1. General Discussion
1.1 Background
1.1.1 History of procedure
The
OSHA Technical Center has received many requests for a sampling and
analytical procedure for di-tert-butyl-p-cresol (BHT). OSHA
promulgated an exposure standard on January, 1989, for BHT at a level
of 10 mg/m³ TWA. There is a NIOSH method 226 for collection of BHT on
silica gel tubes and desorption by 5/95 methanol/carbon disulfide, and
analysis by GC-FID (Ref. 5.1). This is a partially validated method
with no retention or collection studies performed. The lab performed a
retention study with 10 liters of 89% RH air, on silica gel tubes
spiked with 100 µg BHT. The average recovery was 30.9%, so another
means of collection was explored. OSHA Method 32 collects phenol and
cresol on XAD-7 tubes and desorbs them with methanol (Ref. 5.2). BHT
is related to these compounds, and is a solid at room temperature, so
a modification of method 32 was tried, using an OVS-7 tube instead of
the XAD-7, and found to be successful. An OVS-7 tube is a glass fiber
filter in front of a 270 mg section of XAD-7 resin followed by a 140
mg section of XAD-7 resin. Desorption, retention, and storage
recoveries were good using OVS-7 tubes.
1.1.2 Potential
workplace exposure (Ref. 5.3)
BHT is used as an antioxidant for
food, animal feed, petroleum products, synthetic rubbers, plastics,
animal and vegetable oils, and soaps. BHT is used as an antiskinning
agent for paints and inks.
1.1.3 Toxic Effects (This section is
for information purposes and should not be taken as the basis for OSHA
policy.) (Ref. 5.4)
BHT is a skin and eye irritant. Levels of 5
to 10 times the level in processed foods caused brain and behavioral
changes in mice; the treated mice fought more and slept less than the
control group. Large doses of BHT in the food of rats, mice, cats, and
dogs caused liver weight increase, which was reversible in the rat
study where 500 mg/kg/day was given for two weeks. The LD50
for male rats was 1.7 g/kg. The FDA limits the BHT level in food to 2
ppm.
1.1.4 Physical properties (Ref. 5.3):
Synonyms: |
Butylated hydroxytoluene; 2,6-Bis
(1,1-dimethyl- ethyl)-4-methyl phenol; BHT; DBPC; Antracine 8;
2, 6-di- tert-butyl-4-methyl phenol; Tenox BHT; Annual CP;
Sustane; Dalpac; Impruvol; Vianol |
Molecular weight: |
220.34 |
Melting point: |
70°C |
Boiling point: |
265°C |
Flash point: |
127°C (261°F) |
Odor: |
light cresylic |
Color: |
white to pale yellow crystals |
Molecular formula: |
C15H240 |
CAS: |
128-37-0 |
IMIS: |
2683 |
RTECS: |
27354; G07875000 |
Structure:
 |
| 1.2 Limit defining parameters
1.2.1 The detection limit of the
analytical procedure is 0.333 µg/mL BHT in the desorbing solvent. This
is the smallest amount that could be detected under normal operating
conditions.
1.2.2 The overall detection limit is 0.01 mg/m³
BHT. (All mg/m³ amounts in this study are based on a 100-liter air
volume and a 3-mL desorption.) 1.3 Advantages
1.3.1 The sampling procedure is
convenient.
1.3.2 The analytical method is reproducible and
sensitive.
1.3.3 Reanalysis of samples is
possible.
1.3.4 It may be possible to analyze other compounds
at the same time.
1.3.5 Interferences may be avoided by proper
selection of column and GC parameters. 1.4 Disadvantages
None known.
2. Sampling procedure
2.1 Apparatus
2.1.1 A calibrated personal sampling
pump, the flow of which can be determined within ±5% at the
recommended flow.
2.1.2 The sampling media consists of OVS-7
tubes. The OVS-7 tubes are specially made 13-mm O.D.. glass tubes that
are tapered to 6-mm O.D.. These tubes are packed with a 13-mm diameter
glass fiber filter then a 270-mg sampling section followed by a 140-mg
backup section of purified XAD-7 resin, available from Alltech. There
is a foam plug between sampling section and backup section and after
the backup section. The glass fiber filter is held next to the
sampling section by a polytetrafluoroethylene (PTFE) retainer.
These tubes are commercially available through many
sources.
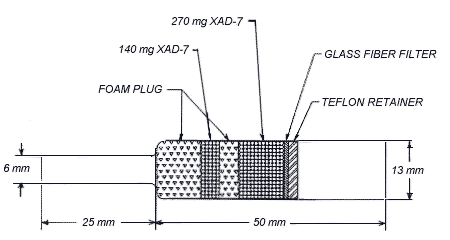
Figure 1. A
diagram of an OVS-7 tube. 2.2
Sampling technique
2.2.1 Remove the end caps of the
OVS-7, immediately before sampling.
2.2.2 Connect the OVS-7 to
the sampling pump with flexible tubing.
2.2.3 Place the tubes
in a vertical position to minimize channeling, with the smaller
section, towards the pump.
2.2.4 Air being sampled should not
pass through any hose or tubing before entering the
OVS-7.
2.2.5 Seal the OVS-7 with plastic caps immediately after
sampling. Seal each sample lengthwise with OSHA Form-21 sealing
tape.
2.2.6 With each batch of samples, submit at least one
blank tube from the same lot used for samples. This tube should be
subjected to exactly the same handling as the samples (break ends,
seal, & transport) except that no air is drawn through
it.
2.2.7 Transport the samples (and corresponding paperwork)
to the lab for analysis.
2.2.8 Bulks submitted for analysis
must be shipped in a separate mailing container from other
samples. 2.3 Desorption
efficiency
2.3.1 Two hundred seventy milligram
portions of XAD-7 resin were placed into separate 4-mL vials and six
portions were spiked at each loading of 0.1 mg (1 mg/m³), 0.5 mg (5
mg/m³), 1 mg (10 mg/m³), and 2 mg (2 mg/m³) BHT. They were allowed to
equilibrate overnight at room temperature. They were desorbed with 3
mL of the desorbing solution for 30 minutes with shaking, and were
analyzed by GC-FID. The overall average was 96.6%.(Table
2.3.1)
Table 2.3.1 Desorption
Efficiency
|
Portion # |
|
%
Recovered |
|
0.1 mg |
0.5 mg |
1.0 mg |
2.0 mg |
|
1 2 3 4 5 6 |
94.2 94.3 95.4 97.2 95.7 96.2 |
97.6 94.8 96.7 96.3 97.0 96.2 |
96.3 96.4 96.4 95.6 98.8 97.7 |
97.4 98.3 97.0 97.1 98.8 96.8 |
|
|
|
|
|
average |
95.5 |
96.4 |
96.9 |
97.6 |
overall
average standard deviation |
96.6 ±1.23 |
|
|
| 2.3.2 Six filters
were placed into separate mL vials and spiked at each loading of. 0.1
mg (1 mg/m³), 0.5 mg (5 mg/m³), 1 mg (10 mg/m³), and 2 mg (20 mg/m³)
BHT. They were allowed to equilibrate overnight at room temperature.
They were extracted with 3 mL of the desorbing solution for 30 minutes
with shaking, and were analyzed by GC-FID. The overall average was
100%.(Table 2.3.2)
Table 2.3.2 Desorption
Efficiency
|
Filter # |
|
%
Recovered |
|
0.1 mg |
0.5 mg |
1.0 mg |
2.0 mg |
|
1 2 3 4 5 6 |
99.3 99.4 101 101 100 100 |
99.5 99.5 99.9 101 99.3 100 |
101 99.2 101 99.0 98.5 98.7 |
100 100 101 101 101 98.7 |
|
|
|
|
|
average |
100 |
99.9 |
99.6 |
100 |
overall
average standard deviation |
100 ±0.863 |
|
|
| 2.4 Retention
efficiency
The filters of six OVS-7 tubes were spiked with 1.0 mg
(10 mg/m³) BHT, allowed to equilibrate for 6 hours, and had 100 liters
humid air (89% RH) pulled through them. The glass fiber filter was
placed before the Teflon spacer to insure that no BHT spiked onto the
filter was in contact with the XAD-7 sections before the humid air was
drawn. They were opened, desorbed, and analyzed by GC-FID. The retention
efficiency averaged 99.3%. There was no BHT found on the backup portions
of the tubes. The amount found on the front adsorbent portion of tile
OVS-7 tubes indicates that BHT is too volatile to be collected on glass
fiber filters. (Table 2.4)
Table 2.4 Retention Efficiency
|
Tube # |
% Recovered Filter |
% Recovered 'A' |
% Recovered 'B' |
Total |
|
1 2 3 4 5 6 |
65.7 65.9 53.1 65.9 71.7 73.2 |
34.4 34.3 44.7 34.5 28.5 25.0 |
0.0 0.0 0.0 0.0 0.0 0.0 |
100 100 97.8 100 100 98.2 |
|
|
|
|
|
|
|
|
average |
99.3 |
| 2.5
Storage
Glass fiber filters (GFF) from the OVS-7 tubes were
removed and spiked with 1.0 mg (10 mg/m³) BHT and were placed in a 4 mL
vial containing the front section of the XAD-7 resin from the OVS-7
tube, and stored at room temperature, in room light, until opened and
analyzed. The recoveries averaged 98.5% for the 14 days stored. The BHT
vaporized off of the glass fiber filters and was absorbed by the XAD-7
resin. The longer the samples were stored, the more of the BHT was
absorbed by the XAD-7 resin. (Table 2.5)
Table 2.5 Storage Study
|
Day |
GFF |
%
Recovered XAD-7 |
Total |
|
7 7 7 14 14 14 |
0.1 0.1 0.0 0.0 0.0 0.0 |
98.5 97.6 98.7 96.4 99.7 100
average |
98.6 97.7 98.7 96.4 99.7 100
98.5 |
| 2.6
Precision
The precision was calculated using the area counts from
six injections of each standard at concentrations of 33.3 µg/mL (1
mg/m³), 167 µg/mL (5 mg/m³), 333 µg/mL (10 mg/m³), and 667 µg/mL (2
mg/m³) BHT in the desorbing solvent. The pooled coefficient of variation
was 0.00904.(Table 2.6)
Table 2.6 Precision Study
|
Injection Number |
33.3 µg/mL |
167 µg/mL |
333 µg/mL |
667 µg/mL |
|
1 2 3 4 5 6
|
13243 13093 13313 13170 13229 13118
|
64377 63760 63894 65779 64064 64332
|
129549 129074 130334 132099 130739 132667
|
261860 259408 258086 261404 262641 260757
|
Average
Standard Deviation
CV
Pooled
CV |
13194
±82.9
0.00628
0.00904 |
64368
±732
0.0114 |
130744
±1408
0.0108 |
260693
±1680
0.00644 |
|
where: 
A(1), A(2), A(3), A(4) = # of
injections at each level CV1, CV2, CV3, CV4 = coefficients at
each level 2.7 Air
volume and sampling rate studied
2.7.1 The air volume studied is 100
liters.
2.7.2 The sampling rate studied is 1 liter per
minute. 2.8
Interferences
Suspected interferences should be listed on sample
data sheets.
2.9 Safety precautions
2.9.1 Sampling equipment should be
placed on an employee in a manner that does not interfere with work
performance or safety.
2.9.2 Safety glasses should be worn at
all times in designated areas.
2.9.3 Follow all safety
practices that apply to the workplace being sampled.
3. Analytical
method
3.1 Apparatus
3.1.1 Gas chromatograph equipped with
a flame ionization detector. A HP 5890 gas chromatograph was used in
this study.
3.1.2 GC column capable of separating the analyte
and an internal standard from any interferences. The column used in
this study was a 15-meter DB-WAX capillary column 0.25-µm d.f.,
0.32-mm I.D.
3.1.3 An electronic integrator or some other
suitable method of measuring peak areas.
3.1.4 Two and four
milliliter vials with Teflon-lined caps.
3.1.5 A 10-µL syringe
or other convenient size for sample injection.
3.1.6 Pipettes
for dispensing the desorbing solution. The Glenco 1-mL dispenser was
used in this method.
3.1.7 Volumetric flasks - 5 mL and other
convenient sizes for preparing standards.
3.1.8 An analytical
balance capable of weighing to the nearest 0.01 mg.
3.2 Reagents
3.2.1 Purified GC grade nitrogen,
hydrogen, and air.
3.2.2 Di-tert-butyl-p-cresol, Reagent
grade.
3.2.3 Methanol, HPLC grade.
3.2.4 Dimethyl
formamide, Reagent grade.
3.2.5 The desorbing solution is 0.25
µL/mL dimethyl formamide in methanol. 3.3 Sample preparation
3.3.1 Sample tubes are opened and the
glass fiber filter and the front and back section of each tube are
placed in separate 4-mL vials.
3.3.2 Each section is desorbed
with 3 mL of the desorbing solution.
3.3.3 The vials are sealed
immediately and allowed to desorb for 30 minutes on a shaker, a
roto-rack, or a sample rocker.
3.3.4 Samples were transferred
to two milliliter vials for analysis, as this was the size needed to
fit in the autosampler. 3.4
Standard preparation
3.4.1 Standards are prepared by
diluting a known quantity of BHT with the desorbing
solution.
3.4.2 At least two separate stock standards should be
made. Dilutions of the stock standards are prepared covering the
concentrations in the samples. The analytical standards used in this
study ranged from 0.000333 to 1.0 mg/mL of BHT in the desorbing
solution. 3.5
Analysis
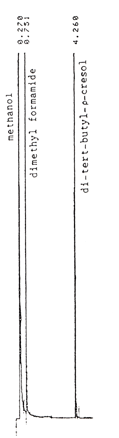 Figure 2. An analytical standard of 333 µg/mL BHT in
methanol with 0.25 µL/mL dimethyl formamide internal
standard.
3.5.1 Gas chromatograph conditions.
Flow rates
(mL/min) |
Temperature
(°C) |
|
Nitrogen (makeup) : Hydrogen
(carrier) : Air : Hydrogen (detector): Injection size
: Elution time : Chromatogram : |
30 1.5 450 60 1
µL 4.26 min (See Figure 2) |
Injector: Detector: Column: |
220 250 90°C - 1
min 10°C/min - 150°C | 3.5.2 Peak areas are measured by an integrator or other
suitable means. 3.6
Interferences (analytical)
3.6.1 Any compound having the general
retention time of the analyte or the internal standard used is an
interference. Possible interferences should be listed on the sample
data sheet. GC parameters should be adjusted if necessary so these
interferences will pose no problems.
3.6.2 Retention time data
on a single column is not considered proof of chemical identity.
Samples over the target concentration should be confirmed by GC/Mass
Spec or other suitable means. 3.7 Calculations
3.7.1 The instrument was calibrated
with a standard of 0.667 mg/mL BHT in the desorbing solution. The
linearity of the calibration is checked with a standards ranging from
0.000333 to 1 mg/mL BHT in the desorbing solution.
3.7.2 If the
calibration is non-linear, a calibration curve is plotted. The area
counts for the samples are plotted with the calibration curve to
obtain the concentration of BHT in solution.
3.7.3 To calculate
the concentration of analyte in the air sample the following formulas
are used:
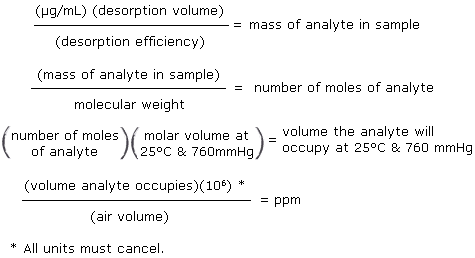
3.7.4 The above equations can be consolidated to form
the following formula. To calculate the ppm of analyte in the sample
based on a 100 liter air sample:
ppm = |
(µg/mL)(DV)(24.46)(106)(g)(mg)
(100 L)(DE)(MW)(1000 mg)(1000 mg) |
µg/mL 24.46 MW DV 100
L DE
|
= = = = = = |
concentration of analyte
in sample or standard Molar volume (liters/mole at 25°C and
760 mmHg. Molecular weight (g/mole) Desorption volume of 3
mL 100 liter air sample Desorption
efficiency | 3.7.5 This
calculation is done for each section of the sampling tube and the
results added together. 3.8
Safety precautions
3.8.1 All handling of solvents should
be done in a hood.
3.8.2 Avoid skin contact with all
chemicals.
3.8.3 Wear safety glasses, gloves and a lab coat at
all times. 4.
Recommendations for further study
Collection studies need to be
performed.
5. References
5.1 "NIOSH Manual of Analytical
Methods", U.S. Department of Health, Education, and Welfare, Public
Health Service, Center for Disease Control, National Institute for
Occupational Safety and Health, 1976, Method 226.
5.2 Cummins,
K., Method 32, "Phenol and Cresol", Organic Methods Evaluation Branch,
OSHA Salt Lake Technical Center, 1986.
5.3 Windholz, M., "The
Merck Index", Eleventh Edition, Merck & Co., Rahway N.J., 1989,
p.238.
5.4 "Documentation of the Threshold Limit Values and
Biological Exposure Indices", Fifth Edition, American Conference of
Governmental Industrial Hygienists Inc., Cincinnati, OH, 1986, p.
227.
|