1,1-DICHLORO-1-FLUOROETHANE (Freon
141b) 1,1,2-TRICHLORO-1,2,2-TRIFLUOROETHANE (Freon 113)
|
 |
Method number: |
113 |
|
|
Matrix: |
Air |
|
|
Freon 141b |
Freon 113 |
Target concentrations: |
1000 ppm |
1000 ppm |
|
OSHA PEL: |
|
1000 ppm (7600
mg/m3) |
|
ACGIH TLV: |
|
1000 ppm (TWA) (7600
mg/m3) 1250 ppm (STEL) (9580
mg/m3) |
|
Procedure: |
Samples are collected by drawing a known volume of air
through two standard size (6-mm o.d., 150/75) Anasorb
CMS tubes connected in series. Samples are desorbed with carbon
disulfide and analyzed by GC using a flame ionization detector
(FID). |
|
Recommended air volume and sampling rate: |
1 L at 50 mL/min (20 min) |
|
|
Freon 141b |
Freon 113 |
Reliable quantitation limits: |
2.7 ppm (13
mg/m3) |
3.1 ppm (24 mg/m3) |
|
Standard error of estimate at the target concentration: |
Freon 141b 5.6% |
Freon 113 5.4% |
|
Status of method: |
Evaluated method. This method has been subjected to
the established evaluation procedures of the Organic Methods
Evaluation Branch. |
|
Date: November 1998 |
Chemist: Donald
Burright |
Organic Methods Evaluation Branch OSHA Salt Lake
Technical Center Salt Lake City, UT 84115-1802
1. General Discussion
1.1 Background
1.1.1 History
There has been an
assortment of samplers to collect chlorofluorocarbons (Freons). They
include standard charcoal tubes (100/50 mg), Carbosieve
S-III (130/65 mg), jumbo charcoal tubes (400/200 mg),
and two charcoal tubes in series (400/200 mg followed by 100/50 mg).
(Refs. 5.1-5.4)
The following adsorbents were tested for their capacity to collect
Freons: activated coconut charcoal, Carbosieve S-III,
Carbotrap, Carboxen 1000, Carboxen 1003, Anasorb CMS and Anasorb
747. Fluorotrichloromethane (Freon 11), dichlorodifluoromethane
(Freon 12), chlorodifluoromethane (Freon 22) and
1,1,2-trichloro-1,2,2-trifluoroethane (Freon 113) were
selected for testing based on the number of samples analyzed at the
Salt Lake Technical Center (SLTC).
1,1,1,2-Tetrafluoroethane (Freon 134a) and
1,1-dichloro-1-fluoroethane (Freon 141b) were added to
the list as commonly used members of the new
'environmentally-safe' Freons. Freon 11 was later
dropped from testing because SLTC did not have adequate equipment to
produce an atmosphere of stable concentration. Anasorb CMS (carbon
molecular sieve) had the most capacity to collect the five Freons
tested. So that all of the Freons could have at least a
15-min sampling time, at least 225 mg of Anasorb CMS
must be in the front section of the sampling device. Therefore the
sampling device consists of two Anasorb CMS tubes (each containing
two sections, 150/75 mg) in series. A goal of this work was to find
a common sampler with a common sampling time for all five of the
selected Freons.
Attempts to desorb the Freons from Anasorb CMS resulted in low
recovery. This was due to the amount of air displaced and heat
generated when the desorbing solvent was added to the vial
containing the absorbent. Several solvents and techniques were tried
with poor results. An aluminum block had holes drilled into it to
fit the desorption vial. One technique that had worked with other
analytes was to cool everything. The block, vials containing
adsorbent, pipettes and desorbing solvent were all cooled to
-20 °C. The recovery of Freon from Anasorb CMS with
these chilled components was less than 65%. The 'boiling' action
observed in the vial was allowing the Freon to be driven out of
solution and escape from the vial before it could be sealed with a
cap. A room-temperature solution to this problem was
found. The Anasorb CMS and desorbing solution are placed inside a
vial and are not permitted to mix until the vial is sealed. Freon
can not escape but is dissolved into the desorbing solution after
the bubbles stop forming.
This method covers only Freon 141b and Freon 113 because all five
Freons being studied were not soluble in the same solvent. This
procedure uses carbon disulfide to desorb the samples. Freon 12,
Freon 22 and Freon 134a are more soluble in a desorbing solution
consisting of 60/40 dimethyl formamide/carbon disulfide and will be
described in a later method.
1.1.2 Toxic effects (This section is for information only and
should not be taken as the basis of OSHA policy.)
Short-term exposure to Freon 113 may cause
irritation of the eyes and throat or drowsiness. Breathing high
concentrations may cause the heart to beat irregularly or to stop.
Prolonged or repeated skin exposure to Freon 113 may cause skin
irritation. (Ref.
5.5)
Exposure to Freon 141b may cause dizziness,
eye irritation, difficulty in breathing, rapid heartbeat, and low
blood pressure. (Ref.
5.6)
1.1.3 Workplace exposure
Freon 113 has been used as a refrigerant, a
heat transfer medium, a solvent for oils and gums, a film processing
solvent, a degreasing and dry-cleaning solvent, and an
intermediate in the manufacture of chlorotrifluoroethylene. The
Montreal Protocol on Substances that Deplete the Ozone Layer is
expected to cause an international decline in its use and production
in the 1990s. (Ref.
5.7)
Freon 141b is one of the new
'environmentally-safe' Freons. It is used as a degreasing solvent
and as a blowing agent for refrigerator insulation. The US Clean Air
Act mandates the phase out of Freon 141b by 2003 as it also depletes
the ozone. (Ref.
5.8)
1.1.4
Physical properties and other descriptive information (Refs. 5.6,
5.7
and 5.9)
|
Freon 141b |
Freon 113 |
CAS number: |
1717-00-6 |
76-13-1 |
molecular weight: |
116.95 |
187.38 |
boiling point, °C: |
32 |
48 |
melting point, °C: |
- 103 |
- 35 |
color: |
colorless |
colorless |
specific gravity: |
1.25 |
1.57 |
molecular formula: |
C2H3Cl2F |
C2Cl3F3 |
vapor pressure, kPa (mmHg): |
2 (15) |
44 (330) |
odor: |
|
slight etheral |
solubility: |
insoluble in water |
alcohol; ether; benzene; 0.02% in water |
synonyms: |
Freon 141b; FC-141b; HCFC-141b |
Freon 113; CFC-113; F-113; TTE |
structural formulas: |
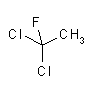 |
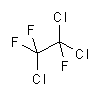 |
The analyte air concentrations throughout this method are based on the
recommended sampling and analytical parameters. Air concentrations listed
in ppm are referenced to 25 °C and 101.3 kPa (760 mmHg).
1.2 Limit defining parameters
1.2.1 Detection limit of the analytical procedure
The detection limits of the analytical procedure are 0.12 and 0.26 ng
for Freon 141b and Freon 113, respectively. These are the amounts of
each analyte that will give a response that is significantly different
from the background response of a reagent blank. (Sections 4.1
and 4.2)
1.2.2 Detection limit of the overall procedure
The detection limits of the overall procedure are 4.0 (0.84 ppm or
4.0 mg/m3) and 7.2 (0.94 ppm or 7.2
mg/m3) µg per sample for Freon 141b and Freon
113, respectively. These are the amounts of each analyte spiked on the
sampler that will give a response that is significantly different from
the background response of a sampler blank. (Sections 4.1
and 4.3)
1.2.3 Reliable quantitation limit
The reliable quantitation limits are 13 (2.7 ppm or 13
mg/m3) and 24 (3.1 ppm or 24
mg/m3) µg per sample for Freon 141b and Freon
113, respectively. These are the amounts of analyte spiked on a sampler
that will give a signal that is considered the lower limit for precise
quantitative measurements. (Section 4.4)
1.2.4 Precision (analytical Procedure)
The precision of the analytical procedure, measured as the pooled
relative standard deviation over a concentration range equivalent to the
range of 0.5 to 2 times the target concentration, is 0.93% and 0.45% for
Freon 141b and Freon 113, respectively. (Section 4.5)
1.2.5 Precision (overall procedure)
The precision of the overall procedure at the 95% confidence level
for the ambient temperature 18-day storage tests (at the
target concentration) is ±11.0 and ±10.5 for Freon 141b and Freon 113,
respectively. This includes an additional 5% for sampling error.
(Section 4.6)
1.2.6 Recovery
The recoveries of Freon 141b and Freon 113 from samples used in the
15-18 day storage tests remained above 99.2% and 100.7%
respectively when the samples were stored at 22 °C. (Section 4.7)
1.2.7 Reproducibility
Six samples, for each analyte, were spiked with a solution containing
one of the Freons after 1 L of humid air had been drawn through the
sampling tubes. These samples were submitted for analysis by one of the
OSHA Salt Lake Technical Center's service branch laboratories along with
a draft copy of this procedure. The samples were analyzed after 15 days
of storage at 4 °C. No individual sample result deviated from its
theoretical value by more than the precision reported in Section 1.2.5.
(Section 4.8)
2. Sampling Procedure
2.1 Apparatus
2.1.1 Samples are collected using a personal sampling pump
calibrated, with the sampling device attached, within ±5% at
the recommended flow rate.
2.1.2 Samples are collected with two 7-cm ×
4-mm i.d. × 6-mm o.d. glass sampling
tubes, each packed with two sections of (150/75 mg) Anasorb
CMS, connected in series. The sections are held in place with
a glass wool plug and two urethane foam plugs. For this
evaluation, commercially prepared sampling tubes were
purchased from SKC, Inc. (catalog no. 226-121).
2.2 Reagents
None required.
2.3 Technique
2.3.1 Immediately before sampling, break off the ends of
both sampling tubes. All tubes should be from the same lot.
Connect the outlet end of one tube to the inlet end of the
other tube with a 1-in. length of
3/16-in.
i.d. silicone rubber tubing. Ensure that the connection is
secure and that the broken ends of the tubes just touch each
other. Be careful not to cut the silicone tubing with the
sharp ends of the sampling tubes.
2.3.2 Attach the sampling device to the sampling pump with
flexible, non-crimping tubing. It is desirable to
utilize sampling tube holders which have a protective cover to
shield the employee from the sharp, jagged end of the sampling
tube. Position the tubes so that the sampled air first passes
through the inlet of the sampling device.
2.3.3 Air being sampled should not pass through any hose or
tubing before entering the sampling device.
2.3.4 To avoid channeling, attach the sampler vertically
with the inlet pointing downward, in the worker's breathing
zone. Position the sampler so it does not impede work
performance or safety.
2.3.5 After sampling for the appropriate time, immediately
remove the sampling device, separate the tubes and seal them
with plastic end caps.
2.3.6 Wrap each tube end-to-end with an
OSHA-21 form.
2.3.7 Submit at least one blank sample with each set of
samples. Handle the blank sampling tube in the same manner as
the other samples, except draw no air through it.
2.3.8 Record sample air volumes (in liters) for each
sample, along with any potential interferences.
2.3.9 Ship any bulk sample(s) in a container separate from
the air samples.
2.3.10 Submit the samples to the laboratory for analysis as
soon as possible after sampling. If delay is unavoidable,
store the samples at reduced temperature.
2.4 Sampler capacity
Sampler capacity is determined by measuring how much air can
be sampled before the analyte breaks through the sampler, i.e.,
the sampler capacity is exceeded. Breakthrough is considered to
occur when the effluent from the sampler contains a
concentration of analyte that is 5% of the upstream
concentration (5% breakthrough). Testing for breakthrough was
performed by using a GC/FID to monitor the effluent from
sampling tubes, each containing 225-mg of Anasorb
CMS. Dynamically generated test atmospheres, which were about
two times the target concentration of each analyte, were used
for the capacity tests. The samples were collected at 50 mL/min
and the relative humidity was about 75% at 25 °C. The 5%
breakthrough air volumes were calculated from the data of
duplicate determinations and are 8.66 and 3.88 L for Freon 141b
and Freon 113, respectively. (Section 4.9)
A goal of this procedure was to develop a common sampling device
with a common sampling time for all five studied Freons.
1,1,1,2-Tetrafluoroethane had the shortest sampling
time and that was the limiting factor in selecting the
20-min sampling time.
2.5 Desorption efficiency
2.5.1 The average desorption efficiencies for Freon 141b
and Freon 113 from Anasorb CMS over the range of 0.5 to 2.0
times the target concentrations (TC) are 99.6% and 100.3%,
respectively. (Section 4.10)
2.5.2 The desorption efficiencies at 0.05, 0.1 and 0.2
times the target concentrations (TC) were found to be very
good and are listed below. (Section 4.10)
Table 2.5.2 Desorption Efficiencies at 0.05
to 0.2 times TC, %
|
TC |
Freon 141b |
Freon 113 |
|
0.05× |
98.3 |
98.4 |
0.1× |
99.0 |
98.8 |
0.2× |
100.5 |
98.9 |
|
2.5.3 Desorbed samples remain stable for at least 24 h.
2.6 Recommended air volume and sampling rate
2.6.1 For long-term samples, collect 1.0 L at
50 mL/min for 20 min.
2.6.2 For short-term samples, collect 0.75 L
at 50 mL/min for15 min.
2.6.3 When short-term samples are collected,
the air concentration equivalent to the reliable quantitation
limit becomes larger. For example, the reliable quantitation
limits are 3.6 ppm (17 mg/m3) and
4.1 ppm (32 mg/m3) for Freon 141b
and Freon 113, respectively, when 0.75 L is sampled.
2.7 Interferences (sampling)
2.7.1 It is not known if any compounds will severely
interfere with the collection of Freon 141b or Freon 113 on
Anasorb CMS. In general, the presence of other contaminant
vapors in the air will reduce the capacity of Anasorb CMS to
collect both analytes.
2.7.3 Suspected interferences should be reported to the
laboratory with submitted samples.
2.8 Safety precautions (sampling)
2.8.1 The sampling equipment should be attached to the
worker in such a manner that it will not interfere with work
performance or safety.
2.8.2 All safety practices that apply to the work area
being sampled should be followed.
2.8.3 Protective eyewear should be worn when breaking off
the ends of the glass sampling tubes.
|
3. Analytical Procedure
3.1 Apparatus
3.1.1 Gas chromatograph equipped with an FID. For this
evaluation, a Hewlett-Packard 5890 Series II Gas
Chromatograph equipped with a 7673A Automatic Sampler was
used. A Forma Scientific Model 2006 refrigerated circulator
was used to cool the sample tray of the HP 7673A to 10 °C to
minimize evaporation.
3.1.2 A GC column capable of separating the analyte of
interest from the desorbing solvent, internal standard and any
interferences. A 60-m × 0.32-mm i.d.
fused silica DB-624 column with a
1.8-µm df (J&W
Scientific, Folsom, CA) was used in this evaluation.
3.1.3 An electronic integrator or some other suitable means
of measuring peak areas. A Waters 860 Networking Computer
System and an HP GC ChemStation were used in this evaluation.
3.1.4 Two- and four-milliliter vials with
polytetrafluoroethylene-lined caps.
Seven-milliliter scintillation vials with
polytetrafluoroethylene-lined caps.
3.1.5 Three-fourths milliliter autosampler vials (8-mm ×
30-mm) from Kimble Glass (catalog no.
60831D-830).
3.1.6 A dispenser capable of delivering 4.0 mL of desorbing
solvent to prepare standards and samples. If a dispenser is
not available, a 4.0-mL volumetric pipette may be
used.
3.2 Reagents
3.2.1 1,1-Dichloro-1-fluoroethane (Freon 141b), reagent
grade or better. The Freon 141b, 97%, used in this evaluation
was purchased from PCR, Inc. (Gainesville, FL).
3.2.2 1,1,2-Trichloro-1,2,2-trifluoroethane (Freon 113),
reagent grade or better. The Freon 113, distilled in glass,
used in this evaluation was purchased from Burdick &
Jackson Laboratories, Inc. (Muskegon, MI).
3.2.3 Carbon disulfide (CS2),
reagent grade or better. The CS2,
99.9+% - low benzene, used in this evaluation was purchased
from Aldrich Chemical (Milwaukee, WI).
3.2.4 A suitable internal standard, reagent grade. The
benzene, 99.94%, used in this evaluation was purchased from EM
Science (Gibbstown, NJ).
3.2.5 Desorbing solvent. The desorbing solvent contains 200
µL of benzene per 1 L of CS2.
3.2.6 GC grade nitrogen, air, and hydrogen.
3.3 Standard preparation
3.3.1 Prepare concentrated stock standard of Freon 141b
and Freon 113 in CS2. Prepare
working analytical standards by injecting microliter amounts
of concentrated stock standards into 4-mL vials
containing 4.0 mL of desorbing solvent delivered from the same
dispenser used to desorb samples. Transfer the standard
solution to 2-mL autosampler vials, if necessary.
For example, to prepare a target level standard of Freon 141b,
inject 20 µL of a stock solution containing 246 mg/mL of Freon
141b in CS2 into 4 mL of desorbing
solvent.
3.3.2 Bracket sample concentrations with working standard
concentrations. If samples fall outside the concentration
range of prepared standards, prepare and analyze additional
standards or dilute the sample.
3.4 Sample preparation
3.4.1 Remove the plastic end caps from the sample tube and
carefully transfer both sections of the adsorbent (225 mg) to
a 0.75-mL vial. Do not place any markings or tape
on the 0.75 mL vial because it will be placed in the desorbing
solvent. Discard the glass tube, urethane foam plugs and glass
wool plug. Place the 225 mg of adsorbent from the
back-up tube in a separate 0.75 mL vial.
3.4.2 Add 4.0 mL of desorbing solvent to each
7-mL scintillation vial using the same dispenser
as used for preparation of standards.
3.4.3 Insert the 0.75-mL vial into the 7-mL
vial and immediately seal the 7-mL vial with a
polytetrafluoroethylene-lined cap.
3.4.4 Shake the vial vigorously by hand several times while
keeping the vial horizontally during the next 60 min. This
will permit the solvent inside the small vial to mix with the
solvent in the larger vial. Do not use a mechanical shaker to
agitate the sample. The adsorbent beads will cause the small
vial to become stuck in the neck of the larger vial and the
result will be inadequate desorption.
3.4.5 Transfer the sample solution to a 2-mL
autosampler vial, if necessary.
3.5 Analysis
3.1 Analytical conditions
GC conditions |
zone temperatures: |
35 °C (column) 250 °C (injector) 300 °C
(detector) |
run time: |
15 min |
column gas flow: |
2.5 mL/min (hydrogen) |
septum purge: |
1.5 mL/min (hydrogen) |
injection size: |
1.0 µL (10.2:1 split) |
column: |
60-m × 0.32-mm i.d. capillary
DB-624 (df = 1.8
µm) |
retention times: |
6.03 min (Freon 141b) 6.55 min (Freon
113) 10.03 min (benzene) |
FID conditions |
hydrogen flow: |
34 mL/min |
air flow: |
450 mL/min |
makeup flow: |
33 mL/min (nitrogen) |
|
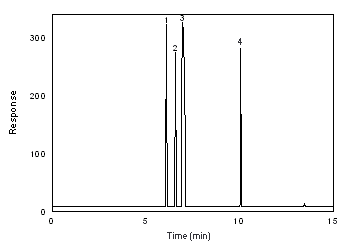 Figure 3.5.1. Chromatogram of Freon
141b and Freon 113 at the target concentration. 1 -
Freon 141b, 2 - Freon 113, 3 - CS2, 4 -
benzene. |
3.2 An internal standard (ISTD)
calibration method is used. A calibration curve can be
constructed by plotting micrograms of analyte per sample
versus ISTD-corrected response of standard
injections. Bracket the samples with freshly prepared
analytical standards over a range of concentrations.
3.6 Interferences (analytical)
3.6.1 Any compound that produces an FID response and has a
similar retention time as the analytes or internal standard is
a potential interference. If any potential interferences were
reported, they should be considered before the samples are
desorbed.
3.6.2 Generally, chromatographic conditions can be altered
to separate an interference from the analyte.
3.6.3 When necessary, the identity or purity of an analyte
peak may be confirmed with additional analytical data.
(Section 4.11)
3.7 Calculations
The amount of analyte per sampler is obtained from the
appropriate calibration curve in terms of micrograms per sample,
uncorrected for desorption efficiency. The back tube is analyzed
primarily to determine if there was any breakthrough from the
front tube during sampling. If a significant amount of analyte
is found on the back tube (e.g., greater than 25% of the amount
found on the front tube), this fact should be reported with the
sample results. If any analyte is found on the back tube, it is
added to the amount on the front tube. This amount is then
corrected by subtracting the total amount (if any) found on the
blank. The air concentration is calculated using the following
formulae.
mg/m3 = |
(micrograms of analyte per sample)
(liters of air sampled)(desorption efficiency)
|
ppm = |
(mg/m3)(24.46)
(molecular weight of analyte)
|
where |
molar volume at 25 °C and 101.3 kPa (760 mmHg) is
24.46 molecular weight of Freon 141b is 116.95
molecular weight of Freon 113 is
187.38 |
3.8 Safety precautions (analytical)
3.8.1 Adhere to the rules set down in your Chemical
Hygiene Plan.
3.8.2 Avoid skin contact and inhalation of all chemicals.
3.8.3 Wear safety glasses, gloves and a lab coat at all
times while in the laboratory areas.
|
4. Backup Data
4.1 Determination of detection limits
YDL -
YBR =
3(SDBR)
Detection limits, in general, are defined as the amount (or
concentration) of analyte that gives a response
(YDL) that is significantly different
[three standard deviations (SDBR)]
from the background response (YBR).
The measurement of YBR and
SDBR in chromatographic methods is
typically inconvenient and difficult because
YBR is usually extremely low.
Estimates of these parameters can be made with data obtained
from the analysis of a series of analytical standards or samples
whose responses are in the vicinity of the background response.
The regression curve obtained for a plot of instrument response
versus concentration of analyte will usually be linear. Assuming
SDBR and the precision of the data
about curve are similar, the standard error of estimate (SEE)
for the regression curve can be substituted for
SDBR in the above equation. The
following calculations derive a formula for DL:
where |
Yobs is observed response
Yest is estimated response
from regression curve n is total number of data points
k is 2 for linear regression curve |
At point YDL on the regression
curve
YDL = A(DL) +
YBR
where A is analytical sensitivity (slope)
therefore
Substituting 3(SEE) + YBR for
YDL gives
4.2 Detection limit of the analytical procedure
(DLAP)
The DLAP is measured as the mass of analyte actually
introduced into the chromatographic column. Ten analytical
standards were prepared in equal descending increments with the
highest standard containing 19.2 and 30.7 µg/mL of Freon 141b
and Freon 113, respectively. This is the concentration that
would produce a peak approximately 10 times the baseline noise
of a reagent blank near the elution time of the analyte. These
standards, and the reagent blank, were analyzed with the
recommended analytical parameters (1-µL injection
with a 10.2:1 split), and the data obtained were used to
determine the required parameters (A and SEE) for the
calculation of the DLAP.
Table 4.2.1. DLAP Data for
Freon 141b A = 186 SEE = 7.16
|
concentration (µg/mL) |
mass on column (ng) |
area
counts (µV-s) |
|
0 1.92 3.85 5.77 7.69 9.61 11.5 13.5 15.4 17.3 19.2 |
0 0.188 0.377 0.565 0.754 0.942 1.13 1.32 1.51 1.70 1.89 |
0 16 50 89 124 160 194 231 258 303 348 |
| |
Figure 4.2.1. Plot of the data from Table 4.2.1 to
determine the DLAP of Freon 141b, DLAP = 0.12 ng.
|
Table 4.2.2. DLAP Data for Freon
113 A = 112 SEE = 9.87
|
concentration (µg/mL) |
mass on column (ng) |
area counts (µV-s) |
|
0 3.07 6.14 9.21 12.3 15.4 18.4 21.5 24.6 27.6 30.7 |
0 0.301 0.602 0.903 1.20 1.50 1.81 2.11 2.41 2.71 3.01 |
0 16 43 96 137 165 184 216 256 302 330 |
|
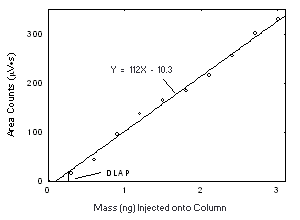
Figure 4.2.2. Plot of the data from Table 4.2.2 to
determine the DLAP of Freon 113, DLAP = 0.26 ng.
|
|
4.3 Detection limit of the overall procedure (DLOP)
The DLOP is measured as mass per sample and expressed as
equivalent air concentration, based on the recommended sampling
parameters. Ten samplers were spiked with equal descending
increments of analyte, such that the highest sampler loading was
76.9 and 123 µg/sample of Freon 141b and Freon 113, respectively.
This is the amount, when spiked on a sampler, that would produce a
peak approximately 10 times the baseline noise for a sample blank.
These spiked samplers, plus a sample blank, were analyzed with the
recommended analytical parameters, and the data obtained used to
calculate the required parameters (A and SEE) for the calculation of
the DLOP. For Freon 141b, the values of 4.12 and 44 were obtained for A and SEE, respectively and the
DLOP was calculated to be 4.0 µg per sample (0.84 ppm or 4.0
mg/m3). For Freon 113, the values of 2.33
and 62 were obtained for A and SEE, respectively
and the DLOP was calculated to be 7.2 µg per sample (0.94 ppm or 7.2
mg/m3).
Table 4.3.1. DLOP Data for Freon
141b
|
mass per sample (µg) |
area counts (µV-s) |
|
0 7.69 15.4 23.1 30.8 38.5 46.1 53.8 61.5 69.2 76.9 |
0 23 55 90 120 156 185 226 252 270 314 |
| |
|
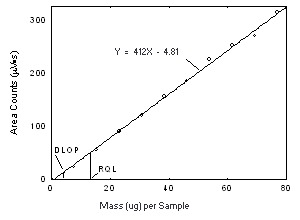 Figure 4.3.1. Plot of the data from Table
4.2.1 to determine the DLOP of Freon 141b on Anasorb CMS, (SEE
= 5.44). |
|
Table 4.3.2. DLOP Data for Freon
113
|
mass per sample (µg) |
area counts (µV-s) |
|
0 12.3 24.6 36.8 49.1 61.4 73.7 86.0 98.2 111 123 |
0 19 54 77 112 135 159 189 218 261 284 |
| |
|
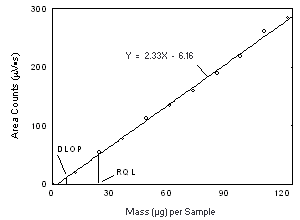 Figure 4.3.2. Plot of the data from Table
4.2.1 to determine the DLOP of Freon 113 on Anasorb CMS, (SEE
= 5.62). |
4.4 Reliable quantitation limit (RQL)
The RQL is considered the lower limit for precise
quantitative measurements. It is determined from the
regression line parameters obtained for the calculations of
the DLOP (Section 4.3),
providing at least 75% of the analyte is recovered. The RQL is
defined as the amount of analyte that gives a response
(YRQL) such that
YRQL - YBR
= 10(SDBR)
therefore
|
|
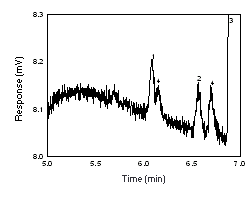 Figure 4.4. Chromatogram of the RQL for
both analytes on Anasorb CMS. 1 = Freon 141b, 2 = Freon 113, 3
= CS2, 4 = interference.
|
Table 4.4 Reliable Quantitation
Limits
|
Freon 141b |
Freon 113 |
|
13 µg 2.7 ppm 13
mg/m3 |
24 µg 3.1 ppm 24
mg/m3 |
|
The RQL for each analyte was calculated and is listed above. The
recovery of the analyte near the RQL was 99.5% and 96.3% for Freon
141b and Freon 113, respectively.
|
4.5 Precision (analytical method)
The precision of the analytical procedure is measured as the
pooled relative standard deviation (RSDP).
Relative standard deviations are determined from six replicate
injections of analyte standards at 0.5, 0.75, 1, 1.5 and 2 times the
target concentration. After assuring that the RSDs satisfy the
Cochran test for homogeneity at the 95% confidence level,
RSDP was calculated to be 0.93% and 0.45%
for Freon 141b and Freon 113, respectively.
Table 4.5.1 Instrument Response to Freon
141b
|
× target concn (µg/mL) |
0.5× 615 |
0.75× 923 |
1× 1230 |
1.5× 1845 |
2× 2460 |
|
area counts (mV-s)
 SD RSD (%) |
157.23 157.22 159.56 160.15 156.29 156.31 157.79 1.375 0.871 |
235.20 229.84 230.53 226.62 229.93 225.81 229.66 2.293 0.999 |
295.72 297.38 296.14 296.65 300.30 302.17 298.06 2.117 0.710 |
441.19 448.19 437.30 451.01 444.80 440.63 443.85 4.147 0.934 |
574.19 573.49 571.21 590.26 585.16 581.85 579.36 6.396 1.104 |
|
Table 4.5.2 Instrument Response to Freon 113
|
× target concn (µg/mL) |
0.5× 981 |
0.75× 1472 |
1× 1963 |
1.5× 2944 |
2× 3925 |
|
area counts (mV-s)
 SD RSD (%) |
117.04 118.30 119.16 118.39 118.97 119.72 118.60 0.686 0.579 |
175.15 174.88 173.80 176.22 177.26 175.66 175.49 0.885 0.504 |
234.08 231.15 231.67 230.90 231.56 233.42 232.13 1.082 0.466 |
341.46 341.14 345.79 343.27 342.88 343.47 343.00 1.175 0.343 |
453.08 455.29 454.31 457.94 454.54 452.17 454.56 4.372 0.302 |
| |
The Cochran test for homogeneity:
The critical value of the g-statistic, at the 95%
confidence level, for five variances, each associated with six
observations is 0.5065. The g-statistics are 0.2801 and
0.3301 for Freon 141b and Freon 113, respectively. Because the
g-statistic does not exceed this value, the RSDs can be
considered equal and they can be pooled
(RSDP) to give an estimated RSD for the
concentration range studied.
4.6 Precision (overall procedure)
The precision of the overall procedure is determined from the
storage data in Section 4.7. The determination of the standard error
of estimate (SEER) for a regression line
plotted through the graphed storage data allows the inclusion of
storage time as one of the factors affecting overall precision. The
SEER is similar to the standard deviation,
except it is a measure of the dispersion of data about a regression
line instead of about a mean. It is determined with the following
equation:
where |
Yobs |
= |
observed % recovery at a given time |
|
Yest |
= |
estimated % recovery from the regression line at the same
given time |
|
n |
= |
total number of data points |
|
k |
= |
2 for linear regression |
|
k |
= |
3 for quadratic regression |
An additional 5% for pump error (SP) is added to the
SEER by the addition of variances to
obtain the total standard error of the estimate.
The precision at the 95% confidence level is obtained by
multiplying the standard error of estimate (with pump error
included) by 1.96 (the z-statistic from the standard normal
distribution at the 95% confidence level). The 95% confidence
intervals are drawn about their respective regression lines in the
storage graphs, as shown in Figures 4.7.1.1
through 4.7.2.2.
The precisions of the overall procedure and the associated figures
are listed below.
4.7 Storage test
|
4.7.1 Freon 141b
Storage samples were generated by sampling from a controlled test
atmosphere containing 3400 mg/m3 of Freon
141b, about 0.7 times the 1000-ppm target
concentration. Anasorb CMS tubes were used to sample for 20 min at
50 mL/min, the relative humidity was about 80% at 22 °C.
Thirty-six storage samples were prepared. Six samples
were analyzed immediately after generation, fifteen tubes were
stored at reduced temperature (4 °C) and the other fifteen were
stored in a closed drawer at ambient temperature (about 22 °C). At
2-4 day intervals, three samples were selected from
each of the two sets and analyzed.
Table 4.7.1 Storage Test for Freon 141b on Anasorb
CMS
|
time (days) |
ambient storage recovery (%) |
|
refrigerated storage recovery
(%) |
|
0 3 5 8 12 15 |
97.2 102.1
94.8 96.0 98.7 96.8 100.1 |
101.6 104.6
96.4 96.8 99.4 99.5 100.3 |
100.5 100.5
98.9 97.8 101.5 99.0 102.3
|
|
97.2 102.1 99.5 98.9 100.9
101.3 101.2 |
101.6 104.6 103.8
99.9 101.1 99.9 97.5 |
100.5 100.5 101.0 101.8
99.2 101.0 103.6 |
|
|
4.7.2 Freon 113
Storage samples were generated by sampling from a controlled test
atmosphere containing 6700 mg/m3 of Freon
113, about 0.9 times the 1000-ppm target concentration.
Anasorb CMS tubes were used to sample for 20 min at 50 mL/min, the
relative humidity was about 80% at 22 °C. Thirty-six
storage samples were prepared. Six samples were analyzed immediately
after generation, fifteen tubes were stored at reduced temperature
(4 °C) and the other fifteen were stored in a closed drawer at
ambient temperature (about 22 °C). At 3-5 day
intervals, three samples were selected from each of the two sets and
analyzed.
Table 4.7.2 Storage Test for Freon 113 on Anasorb
CMS
|
time (days) |
ambient storage recovery (%) |
|
refrigerated storage recovery
(%) |
|
0 3 8 11 15 18 |
103.4 100.0 99.1 102.9 103.7 99.5 102.4 |
98.7 98.1 103.1 102.5 102.8 98.2 102.4 |
100.3 99.3 101.1 104.1 103.8 103.9 102.1 |
|
103.4 100.0 99.8 104.2 103.3 103.3 104.0 |
98.7 98.1 104.8 100.9 105.7 101.9 100.4 |
100.3 99.3 100.5 100.8 103.8 102.8 104.8 |
|
|
4.8 Reproducibility
Six samples for each analyte were prepared by drawing humid air
through the sampling tube for 20 min at 50 mL/min. The samplers were
then liquid-spiked with an aliquot of a solution
containing one of the Freons. The samples were submitted, along with
a draft copy of this procedure, to an OSHA Salt Lake Technical
Center service branch. The samples were analyzed after being stored
for 15 days at 4 °C. Sample results were corrected for desorption
efficiency. No sample result for Freon 141b or Freon 113 had a
deviation greater than the precision of the overall procedure
determined in Section 4.6.
Table 4.8 Reproducibility Data
|
|
Freon 141b
|
Freon 113
|
sample |
expected (ppm) |
reported (ppm) |
recovery (%) |
deviation (%) |
expected (ppm) |
reported (ppm) |
recovery (%) |
deviation (%) |
|
1 2 3 4 5 6 |
1015 1015 1015 1015 1015 1015 |
916.0 964.4 995.3 1017.7 1010.1 996.5 |
90.6 95.4 98.5 100.7 99.9 98.6 |
- 9.4 - 4.6 - 1.5 + 0.7 -
0.1 - 1.4 |
979 979 979 979 979 979 |
924.3 894.0 903.4 926.3 929.4 940.3 |
94.1 91.0 92.0 94.3 94.6 95.8 |
- 5.9 - 9.0 - 8.0 - 5.7 -
5.4 - 4.2 |
|
|
4.9 Sampler capacity
The sampling capacity of a sampling tube containing 225 mg of
Anasorb CMS was tested by sampling from a dynamically generated test
atmosphere of Freon 141b (9560 mg/m3 or
1999 ppm) or Freon 113 (15300 mg/m3 or
1998 ppm). The samples were collected at 50 mL/min and the relative
humidity was about 75% at 25 °C. A GC with a gas sampling valve was
placed in-line behind the 225-mg front
test section. The valve was rotated to measure the amount of Freon
passing through the sampler at the time of rotation. The 5%
breakthrough air volume was determined to be 8.66 and 3.88 L for
Freon 141b and Freon 113, respectively.
Table 4.9.1 Capacity of Freon 141b
on Anasorb CMS
|
first test |
second
test |
air volume (L) |
breakthrough (%) |
air volume (L) |
breakthrough (%) |
|
7.30 7.55 7.80 8.05 8.30 8.55 8.80 9.05 9.30 |
0 0 0.27 0.48 1.5 2.7 5.9 10.5 16.7 |
7.54 7.80 8.05 8.3 8.55 8.80 9.05 9.3 |
0 0 0.36 1.0 2.9 6.7 12.1 18.4 |
| |
Figure 4.9.1. Five percent breakthrough air
volume for Feon 141b on Anasorb CMS.
|
Table 4.9.2 Capacity of Freon 113
on Anasorb CMS
|
first test |
second
test |
air volume (L) |
breakthrough (%) |
air volume (L) |
breakthrough (%) |
|
3.24 3.44 3.64 3.85 4.05 4.25 4.65 |
0 0 1.1 3.3 6.7 11.1 17.7 |
3.05 3.25 3.46 3.66 3.86 4.06 4.26 4.47 |
0 0 0.60 2.0 4.4 8.8 14.0 19.6 |
| |
Figure 4.9.1. Five percent breakthrough air
volume for Feon 113 on Anasorb CMS.
|
|
4.10 Desorption efficiency and stability of
desorbed samples
4.10.1 Freon 141b
The desorption efficiencies (DE) of Freon 141b were determined
by liquid-spiking 225-mg of Anasorb CMS
in a vial with amounts equivalent to 0.05 to 2 times the
1000-ppm target concentration. These samples were
stored overnight at ambient temperature and then desorbed and
analyzed. The average desorption efficiency over the working range
of 0.5 to 2 times the target concentration is 99.6%.
Table 4.10.1.1 Desorption Efficiency of Freon 141b
from Anasorb CMS
|
× target concn (µg/sample) |
0.05× 246 |
0.1× 492 |
0.2× 984 |
0.5× 2460 |
1.0× 4920 |
2.0× 9840 |
|
DE (%)
 |
98.0 99.6 98.8 97.1 99.6 96.6 98.3 |
98.5 97.8 97.9 99.3 99.2 101.4
99.0 |
100.3 99.0 103.0
99.6 100.7 100.4 100.5 |
98.2 97.1 96.7 95.2 96.4 100.7
97.4 |
99.3 103.3 101.9 101.3 101.6
96.7 100.7 |
99.2
99.9 102.3 102.2 100.4
99.8 100.6 |
|
The stability of desorbed samples was investigated by
reanalyzing the target concentration samples 24 h after initial
analysis. After the original analysis was performed, three vials
were recapped with new septa while the remaining three retained
their punctured septa. The samples vials were stored in the
refrigerated sampling tray (10 °C) for the GC injector. The
samples were reanalyzed with fresh standards. The average percent
change was +1.6% for samples that were resealed with new septa,
and - 0.3% for those that retained their punctured septa.
Table 4.10.1.2 Stability of Desorbed Samples for
Freon 141b from Anasorb CMS
|
punctured septa
replaced |
punctured septa
retained |
initial DE (%) |
DE after one day (%) |
difference |
initial DE (%) |
DE after one day (%) |
difference |
|
99.3 103.3 101.9
101.5 |
102.6 105.2 101.6 (averages) 103.1 |
+3.3 +1.9 - 0.3
+1.6 |
101.3 101.6
96.7
99.9 |
98.5 99.1 101.2
(averages) 99.6 |
- 2.8 - 2.5 +4.5
- 0.3 |
|
|
4.10.2 Freon 113
The desorption efficiencies (DE) of Freon 113 were determined by
liquid-spiking 225-mg of Anasorb CMS in a
vial with amounts equivalent to 0.05 to 2 times the
1000-ppm target concentration. These samples were
stored overnight at ambient temperature and then desorbed and
analyzed. The average desorption efficiency over the working range
of 0.5 to 2 times the target concentration is 100.3%.
Table 4.10.2.1 Desorption Efficiency of Freon 113 from
Anasorb CMS
|
× target concn (µg/sample) |
0.05× 243.1 |
0.1× 486.2 |
0.2× 972.4 |
0.5× 2431 |
1.0× 4862 |
2.0× 9724 |
|
DE (%)
 |
97.9 98.9 98.8 99.7 97.6 97.6 98.4 |
100.2
98.7 98.5 98.5 98.6 98.2 98.8 |
98.4 98.5 99.0 99.2 99.5 99.0 98.9 |
99.5 100.3 100.6
99.6 100.3 99.5 100.0 |
99.5 100.6 100.7 100.4 100.7 101.3 100.5 |
99.8 101.0
99.8 101.4 100.2 100.4 100.4 |
| |
The stability of desorbed samples was investigated by reanalyzing
the target concentration samples 24 h after initial analysis. After
the original analysis was performed, three vials were recapped with
new septa while the remaining three retained their punctured septa.
The samples vials were stored in the refrigerated sampling tray (10
°C) for the GC injector. The samples were reanalyzed with fresh
standards. The average percent change was - 0.9% for samples that
were resealed with new septa, and - 0.9% for those that retained
their punctured septa.
Table 4.10.2.2 Stability of Desorbed Samples for Freon
113 from Anasorb CMS
|
punctured septa replaced |
punctured septa
retained |
initial DE (%) |
DE after one day (%) |
difference |
initial DE (%) |
DE after one day (%) |
difference |
|
99.5 100.6 100.7
100.3 |
98.5 99.6 100.1
(averages) 99.4 |
- 1.0 - 1.0 - 0.6
- 0.9 |
100.4 100.7 101.3
100.8 |
99.4 99.3 101.1
(averages) 99.9 |
- 1.0 - 1.4 - 0.2
- 0.9 |
|
4.11 Qualitative analysis
Freon 141b and Freon 113 can be easily separated and identified
by GC/MS. Mass spectra were obtained from an HP5973 Mass Selective
Detector interfaced to an HP6890 GC.
Figure 4.11.1. Mass spectrum of Freon 141b.
|
Figure 4.11.2. Mass spectrum of Freon 113.
|
5. References
5.1 NIOSH Manual of Analytical
Methods, Eller, P.M., Ed, 4th ed.,
US Department of Health and Human Services, Public Health
Service, Centers for Disease Control, National Institute for
Occupational Safety and Health, Division of Physical Science and
Engineering, Cincinnati, OH, DHHS (NIOSH) Publication No.
94-113, 1994; Method 1018. (Back
to Text)
5.2 NIOSH Manual of Analytical
Methods, Eller, P.M., Ed, 4th ed.,
US Department of Health and Human Services, Public Health
Service, Centers for Disease Control, National Institute for
Occupational Safety and Health, Division of Physical Science and
Engineering, Cincinnati, OH, DHHS (NIOSH) Publication No.
94-113, 1994; Method 1020. (Back
to Text)
5.3 NIOSH Manual of Analytical
Methods, Eller, P.M., Ed, 4th ed.,
US Department of Health and Human Services, Public Health
Service, Centers for Disease Control, National Institute for
Occupational Safety and Health, Division of Physical Science and
Engineering, Cincinnati, OH, DHHS (NIOSH) Publication No.
94-113, 1994; Method 1006. (Back
to text)
5.4 OSHA Computerized Information System
Database, Chemical Sampling Information, Salt Lake Technical
Center, Occupational Safety and Health Administration, Salt Lake
City, UT, Sept 1998. (Back
to text)
5.5 Occupational Health Guidelines for
Chemical Substances, NIOSH/OSHA, DHHS (NIOSH) Publ No.
81-123, Jan 1981. (Back
to text)
5.6 Material Safety Data Sheet:
1,1-Dichloro-1-fluoroethane, PCR, Inc.,
Gainesville, FL, Nov 1992. (Back
to text)
5.7 Documentation of the Threshold
limits Values and Biological Exposures Indices,
6th ed., American Conference of
Governmental Industrial Hygienists, Inc.: Cincinnati, OH, 1991,
Vol. III, pp. 1631-1635. (Back
to text)
5.8 Hileman, B.; A Chilling Battle.
Chem. Eng. News, 1998, 76(31), 33-34. (Back
to text)
5.9 Material Safety Data Sheet;
Trichlorotrifluoroethane, DuPont Canada, Inc., Mississauga,
Ontario, Jan 1998. (Back
to text)
|
|