1. General Discussion
1.1 Background
1.1.1 History of procedure
The NIOSH Method
270 (Ref 5.1) is not convenient for the industrial hygienist in
the field, as the ethanolamine is collected on silica gel tubes and
the amine is stabilized by spiking the tubes with concentrated HCl
after sampling. The sample is desorbed, neutralized, and then
derivatized with benzaldehyde. Direct analysis of
the ethanolamine is difficult for the chemist due to poor
chromatography and carryover problems. A sampling tube containing
XAD-2 resin coated with 10% NITC by weight to derivatize and stabilize
the amine had good desorption, retention and storage
efficiencies.
1.1.2 Potential workplace exposure (Ref
5.2) Ethanolamine is used to remove CO2 and
H2S from natural gas and other gases. Ethanolamine is used
as an ingredient in many products: in the synthesis of surface active
agents, in polishes, in hair waving solutions, in emulsifiers, as a
softening agent for hides, and as a dispersing agent for agricultural
chemicals.
1.1.3 Toxic Effects (This section is for
information purposes and should not be taken as the basis for OSHA
policy.)
The TLV of ethanolamine is based mainly on skin
toxicity, causing redness, swelling, and lesions. Dogs, rats, and
guinea pigs exposed to 100 ppm for 30 days were apathetic, had poor
appetites, and had dermal effects ranging from ulceration to hair
loss. Dogs exposed to 5 ppm for 90 days had skin irritation, weight
loss, and a decrease in alertness and activity. (Ref. 5.3)
1.1.4 Physical properties (Ref 5.2):
Synonyms: |
2-aminoethanol;
2-hydroxyethylamine; ethylolamine; colamine |
Molecular weight: |
61.08 |
Density: |
1.0117 |
Freezing point: |
10.30°C |
Odor: |
ammoniacal odor |
Color: |
light yellow liquid |
Molecular formula: |
C2 H7
NO |
Flash point: |
91°C (195°F) |
CAS: |
141-43-5 |
IMIS: |
1030 |
RTECS: |
KJ5775000 |
Structure: |
|
1.2 Limit defining
parameters
1.2.1 The detection limit of the analytical procedure is
8.09 ng per injection. This is the smallest amount which could be
detected under normal operating conditions.
1.2.2 The
overall detection limit is 0.06 ppm based on a 10-liter air volume, a
desorption volume of 2 mL, and desorption efficiency of 100%. All ppm
values stated in this method are based on a 10-L air volume and 2-mL
desorption volume.
1.3 Advantages
1.3.1 The sampling procedure is
convenient.
1.3.2 The analytical method is reproducible
and sensitive.
1.3.3 Reanalysis of samples is
possible.
1.3.4 It may be possible to analyze other
compounds at the same time.
1.3.5 Interferences may be
avoided by proper selection of column and LC
parameters.
1.4
Disadvantages
Sampling tubes are not available
commercially and must be prepared by the
laboratory. 2.
Sampling procedure
2.1 Apparatus
2.1.1 A calibrated personal sampling
pump, the flow of which can be determined within ±5% at the
recommended flow.
2.1.2 Sampling tubes containing XAD-2
resin coated with 10% NITC by weight. A sampling tube consists of two
sections of coated XAD-2 resin separated by a glass wool plug. The
front section contains 80-mg coated sorbent and the 40-mg backup
section. The sections are held in place with glass wool plugs in a
glass tube 4-mm ID × 70-mm length.
The adsorbent is
prepared by coating commercially purified 16/50 mesh XAD-2 (Supelco)
with 10% NITC by weight using methylene chloride as as a solvent. The
solvent is removed by rotary evaporation (Ref 5.4)
2.1.3
Lengths of flexible tubing are needed to connect the sampling tubes to
the sampling pumps.
2.1.4 Two plastic caps and an OSHA Form-21
are needed to seal each sampling tube after
sampling.
2.2 Sampling
technique
2.2.1 The ends of the sampling tube
are opened immediately before sampling.
2.2.2 Connect the
sampling tube to the sampling pump with flexible tubing with the
smaller section towards the pump.
2.2.3 Tubes
should be placed in a vertical position to minimize channeling.
2.2.4 Air being sampled should not pass through any hose or
tubing before entering the sampling tube.
2.2.5 Seal the
sampling tube with plastic caps immediately after sampling. Seal each
sample lengthwise with OSHA Form-21. 2.2.6 With
each batch of samples, submit at least one blank tube from the same
lot used for air samples. This tube should be subjected
to exactly the same handling as the samples (break ends,
seal, & transport) except that no air is drawn through it.
2.2.7 Transport the samples (and corresponding paperwork) to
the lab for analysis.
2.2.8 Bulks submitted for analysis
must be shipped in a container separate from the
samples.
2.3 Desorption efficiency
Sampling tubes were spiked with 0.65, 1.62,
3.24, and 6.48 ppm, ethanolamine. They were allowed to equilibrate at
room temperature overnight. They were opened, each section placed into a
4-mL vial, and 2-mL dimethylformamide was added. They were allowed
to desorb for 30 minutes with occasional shaking, and analyzed by HPLC.
The desorption efficiency averaged 100% (Table
2.3).
Table
2.3 Desorption efficiency |
Tube# |
% Recovered 161.8 µg
6.48 ppm |
% Recovered 80.9
µg 3.24 ppm |
% Recovered 40.45 µg
1.62 ppm |
% Recovered 16.18 µg
0.65 ppm |
|
|
|
|
|
1 |
96.1 |
100 |
103 |
101 |
2 |
99.1 |
100 |
95.3 |
98.8 |
3 |
102 |
101 |
97.3 |
101 |
4 |
97.7 |
100 |
98.9 |
101 |
5 |
103 |
101 |
101 |
101 |
6 |
102 |
101 |
101 |
98.0 |
|
|
|
|
|
average |
100 |
101 |
99.4 |
100 |
|
|
|
|
|
overall
average |
100 |
|
|
standard
deviation |
±2.00 |
|
|
2.4 Retention efficiency
Sampling tubes
were spiked with 161.8 µg (6.48 ppm) ethanolamine, and 10 liters of
humid air (93% RH) were drawn through them. They were desorbed and
analyzed by HPLC. There was no ethanolamine found on the backup portions
of the sampling tubes (Table 2.4).
Table
2.4 Retention Efficiency |
Tube # |
% Recovered 'A' |
% Recovered 'B' |
% Total |
|
|
|
|
1 |
103 |
0 |
103 |
2 |
105 |
0 |
105 |
3 |
104 |
0 |
104 |
4 |
97 |
0 |
97 |
5 |
101 |
0 |
101 |
6 |
100 |
0 |
100 |
|
|
|
|
average |
|
|
102 |
|
|
|
|
2.5 Storage
Sampling tubes were
spiked with 80.9 µg (3.24 ppm) ethanolamine and stored at room
temperature until they were desorbed and analyzed. The recoveries
remained above 98.1% for the 16-day storage period (Table
2.5).
Table
2.5 Storage Study |
Day |
% Recovered |
4 |
101 |
4 |
99.3 |
4 |
101 |
8 |
98.1 |
8 |
98.4 |
8 |
100 |
16 |
101 |
16 |
103 |
16 |
102 |
2.6 Precision
Precision was calculated
using the area counts from six injections of each standard at
concentrations of 0.405, 20.2, 40.5, and 80.9 µg/ml ethanolamine. (Table
2.6).
Table 2.6 Precision |
Injection
number |
80.94 µg/mL
6.48 ppm |
40.47 µg/mL
3.2 ppm |
20.23 µg/mL
1.62 ppm |
0.4047
µg/mL 0.32 ppm |
1 |
4840660 |
2497430 |
1249926 |
266774 |
2 |
4843388 |
2450287 |
1251863 |
259756 |
3 |
4847381 |
2454235 |
1253753 |
259865 |
4 |
4854116 |
2457850 |
1249499 |
254630 |
5 |
4845563 |
2454948 |
1254341 |
250966 |
6 |
4839621 |
2447595 |
1256576 |
254752 |
average |
4845122 |
2460391 |
1252660 |
257791 |
standard
deviation |
±5280 |
±18502 |
±2737 |
±5562 |
CV |
0.00109 |
0.00752 |
0.00218 |
0.0216 |
Pooled CV |
|
6.809 |
|
|

A(1),A(2),A(3),A(4) = # of injections at each
level
CV1,CV2,CV3,CV4 = Coefficients at each level
2.7 Air volume and sampling rate studied
2.7.1 The air volume studied was 10
liters.
2.7.2 The sampling rate studied was 0.1 liters
per minute.
2.8 Interferences
(sampling)
2.8.1 Compounds which react with the
derivatizing reagent may decrease the capacity for the analyte.
2.8.2 Suspected interferences should be listed on sample data
sheets.
2.9 Safety precautions
2.9.1 Sampling equipment should be
placed on an employee in a manner that does not interfere with work
performance or safety.
2.9.2 Safety glasses should be
worn at all times.
2.9.3 Follow all safety practices
that apply to the workplace being
sampled. 3. Analytical
method
3.1 Apparatus
3.1.1 Liquid chromatograph equipped
with an ultraviolet detector capable of monitoring 254 and 280
nm. The response is most sensitive at 254 nm. For this study a Waters
M-6000A pump was used with a Waters 440 Absorbance Detector.
3.1.2 LC column capable of separating the analyte from any
interferences. A l0-µm Zorbax CN, 25 cm × 4.6 mm ID, was used for this
study.
3.1.3 An electronic integrator or some other
suitable method of measuring peak areas.
3.1.4 Four
milliliter vials with Teflon-lined caps for sample
desorption.
3.1.5 A 20 µL syringe or other convenient
size for sample injection, or an autosampler that can inject 15 µL.
Injections were made with a Waters WISP 710 automatic sample injection
module in this study.
3.1.6 A dispenser or pipet capable
of delivering 2.0 mL dimethylformamide.
3.1.7 Volumetric
flasks and pipets for preparing standards.
3.1.8 An
analytical balance capable of weighing to the nearest 0.01
mg.
3.2 Reagents
3.2.1 Ethanolamine, reagent
grade
3.2.2 Dimethy1formamide (DMF), HPLC grade
3.2.3 1-Naphthylisothiocyanate (NITC), reagent grade
3.2.4 Isooctane, HPLC grade
3.2.5 Isopropanol,
HPLC grade.
3.3 Sample preparation
3.3.1 Sample tubes are opened and the
front and back section of each tube are placed in separate
4-mL vials.
3.3.2 Each section is desorbed with 2 mL
DMF.
3.3.3 The vials are sealed immediately and allowed
to desorb for 30 minutes with occasional
shaking.
3.4 Standard preparation
3.4.1 Stock standards are prepared by
diluting a known quantity of ethanolamine with a solution of NITC in
DMF. The molecular weight of NITC is 185.25, and the molecular weight
of ethanolamine is 61.08. One molecule of the derivative is
formed from one molecule of ethanolamine and one molecule of
NITC. An excess is added to insure that all of the ethanolamine is
reacted. A derivatizing solution of 50 mg NITC in 100 mL DMF was
prepared to make the analytical standards.
An analytical
standard of 1 µL ethanolamine in 10 mL of this derivatizing solution
would be equivalent to 8.1 ppm based on a 10-L air volume and 2 mL
desorption. More concentrated standards can be prepared by weighing
out the ethanolamine, then dry reacting with NITC by adding the molar
quantity of NITC, and then diluting with the derivatizing solution.
This ensures an excess of NITC. An analytical standard of
approximately one drop of ethanolamine in 10 mL weighed 50 mg,
then 152 mg NITC was weighed out in the same volumetric, and the
derivatizing solution was added to obtain a stock standard of 5 mg/mL
derivatized ethanolamine.
3.4.2 At least two separate
stock standards should be made.
3.4.3 Dilutions of these
stock standards are made over the range of the samples, down to the
level of the detection limit. At least four working standards should
be prepared, so that a curve of concentration versus response can be
plotted. Sample concentrations should be bracketed with working
standards.
3.4.4 Analytical standards and samples should
not be placed in an ultrasonic bath, as this causes decomposition of
the derivative.
3.5 Analysis
3.5.1 Liquid chromatograph
conditions.
Column: |
l0-µm Zorbax CN, 25-cm × 4.6-mm
ID |
Mobile Phase: |
80/20 isooctane/isopropanol at
1mL/min |
Injection size: |
10 µL |
Detector: |
UV at 254 nm or 280 nm |
Chromatogram: |
|
Figure 1. Standard of 80.9 ug/mL ethanolamine with NITC
in DMF, analyzed by normal phase.
3.5.2 This
analysis can also be run reverse phase, using the following
conditions.
Column: |
Whatman partisphere
C18,10-cm × 7-mm |
Mobile Phase: |
30/70 acetonitrile/water at 1
mL/min |
Injection size: |
10 µL |
Detector: |
UV at 254 nm or 280 nm |
Chromatogram: |
|
Figure 2. A standard of 80.9 ug/mL ethanolamine in DMF,
analyzed by reversed phase.
3.5.3 Peak areas are measured
by an integrator or other suitable
means.
3.6 Interferences
(analytical)
3.6.1 Any compound having the general
retention time of the analyte is an interference. Possible
interferences should be listed on the sample data sheet. LC parameters
should be adjusted if necessary so these interferences will pose no
problems.
3.6.2 Retention time data on a single column
is not considered proof of chemical identity. Samples over the target
concentration should be confirmed by GC/Mass Spec or other suitable
means.
3.7 Calculations
3.7.1 A curve with area counts versus concentration is
calculated from the calibration standards.
3.7.2 The
area counts for samples are plotted with the calibration curve to
obtain the concentration of triethylamine in solution.
3.7.3 To calculate the air concentration of analyte from the
liquid concentration the following formulae are
used:
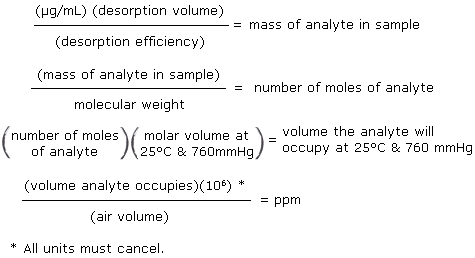
3.7.4 The above equations can be consolidated to form
the following formula. To calculate the ppm of analyte in the sample
based on a 5-liter air sample:

µg/mL |
= concentration of analyte in
sample or standard |
24.46 |
= Molar volume (liters/mole) at
25°C and 760 mmHg. |
MW |
= Molecular weight (g/mole) |
DV |
= Desorption volume |
5 L |
= 5-liter air sample |
DE |
= Desorption
efficiency |
3.7.5
This calculation is done for each section of the sampling tube and the
results added together.
3.8 Safety
precautions
3.8.1. All handling of solvents should
be done in a hood.
3.8.2. Avoid skin contact with all
solvents. 3.8.3. Wear safety glasses at all
times. 4.
Recommendations for further study
Collection efficiencies need to be
studied. 5.
References
5.1 "NIOSH Manual of Analytical Methods", U.S. Department of
Health, Education, and Welfare, Public Health Service, Center for
Disease Control, National Institute for Occupational Safety and Health,
Second Edition, Vol. 4, Method 270.
5.2 Windholz, M., "The
Merck Index", Tenth Edition, Merck & Co., Rahway N.J., 1983, p.
541.
5.3 "Documentation of the Threshold Limit Values and
Biological Exposure Indices", Fifth Edition, American Conference of
Governmental Industrial Hygienists Inc., Cincinnati, OH, 1986, p.
235.
5.4 Elskamp, C., Method 60, "Ethylenediamine,
diethylenetriamine, and triethylenetetramine", Organic Methods
Evaluation Branch, OSHA Analytical Laboratory, 1986.
|