unpublished).
14. Occupational Exposure to Chemicals in Laboratories. Code
of Federal Regulations, Part 1910.1450, Title 29, 1998;
http://www.osha.gov/OshaStd_data/1910_1450_APP_A.html, (accessed May
2000)
15. Diisocyanates, 1,6-Hexamethylene
Diisocyanate (HDI), Toluene-2.6-Diisocyanate, Toluene-2.4-Diisocyanate,
Method 42, 1989; org042/org042.html,
(accessed May 2000).
16. Diisocyanates,
1,6-Hexamethylene Diisocyanate (HDI), Toluene-2.6-Diisocyanate,
Toluene-2.4-Diisocyanate, Method 42, 1989; org042/org042.html,
(accessed May 2000).
17. Lawrence, R. Evaluation Guidelines for Surface Sampling Methods;
OSHA Salt Lake Technical Center, U.S. Department of Labor: Salt Lake City
, UT, 2000, unpublished.
18. Wu, W., et al.
Application of Tryptamine as a Derivatizing Agent for Airborne Isocyanate
Determination part 4. Evaluation of Major High-performance Liquid
Chromatographic Methods Regarding Airborne Isocyanate Determination With
Specific Investigation of the Competitive Rate of Derivatization, Analyst 1991, 119, p
24.
|