 ETHYL ACRYLATE METHYL ACRYLATE
Method no.: |
92 |
Matrix: |
Air |
Target concentration: |
5 ppm (20 mg/m3) for ethyl
acrylate 10 ppm (35 mg/m3) for methyl
acrylate |
Procedure: |
Samples are collected by drawing air through glass sampling
tubes containing coconut shell charcoal coated with
4-tert-butylcatechol. Samples are desorbed with
carbon disulfide and analyzed by GC using a flame ionization
detector. |
Recommended air volume and sampling rate: |
12 L at 0.05 L/min |
Reliable quantitation limit: |
20 ppb (80 µg/m3) for ethyl
acrylate 40 ppb (140 µg/m3) for
methyl acrylate |
Standard error of estimate at the target
concentration: (Section
4.7.) |
5.14% for ethyl acrylate 5.50% for methyl acrylate |
Status of method: |
Evaluated method. This method has been subjected to the
established evaluation procedures of the Organic Methods Evaluation
Branch. |
Date: December 1991 |
Chemist: Donald Burright |
Organic Methods Evaluation Branch OSHA Salt Lake Technical
Center Salt Lake City, UT 84165-0200
1. General Discussion
1.1. Background
1.1.1. History
The OSHA Salt Lake Technical Center has in the past used a
modified form of NIOSH Methods 1450 and S-38 for the
sampling and analysis of ethyl acrylate (EA) and methyl acrylate
(MA) respectively. (Refs. 5.1.
and 5.2.)
These methods specify collection on coconut shell charcoal,
desorption with carbon disulfide (CS2) and
analysis by GC with a flame ionization detector (FID). The
modification changed the desorption solvent to 95/5 methylene
chloride/methanol. With these modified procedures, both EA and MA
display an increase in their respective desorption efficiencies.
However, the desorption efficiencies still remain a function of
sampler loading. For example, the desorption efficiency for EA
decreases from 99.8% to 84.9% as the amount on the sampler decreases
from 1.7 to 0.08 times of target concentration, and for MA it
decreases from 91.2% to 66.7% as the amount on the sampler decreases
from 0.8 to 0.04 times of target concentration. To eliminate this
deficiency, coconut shell charcoal coated with
4-tert-butylcatechol (TBC) was utilized for sampling. This
material had been found to stabilize styrene at low sampler loading
on the charcoal and eliminate the non-constant desorption
efficiency. This same result was observed for EA and MA. An extended
temperature program on the GC was used to remove the TBC from the
chromatographic column after each injection and resulted in a 25 min
run time. 1.1.2. Toxic effects (This section is for information only
and should not be taken as the basis of OSHA policy.) Inhalation of
EA vapors can irritate the nose, throat and lungs. Vapor
concentrations of 25 ppm may not be tolerated for more than a few
minutes. Higher concentrations may cause drowsiness, dizziness,
tiredness, headache, nausea, difficulty in breathing and
convulsions. Vapors can be irritating to the eyes and cause tears.
Liquid can cause serious burns of the eyes. Skin contact by pure
liquid or concentrated solutions of EA can cause severe irritation
and burns. EA can cause marked local irritation of the mouth and
digestive tract if ingested. Large doses can be fatal. (Ref.
5.3.) In the Code of Federal Regulations, the final rule limits
in Table Z-1-A specify a TWA of 5 ppm (20
mg/m3) and a STEL of 25 ppm (100
mg/m3). The table also lists a skin
designation. (Ref.
5.4.) International Agency for Research on Cancer (IARC) states
there is sufficient evidence for the carcinogenicity of EA in
experimental animals. No data on humans were available. (Ref.
5.5.)
Inhalation of MA vapors can irritate the nose, throat and lungs.
Irritation can occur at concentrations of 75 ppm. Higher
concentrations may cause drowsiness, dizziness, tiredness, headache,
nausea, difficulty in breathing and convulsions. Severe exposure can
be fatal. Vapors can irritate the eyes and cause tears. Liquid can
cause chemical burns of the eyes. Skin contact by liquid MA can
cause severe irritation or burns. Vapors are irritating to the skin.
Toxic amounts of MA can be absorbed through intact skin. MA can
cause marked local irritation of the mouth and digestive system if
ingested. Large doses can be fatal. (Ref.
5.3.) In the Code of Federal Regulations, the final rule limits
in Table Z-1-A specify a TWA of 10 ppm (35
mg/m3) and lists a skin designation. (Ref.
5.4.) IARC states there is inadequate evidence for the
carcinogenicity of MA in experimental animals. No data on humans
were available. (Ref.
5.6.)
1.1.3. Workplace exposure
EA is used in the manufacture of acrylic emulsion polymers used
in paints, surface coatings for textiles, paper and leather,
adhesives and sealants; acrylic fibers; chemical intermediates;
fragrance and flavoring agent. (Ref.
5.3.) The U.S. International Trade Commission reported
production of 131 million kilograms during 1983. (Ref.
5.5.)
MA is used primarily as a comonomer with acrylonitrile in the
manufacture of acrylic and modacrylic fibers; in the manufacture of
acrylic emulsion polymers used in paints, surface coatings for
textiles, paper and leather, adhesives, sealants, and surfactants;
and in the synthesis of vitamin B1. (Ref.
5.3.) Fourteen million kilograms were produced during 1983. (Ref.
5.6.)
1.1.4. Physical properties and other descriptive information
(Ref. 5.3.)
compound: |
ethyl acrylate |
methyl acrylate |
CAS no.: |
140-88-5 |
96-33-3 |
molecular weight: |
100.12 |
86.09 |
melting point: |
-75°C |
-75°C |
boiling point: |
99°C |
80°C |
chemical formula: |
C5H8O2 |
C4H6O2 |
vapor pressure: (at 20°C) |
4 kPa (30 mmHg) |
9.2 kPa (69 mmHg) |
density: (at 20°C) |
0.923 g/mL |
0.957 g/mL |
self-ignition temperature: |
372°C |
468°C |
flash point: (open cup) |
10°C |
-3°C |
lower explosive limit: |
1.4% |
2.8% |
upper explosive limit: |
14% |
25% |
odor threshold: |
0.5 ppb |
14 ppb |
solubility: |
slightly soluble in water; soluble in alcohol and ether |
moderately soluble in water; soluble in alcohol, ether,
acetone and benzene |
synonyms: |
acrylic acid, ethyl ester; ethyl
2-propenoate; ethoxy carbonyl ethylene;
2-propenoic acid, ethyl ester |
acrylic acid, methyl ester; methyl
2-propenoate; 2-propenoic acid,
methyl ester |
molecular structure: |
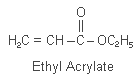 |
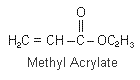 |
The analyte air concentrations throughout this method are based on the
recommended sampling and analytical parameters. Air concentrations
listed in ppm and ppb are referenced to 25°C and 101.3 kPa (760 mmHg).
1.2. Limit defining parameters
1.2.1. Detection limit of the analytical procedure
The detection limits of the analytical procedure are 0.077 and
0.135 ng per injection (1.0-µL injection with a
12.5:1 split) for EA and MA respectively. These are the amounts of
analyte that will produce peaks with heights that are approximately
5 times the baseline noise. (Section
4.1.)
1.2.2. Detection limit of the overall procedure
The detection limits of the overall procedure are 0.961 and 1.682
µg per sample for EA and MA respectively. This is the amount
of analyte spiked on the sampling device that, upon analysis,
produces a peak similar in size to that of the respective detection
limit of the analytical procedure. These detection limits correspond
to air concentrations of 20 ppb (80
µg/m3) and 40 ppb (140
µg/m3) for EA and MA respectively.
(Section
4.2.)
1.2.3. Reliable quantitation limit
The reliable quantitation limits are 0.961 and 1.682 µg
per sample for EA and MA respectively. This is the smallest amount
of analyte which can be quantitated within the requirements of a
recovery of at least 75% and a precision (±1.96 SD) of ±25% or
better. These detection limits correspond to air concentrations of
20 ppb (80 µg/m3) and 40 ppb (140
µg/m3) for EA and MA respectively.
(Section
4.3.)
The reliable quantitation limit and detection limits reported in
the method are based upon optimization of the instrument for the
smallest possible amount of analyte. When the target concentration
of analyte is exceptionally higher than these limits, they may not
be attainable at the routine operating parameters.
1.2.4. Instrument response to the analyte
The instrument responses over concentration ranges representing
0.5 to 2 times the target concentration are linear. (Section
4.4.)
1.2.5. Recovery
The recoveries of EA and MA from samples used in 16-day ambient
storage tests remained above 96.9% and 96.7% respectively. (Section
4.5., regression lines of Figures 4.5.1.1.
and 4.5.2.1.)
1.2.6. Precision (analytical procedure)
The pooled coefficients of variation obtained from replicate
determinations of analytical standards at 0.5, 1 and 2 times the
target concentrations are 0.0046 and 0.0189 for EA and MA
respectively. (Section
4.6.)
1.2.7. Precision (overall procedure)
The precisions at the 95% confidence level for the 16-day ambient
temperature storage tests are ±10.1% and ±10.8% for EA and MA
respectively. (Section
4.7.) These each include an additional ±5% for sampling error.
1.2.8. Reproducibility
Six samples, liquid-spiked with EA and MA and a draft copy of
this procedure were given to a chemist unassociated with this
evaluation. The samples were analyzed for EA and MA after 11 days of
storage at 12C. No individual sample result for EA and MA deviated
from its theoretical value by more than the precision reported in Section
1.2.7. (Section
4.8.)
1.3. Advantages
1.3.1. The new adsorbent, TBC-coated coconut shell charcoal,
provides constant desorption with CS2 at
low sampler loadings unlike the non-constant desorption
of untreated coconut shell charcoal.
1.3.2. The sampler may be used for other analytes, i.e. styrene
or vinyl benzene.
2. Sampling Procedure
2.1. Apparatus
2.1.1. Samples are collected using a personal sampling pump that
can be calibrated within ±5% of the recommended flow rate with the
sampling device attached.
2.1.2. Samples are collected with 4-mm i.d. × 6-mm o.d. × 7.0 cm
glass sampling tubes packed with two sections of coconut shell
charcoal that has been coated with TBC, 10% by weight. The front
section contains 110 mg and the back section contains 55 mg of
TBC-coated coconut shell charcoal. The sections are
held in place with glass wool plugs. For this evaluation, tubes were
purchased from SKC, Inc. (catalog no. 226-73).
2.2. Reagents
No sampling reagents are required.
2.3. Technique
2.3.1. Immediately before sampling, break off the ends of the
TBC-coated coconut shell charcoal tube. All tubes
should be from the same lot.
2.3.2. Attach the sampling tube to the sampling pump with
flexible tubing. It is desirable to utilize sampling tube holders
which have a protective cover to shield the employee from the sharp,
jagged end of the sampling tube. Position the tube so that sampled
air passes through the 110-mg section first.
2.3.3. Air being sampled should not pass through any hose or
tubing before entering the sampling tube.
2.3.4. Attach the sampler vertically with the 110-mg section
pointing downward, in the worker's breathing zone so it does not
impede work performance or safety.
2.3.5. After sampling for the appropriate time, remove the sample
and seal the tube with plastic end caps. Wrap each sample
end-to-end with a Form OSHA-21 seal.
2.3.6. Submit at least one blank sample with each set of samples.
Handle the blank sample in the same manner as the other samples
except draw no air through it.
2.3.7. Record sample volumes (in liters of air) for each sample,
along with any potential interferences.
2.3.8. Ship any bulk samples separate from the air samples.
2.3.9. Submit the samples to the laboratory for analysis as soon
as possible after sampling. If delay is unavoidable, store the
samples at reduced temperature.
2.4. Sampler capacity
2.4.1. The sampling capacity of the front section of a
TBC-coated coconut shell charcoal sampling tube was tested by
sampling from a dynamically generated test atmosphere of MA (70.5
mg/m3 or 20.0 ppm). The samples were
collected at 0.05 L/min and the relative humidity was 80%. A 5%
breakthrough air volume was not attained after sampling for 6.5 h or
19.5 L, which is 63% greater than the recommended sample volume of
12 L.
2.4.2. The sampling capacity of the front section of a TBC-coated
coconut shell charcoal sampling tube was tested by sampling from a
dynamically generated test atmosphere of EA (40.9
mg/m3 or 9.99 ppm). The samples were
collected at 0.05 Lpm and the relative humidity was 80%. A 5%
breakthrough air volume was not attained after sampling for 7 h or
21.0 L, which is 75% greater than the recommended sample volume of
12 L.
2.5. Desorption efficiency
2.5.1. The average desorption efficiencies from TBC-coated
coconut shell charcoal adsorbent are 100.3% and 99.7% for EA and MA
over the range of 0.5 to 2 times the target concentration. (Section
4.10.1.)
2.5.2. Desorbed samples remain stable for at least 24 h. (Section
4.10.2.)
2.6. Recommended air volume and sampling rate
2.6.1. For time-weighted average samples, the recommended air
volume is 12 L collected at 0.05 L/min (4-h samples).
An air volume, which is well within the capacity of the sampler, is
recommended because of the potential sampling interferences caused
by other substances collected during longer sampling times.
2.6.2. For short-term exposure limit samples, the recommended air
volume is 0.75 L collected at 0.05 L/min (15-min
samples).
2.6.3. When short-term exposure limit samples are required, the
reliable quantitation limit becomes larger. For example, the
reliable quantitation limits are 0.32 ppm (1.3
mg/m3) and 0.64 ppm (2.3
mg/m3) for EA and MA respectively when
0.75 L of air is collected.
2.7. Interferences (sampling)
2.7.1. It is not known if any compounds will severely interfere
with the collection of EA or MA on TBC-coated coconut
shell charcoal. In general, the presence of other contaminant vapors
in the air will reduce the capacity of TBC-coated coconut shell
charcoal to collect EA or MA.
2.7.2. Suspected interferences should be reported to the
laboratory with submitted samples.
2.8. Safety precautions (sampling)
2.8.1. The sampling equipment should be attached to the worker
in such a manner that it will not interfere with work performance or
safety.
2.8.2. All safety practices that apply to the work area being
sampled should be followed.
2.8.3. Protective eyewear should be worn when breaking the ends
of the glass sampling tubes.
3. Analytical Procedure
3.1. Apparatus
3.1.1. A GC equipped with a flame ionization detector (FID). A
Hewlett-Packard 5890 Gas Chromatograph equipped with a
7673A Autosampler and an FID was used in this evaluation.
3.1.2. A GC column capable of separating EA, MA and the internal
standard from the desorbing solvent and any potential interferences.
A 60-m × 0.32-mm i.d. SPB-5
(1.0-µm film thickness) capillary column
(Supelco, Inc.) was used in this evaluation.
3.1.3. An electronic integrator or some other suitable means of
measuring detector response. A Waters 860 Networking Computer System
was used in this evaluation.
3.1.4. Two-milliliter vials with polytetrafluoroethylene-lined
caps.
3.1.5. A dispenser capable of delivering 1.0 mL of desorbing
solution is used to prepare standards and samples. If a dispenser is
not available, a 1.0-mL volumetric pipet may be used.
3.2. Reagents
3.2.1. Ethyl acrylate (EA). Practical Grade used in this
evaluation was purchased from JT Baker Chemical Co. (Phillipsburg,
NJ).
3.2.2. Methyl acrylate (MA). The MA used in this evaluation was
purchased from JT Baker Chemical Co. (Phillipsburg, NJ).
3.2.3. Carbon disulfide, CS2. Reagent
grade or better should be used. The carbon disulfide used in this
evaluation was purchased from EM Science (Gibbstown, NJ).
3.2.4. Desorbing solution. The desorbing solution is prepared by
adding 250 µL of an appropriate internal standard to 1 L of
CS2. Benzene (reagent grade) was used in
this evaluation and was purchased from EM Science (Gibbstown, NJ).
3.3. Standard preparation
3.3.1. Prepare concentrated stock standards of EA and MA in
CS2. Prepare working analytical standards
by injecting microliter amounts of concentrated stock standards into
2-mL vials containing 1 mL of desorbing solution
delivered from the same dispenser used to desorb samples. For
example, to prepare a target level standard, inject 10 L of a stock
solution containing 24 and 42 mg/mL of EA and MA respectively in
CS2 into 1 mL of desorbing solution.
3.3.2. Prepare a sufficient number of analytical standards to
generate a calibration curve. Ensure that the amount of EA and MA
found in the samples is bracketed by the range of the standards.
Prepare additional standards if necessary.
3.4. Sample preparation
3.4.1. Remove the plastic caps from the sample tube and
carefully transfer each section of the adsorbent to separate
2-mL vials. Discard the glass tube and glass wool
plugs.
3.4.2. Add 1.0 mL of desorbing solution to each vial and
immediately seal the vials with
polytetrafluoroethylene-lined caps.
3.4.3. Shake the vials vigorously several times during the next
30 min.
3.5. Analysis
3.5.1. Analytical conditions
GC conditions |
|
|
initial temperatures: |
50°C (column) 250°C (injector) 300°C
(detector) |
temp program: |
increase temp at 5°C/min to 100°C, then increase
temp at 25°C/min to 275°C, hold for 8 min. |
run time: |
25 min - this was used to elute the TBC from the
column |
column gas flow: |
1.2 mL/min (hydrogen) |
septum purge: |
1.5 mL/min (hydrogen) |
injection size: |
10 µL (12.5:1 split) |
column: |
60 m × 0.32-mm i.d. capillary SPB-5
(1.0-µm film thickness) |
retention times: |
7.4 min (MA) 8.7 min (benzene) 9.4 min (EA) |
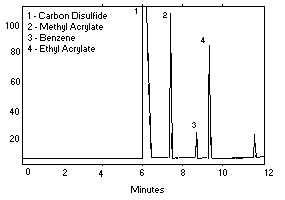 |
|
FID conditions |
|
hydrogen flow: |
34 mL/min |
air flow: |
450 mL/min |
nitrogen makeup flow: |
33 mL/min |
3.5.2. An internal standard (ISTD) calibration method is used. A
calibration curve can be constructed by plotting micrograms of
analyte per milliliter versus ISTD-corrected response
of standard injections. Bracket the samples with freshly prepared
analytical standards over a range of concentrations.
3.6. Interferences (analytical)
3.6.1. Any compound that produces an FID response and has a
similar retention time as the analyte or internal standard is a
potential interference. If any potential interferences were
reported, they should be considered before samples are desorbed.
Generally, chromatographic conditions can be altered to separate an
interference from the analyte.
3.6.2. Retention time on a single column is not considered proof
of chemical identity. Analysis by an alternate GC column or
confirmation by mass spectrometry are additional means of
identification.
3.7. Calculations
The amount of analyte per milliliter is obtained from the
appropriate calibration curve in terms of micrograms per milliliter
uncorrected for desorption efficiency. The back (55-mg)
section is analyzed primarily to determine the extent of sample
saturation during sampling. If any analyte is found on the back
section, it is added to the amount on the front section. This total
amount is then corrected by subtracting the total amount (if any)
found on the blank. The air concentration is calculated using the
following formulae.
|
where |
A = micrograms of analyte per
milliliter B = desorption volume C
= liters of air sampled D =
desorption efficiency | |
|
where |
24.46 MW |
= = = |
molar volume (liters) at 101.3 kPa (760 mmHg) and
25°C 100.12 for EA 86.09 for
MA | |
3.8. Safety precautions (analytical)
3.8.1. Restrict the use of all chemicals to a fume hood.
3.8.2. Avoid skin contact and inhalation of all chemicals.
3.8.3. Wear safety glasses, gloves and a lab coat at all times
while working with chemicals.
4. Backup Data
4.1. Detection limit of the analytical procedure
The injection size recommended in the analytical procedure
(1-µL, 12.5 split) was used to determine the
detection limit of the analytical procedure. The detection
limits of the analytical procedure are 0.077 and 0.135 ng
on-column for EA and MA respectively. These were
the amounts of analyte that gave a peak with a height about 5
times the height of the baseline noise. These detection limits
were determined by analysis of a standard containing 0.961
µg/mL of EA and 1.682 µg/mL of MA. |
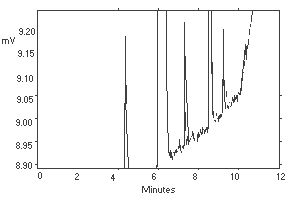 Figure 4.1.
Detection limit of the analytical procedure.
|
4.2. Detection limit of the overall procedure
The detection limits of the overall procedure are 0.961 µg
per sample (20 ppb or 80 µg/m3) for
EA and 1.682 µg per sample (40 ppb or 140
µg/m3) for MA. The injection size
listed in the analytical procedure (1.0 µL, 12.5:1 split) was
used in the determination of the detection limit of the overall
procedure. Six vials containing 110 mg of TBC-coated
coconut shell charcoal were liquid-spiked with 0.961
µg of EA and 1.682 µg of MA. The samples were stored at
ambient temperature and were desorbed about 24 h after being spiked.
Table 4.2.1. Detection Limit of the Overal
Procedure for EA
|
sample no. |
µg spiked |
µg recovered |
|
1 2 3 4 5 6 |
0.961 0.961 0.961 0.961 0.961 0.961 |
0.915 0.947 0.963 0.998 0.928 0.905 |
| |
Table 4.2.2. Detection Limit of the Overal
Procedure for MA
|
sample no. |
µg spiked |
µg recovered |
|
1 2 3 4 5 6 |
1.68 1.68 1.68 1.68 1.68 1.68 |
1.68 1.65 1.64 1.69 1.69 1.70 |
| |
4.3. Reliable quantitation limit data
The reliable quantitation limits are 0.961 µg per sample (20
ppb or 80 µg/m3) for EA and 1.682
µg per sample (40 ppb or 140
µg/m3) for MA. The injection size
listed in the analytical procedure (1.0 µL, 12.5:1 split) was
used in the determination of the reliable quantitation limit. Six
vials containing 110 mg of TBC-coated coconut shell
charcoal were liquid-spiked with a
CS2 solution containing EA and MA. Because
the recovery of the analytes from the spiked samples was greater than
75% and had a precision of ±25% or better, the detection limits of the
overall procedure and reliable quantitation limit are the same.
Table 4.3.1. Reliable Quantiatation Limit for
EA (Based on samples and data of Table
4.2.1.)
|
percent recovered |
statistics |
|
95.2 98.5 100.2 103.9
96.6 94.2
|
mean = SD
= Precision
= = |
98.1 3.6 (1.96)(±3.6) ±7.1 |
| |
Table 4.3.2. Reliable Quantiatation Limit for
MA (Based on samples and data of Table
4.2.2.)
|
percent recovered |
statistics |
|
100.0 98.2
97.6 100.6 100.6 101.2 |
mean = SD
= Precision
= = |
99.7 1.5 (1.96)(±1.5) ±2.9 |
| |
4.4. Instrument response to the analyte
The instrument response to EA and MA over the range of 0.5 to 2
times the target concentration is linear with a slope of 904 and 744
(in ISTD-corrected area counts per microgram per
milliliter) respectively. The precision of the response to the
analytes was determined by multiple injections of standards. The data
below is presented graphically in Figures 4.4.1.
and 4.4.2.
Table 4.4.1. Instrument Response to
EA
|
× target concn µg/mL |
0.5× 120.1 |
1.0× 240.2 |
2.0× 480.5 |
|
area counts |
114739 115864 114104 114893 115627 114515 |
229235 229263 229393 228508 230194 229596 |
439553 438815 442452 442554 444326 443086 |
|
mean |
114957 |
229365 |
441798 |
| |
Table 4.4.2. Instrument Response to
MA
|
× target concn µg/mL |
0.5× 210.3 |
1.0× 420.6 |
2.0× 841.3 |
|
area counts |
160525 161938 155385 159164 155422 157746 |
319379 307530 307678 319313 308723 321258 |
622744 636503 637850 634148 607192 626962 |
|
mean |
158363 |
313980 |
627566 |
| |
|
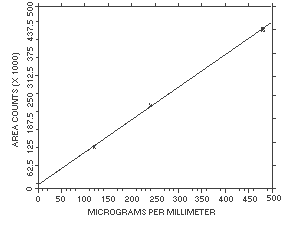 Figure 4.4.1.
Calibration curve for ethyl acrylate. |
 Figure 4.4.2.
Calibration curve for methyl acrylate.
|
4.5. Storage data
Storage samples for EA and MA were prepared by injecting an aliquot
of a CS2 solution containing the analytes
into the TBC-coated coconut shell charcoal. Humid air,
80% RH, was drawn through the tubes for 2 h at 0.05 L/min.
Thirty-six storage samples were prepared. Six samples
were analyzed immediately. Fifteen tubes were stored at reduced
temperature (12°C) and the other fifteen were stored in a closed
drawer at ambient temperature (about 22°C). At 2-5 day
intervals, three samples were selected from each of the two storage
sets and analyzed. The results are listed below and shown graphically
in Figures 4.5.1.1.-4.5.2.2.
Table 4.5.1. Storage Test of EA
|
time (days) |
percent recovery (ambient) |
|
percent recovery (refrigerated) |
|
0 5 7 12 14 16 |
99.3 100.2
97.3 98.5 98.1 97.5 97.2 |
98.4 99.1 96.8 100.2
97.9 98.6 95.4 |
100.7 98.7 96.4 100.7
97.1 96.5 96.4 |
|
99.3 100.2 100.5 100.0 100.0 100.3
98.7 |
98.4 99.1 98.2 99.6 100.8
99.0 100.8 |
100.7 98.7 98.6 100.6 100.4
100.3 100.4 |
|
Table 4.5.2. Storage Test of MA
|
time (days) |
percent recovery (ambient) |
|
percent recovery (refrigerated) |
|
0 5 7 12 14 16 |
103.5 99.5 99.6 100.0 100.8
95.6 96.5 |
101.6 102.4 100.5
95.8 98.8 96.6 94.5 |
101.9 101.8 95.8 93.8 100.2
99.1 98.8 |
|
103.5 99.5 99.3 95.9 100.6
98.9 99.3 |
101.6 102.4 99.4 100.9
103.6 99.6 99.5 |
101.9 101.8 101.8
95.8 105.5 97.5 99.1 |
|
4.6.Precision (analytical method)
The precision of the analytical procedure is defined as the pooled
coefficient of variation determined from replicate injections of EA
and MA standards at 0.5, 1 and 2 times the target concentration. Based
on the data of Tables 4.4.1.
and 4.4.2.,
the coefficients of variation (CV) for the three levels and the pooled
coefficient of variation (CV) were calculated and are listed below.
The pooled coefficient of variations are 0.0046 and 0.0189 for EA and
MA respectively.
Table 4.6.1. Precision of the Analytical Method for
EA (Based on the Data of Table
4.4.1.)
|
× target concn µg/mL |
0.5× 120.1 |
1.0× 240.2 |
2.0× 480.5 |
|
SD1 CV |
671 0.0058 |
553 0.0024 |
2148 0.0049 |
1 - in area counts | |
Table 4.6.2. Precision of the Analytical Method for
MA (Based on the Data of Table
4.4.2.)
|
× target concn µg/mL |
0.5× 210.3 |
1.0× 420.6 |
2.0× 841.3 |
|
SD1 CV |
2684 0.0169 |
6627 0.0211 |
11558 0.0184 |
1 - in area
counts | |
4.7. Precision (overall procedure)
The precision of the overall procedure is determined from the
storage data. The determination of the standard error of estimate
(SEE) for a regression line plotted through the graphed storage data
allows the inclusion of storage time as one of the factors affecting
overall precision. The SEE is similar to the standard deviation,
except it is a measure of dispersion of data about a regression line
instead of about a mean. It is determined with the following equation:
where |
n = k
= k = |
total no. of data points 2 for linear
regression 3 for quadratic regression |
|
Yobs
= |
observed percent recovery at a given time |
Yest
= |
estimated percent recovery from the regression line at the
same given time |
An additional 5% for pump error is added to the SEE by the addition
of variances. The precision at the 95% confidence level is obtained by
multiplying the SEE (with pump error included) by 1.96 (the
z-statistic from the standard normal distribution at the
95% confidence level). The 95% confidence intervals are drawn about
their respective regression line in the storage graph as shown in Figure
4.5.1.1. The data for Figures 4.5.1.1.
and 4.5.2.1.
were used to determine the SEEs of ±5.14% and ±5.50% and the
precisions of the overall procedure of ±10.1% and ±10.8% for EA and MA
respectively.
4.8. Reproducibility data
Six samples were prepared by injecting an aliquot of a
CS2 solution containing the analytes into
the TBC-coated coconut shell charcoal. Humid air, 80% RH,
was drawn through the tubes for 2 h at 0.05 L/min to add water to
sampler matrix. The samples were given to a chemist unassociated with
this study. The samples were analyzed after being stored for 11 days
at 12°C. Sample results were corrected for desorption efficiencies. No
sample result for EA or MA had a deviation greater than the precisions
of the overall procedure determined in Section
4.7., which are ±10.1% and ±10.8% respectively.
Table 4.8.1. Reproducibility Data for
EA
|
µg spiked |
µg recovered |
percent recovered |
percent deviation |
|
240.2 240.2 240.2 240.2 240.2 240.2 |
216.8 224.0 223.6 218.2 218.5 228.8 |
90.3 93.3 93.1 90.8 91.0 95.3 |
-9.7 -6.7- 6.9 -9.2 -9.0 -4.7 |
| |
Table 4.8.2. Reproducibility Data for
MA
|
µg spiked |
µg recovered |
percent recovered |
percent deviation |
|
420.6 420.6 420.6 420.6 420.6 420.6 |
375.4 395.5 393.2 379.6 379.0 406.1 |
89.3 94.0 93.5 90.3 90.1 96.6 |
-10.7
-6.0 -6.5 -9.7 -9.9 -3.4 |
| |
4.9. Sampler capacity
The sampling capacity of the front section of a TBC-coated coconut
shell charcoal sampling tube was tested by sampling from a dynamically
generated test atmosphere of MA (70.5 mg/m3
or 20.0 ppm). The samples were collected at 0.05 L/min and the
relative humiditywas 80%. A complete TBC-coated coconut
shell charcoal sampling tube was placed in-line with the
test front section and changed at measured intervals. After sampling
for 6.5 h or 19.5 L, the back tube (that had been used for only the
last 30 min) contained 1.08 µg of MA, which was 1.02% of the
upstream concentration. The prior sample had contained 0.54%, all
other samples contained no MA. An extrapolation of this data was used
to estimate the 5% breakthrough air volume, which resulted in an air
volume of 28.1 L, well over the recommended air volume of 12 L.
Table 4.9. Breakthrough on the TBC-coated Charcoal Tube
for MA
|
air volume (L) |
sample time (min) |
downstream (mg/m3) |
breakthrough (percent) |
|
1.50 4.50 6.75
8.25
9.75 11.25 12.75 14.25 15.75 17.25 1875 |
30
90 135 165 195 225 255 285 315 345 375 |
0.00 0.00 0.00 0.00 0.00 0.00 0.00 0.00 0.00 0.38
0.72 |
0.00 0.00 0.00 0.00 0.00 0.00 0.00 0.00 0.00 0.54
1.02 |
|
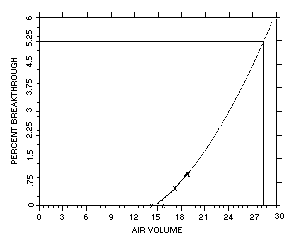 Figure 4.9. Estimated
breakthrough air volume for methyl acrylate.
4.10. Desorption efficiency and stability of desorbed samples
4.10.1. Desorption efficiency
The desorption efficiencies (DE) of EA and MA were determined by
liquid-spiking 110-mg portions of
TBC-coated coconut shell charcoal with the analytes at
0.5 to 2 times the target concentrations. These samples were stored
overnight at ambient temperature and then desorbed with desorbing
solution and analyzed. The average desorption efficiency over the
studied range was 100.3% and 99.7% for EA and MA respectively.
Table 4.10.1.1. Desorption Efficiency of
EA
|
× target concn µg/mL |
0.5× 120.1 |
1.0× 240.2 |
2.0× 480.5 |
|
DE, % |
100.9 99.3 98.7 99.9 100.9
98.9 |
100.2 100.3 101.7 100.3
99.6 101.0 |
101.6 101.7 99.2
99.4 100.7 101.2 |
|
mean |
99.8 |
100.5 |
100.6 |
| |
Table 4.10.1.2. Desorption Efficiency of
MA
|
× target concn µg/mL |
0.5× 210.3 |
1.0× 420.6 |
2.0× 841.3 |
|
DE, % |
99.3 105.8 105.0 100.4
94.2 105.7 |
97.3 95.8 92.8 97.7 97.7 99.5 |
102.8 103.7 101.1 100.4
99.5 96.4 |
|
mean |
101.7 |
96.8 |
100.6 |
| |
4.10.2. Stability of desorbed samples
The stability of desorbed samples was investigated by reanalyzing
the target concentration samples 24 h after initial analysis. The
original analysis was performed and the vials were not recapped
after injection. The samples were reanalyzed with fresh standards.
The average recovery of the reanalysis, compared to the average
recovery of the original analysis, was 99.4% (-0.9%
change) and 90.0% (-9.7% change) for EA and MA
respectively.
Table 4.10.2.1. Stability of Desorbed Samples for
EA
|
initial recovery (percent) |
recovery after 24 h (percent) |
percent change |
|
101.0
99.6 100.3 101.7 100.3 100.2 |
100.8
99.3 99.9 99.0 99.4 98.2 |
-0.2 -0.3 -0.4 -2.7 -0.9 -2.0 |
| |
Table 4.10.2.2. Stability of Desorbed Samples for
MA
|
initial recovery (percent) |
recovery after 24 h (percent) |
percent change |
|
99.5 97.7 97.7 92.8 95.8 97.3 |
86.8 88.7 94.6 89.1 92.3 88.3 |
-12.7
-9.0 -3.1 -3.7 -3.5 -9.0 |
| |
5. References
5.1. "NIOSH Manual of Analytical Methods", 3rd ed.; U.S.
Department of Health and Human Services, Center for Disease Control,
National Institute of Occupational Safety and Health; Cincinnati, OH,
1984, Method 1450, DHHS (NIOSH) Publ. No. 84-100.
5.2. "NIOSH Manual of Analytical Methods", 3rd ed.; U.S. Department
of Health and Human Services, Center for Disease Control, National
Institute for Occupational Safety and Health; Cincinnati, OH, 1984,
Method S-38, DHHS (NIOSH) Publ. No. 84-100.
5.3. Cheminfo Database on CCINFO CD-ROM disc 91-2, Canadian Centre
for Occupational Health and Safety, Hamilton, Ontario.
5.4. "Code of Federal Regulations", Title 29, 1910.1000, Table
Z-1-A. Limits for Air Contaminants, U.S. Government Printing Office,
Washington, D.C., 1990.
5.5. International Agency for Research on Cancer, "IARC Monograph
on the Evaluation of the Carcinogenic Risk of Chemicals to Humans:
Some Chemicals Used in Plastics and Elastomers", IARC, Lyon, France,
1986, Vol. 39, pp. 81-98.
5.6. International Agency for Research on Cancer, "IARC Monograph
on the Evaluation of the Carcinogenic Risk of Chemicals to Humans:
Some Chemicals Used in Plastics and Elastomers", IARC, Lyon, France,
1986, Vol. 39, pp. 99-112.
|