1. General Discussion
1.1. Background
1.1.1. History of procedure
The OSHA Analytical Laboratory received a set of samples
requesting the analysis of 1,3,5-triglycidyl isocyanurate
(TGI) from glass fiber filters. Storage studies on glass fiber filters
yielded poor recoveries of TGI. Therefore, this report describes the
preliminary validation of a sampling and analytical method using glass
fiber filters coated with hydrobromic acid (HBr).
1.1.2. Toxic
effects (This section is for information only and should not be taken
as the basis of OSHA policy.) (Ref. 5.3.)
The oral
LD50 for rats is 400 mg/kg. The dermal LD50 for
rats is >3000 mg/kg.
1.1.3. Potential workplace exposure
No estimate of worker exposure to TGI could be found. TGI is a
solid resin that provides superior thermal, electrical, and mechanical
properties and is recommended for laminates, insulating varnishes,
coatings, and adhesives. (Ref. 5.2.)
1.1.4. Physical
properties (Ref. 5.1. to 5.3.)
Molecular weight: |
300.3 |
Molecular formula: |
C12H18N3O6 |
CAS #: |
2451-62-9 |
Specific gravity: |
1.4 at 25 °C |
Melting point: |
85-110 °C |
Solubility: |
soluble in
dimethylformamide, dimethylsulfoxide |
Synonyms: |
tris(2,3-epoxypropyl)isocyanurate |
Structure: |
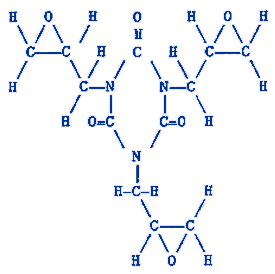 |
Description: |
white crystalline
powder | 1.2. Limit defining parameters
The detection limit
of the analytical procedure is 0.9 pg per injection. This is the amount
of analyte which will give a peak whose height is approximately five
times the baseline noise. (Figure 1) 2. Sampling procedure
2.1. Apparatus
2.1.1. Samples are collected by using
a personal sampling pump that can be calibrated to within ± 5% of the
recommended flow rate with the sampling device in line.
2.1.2.
Samples are collected with 37 mm Gelman type A/E glass fiber filters
treated with HBr. The filters are prepared by soaking each filter with
0.5 mL of HBr solution (25 mL of 48% hydrobromic acid solution in 75
mL of acetonitrile) and allowing them to air dry overnight. These
filters are further dried by placing them in a vacuum oven at 60°C for
two hours. The filters are assembled in two-piece 37 mm
polystyrene cassettes with backup pads. The cassettes are sealed with
shrink bands and the ends are plugged with plastic plugs.
2.2. Reagents
No sampling
reagents are required.
2.3. Sampling technique
2.3.1. Immediately before sampling,
remove the plastic plugs from the filter cassettes.
2.3.2.
Attach the cassette to the sampling pump with flexible tubing.
2.3.3. Attach the cassette vertically in the employee's
breathing zone in such a manner that it does not impede work
performance.
2.3.4. After sampling for the appropriate time,
remove the cassette and seal with plastic plugs.
2.3.5. Wrap
each sample end-to-end with an OSHA seal (Form 21).
2.3.6. Submit at least one blank for each set of samples.
Handle the blank in the same manner as the samples, except no air is
drawn through it.
2.3.7. Record the air volume (in liters of
air) for each sample, and list any possible interferences.
2.3.8. Submit bulk samples for analysis in a separate
container. 2.4. Extraction
efficiency
Five treated glass fiber filters were each liquid
spiked with 8 µL of a 2.005 mg/mL TGI standard. After two hours, the
samples were extracted with 3 mL of dimethylformamide (DMF) by shaking
them for 30 min and then analyzed as per section 3.5. The results are
listed in the table below.
Table 2.4. Extraction
Efficiency
|
Sample # |
Amount Spiked, µg |
Amount Found, µg |
% Recovered |
|
Ex1 |
16.04 |
15.81 |
98.6 |
Ex2 |
16.04 |
17.75 |
110.6 |
Ex3 |
16.04 |
16.57 |
103.3 |
Ex4 |
16.04 |
17.39 |
108.4 |
Ex5 |
16.04 |
17.54 |
109.4 |
|
Average =
106 | 2.5. Retention
efficiency
Six treated glass fiber filters were liquid spiked
with 8 µL of a 2.005 mg/mL standard and humid air (~80% relative humidity) was drawn
through each filter at 1 L/min for 60 minutes. The filters were
extracted with 3 mL of DMF by shaking them for 30 min and then analyzed
as per section 3.5. The results are listed in the table below.
Table
2.5. Retention Efficiency
|
Sample |
Amount Spiked, µg |
Amount Found, µg |
% Recovered |
|
R1 |
16.04 |
12.62 |
78.7 |
R2 |
16.04 |
14.28 |
89.0 |
R3 |
16.04 |
15.07 |
93.9 |
R4 |
16.04 |
16.97 |
105.8 |
R5 |
16.04 |
15.85 |
98.8 |
R6 |
16.04 |
16.43 |
102.4 |
|
Average =
94.8 | 2.6. Sample
storage
Twelve treated filters were liquid spiked with 8 µL of a
2.005 mg/mL standard and humid air (~80% relative
humidity) was drawn through each filter at 1 L/min for 60 minutes. Six
of the samples were stored at ambient temperature in a drawer, and six
were stored in a freezer. After four days of storage, three samples from
each group were extracted with 3 mL of DMF by shaking for 30 min and
then analyzed as per section 3.5. The remaining samples were desorbed
and analyzed after eight days of storage. The results are given in the
tables below.
Table
2.6.1. Ambient Storage
|
Days Stored |
Amount Spiked, µg |
Amount Found, µg |
% Recovered |
|
4 |
16.04 |
16.27 |
101.4 |
4 |
16.04 |
15.64 |
97.5 |
4 |
16.04 |
lost in analysis |
8 |
16.04 |
13.23 |
82.5 |
8 |
16.04 |
12.85 |
80.1 |
8 |
16.04 |
17.11 |
106.7 |
|
Average of 4 days =
99.4 |
|
Average of 8 days =
89.8 |
Table
2.6.2 Refrigerated Storage
|
Days Stored |
Amount Spiked, µg |
Amount Found, µg |
% Recovered |
|
4 |
16.04 |
17.16 |
107 |
4 |
16.04 |
17.15 |
107 |
4 |
16.04 |
17.20 |
107.2 |
8 |
16.04 |
13.06 |
81.4 |
8 |
16.04 |
17.1 |
106.6 |
8 |
16.04 |
15.84 |
98.8 |
|
Average of 4 days =
107 |
|
Average of 8 days =
95.6 | 2.7. Recommended
air volume and sampling rate
2.7.1. The recommended air volume is
60 L.
2.7.2. The recommended flow rate is 1.0 L/min.
2.8. Interferences
It is not
known if any compounds will interfere with the collection of TGI. Any
collected compound that reacts with the HBr may compete for the
derivatizing reagent on the filter.
2.9. Safety
precautions
2.9.1. Attach the sampling equipment
in such a manner that it will not interfere with work performance or
employee safety.
2.9.2. Follow all safety practices that apply
to the work area being sampled. 3. Analytical procedure
3.1. Apparatus
3.1.1. A balance capable of weighing
to the nearest tenth of a milligram. A Mettler HL52 balance was used
in this evaluation.
3.1.2. Mechanical shaker.
3.1.3. A
gas chromatograph (GC) equipped with an electron capture detector
(ECD). A Hewlett Packard 5890 was used in this evaluation.
3.1.4. A GC column capable of separating TGI from any
interferences. A 10 m x .32 mm i.d. (1.0 µm film) DB-5
column was used in this evaluation.
3.1.5. An electronic
integrator, or some other suitable method for measuring detector
response. The Hewlett-Packard 3357 Laboratory Data System
was used in this evaluation.
3.1.6. Volumetric flasks and
pipets.
3.1.7. Vials, 4-mL with
Teflon-lined caps.
3.1.8. Vials,
2-mL suitable for use on GC autosamplers.
3.2. Reagents
3.2.1. Dimethylformamide (DMF), high
purity Burdick and Jackson
3.2.2.
1,3,5-Triglycidyl isocyanurate, Polysciences, Inc.
3.2.3. Iso-octane, HPLC grade, Fisher Scientific
Co.
3.2.4. Heptafluorobutyric anhydride (HFBAnh), Pierce
Chemical Co.
3.2.5. High purity water, Milli-Q
filtered water, Millipore Inc.
3.2.6. Hydrobromic acid, 48%
solution, Fisher Scientific Co. 3.3. Standard preparation
Prepare stock TGI
standards by weighing 10 to 14 mg of TGI. Transfer the TGI to separate
10-mL volumetric flasks, and add DMF containing HBr (three
drops 48% HBr in 10 ml of DMF) to the mark. Make working range standards
of 0.4 to 10 µg/mL by pipet dilutions of the stock standards with DMF.
This range corresponds to 1.2 to 30 µg per sample when an extraction
volume of 3 mL is used. Store stock and dilute standards in a freezer.
3.4. Sample preparation
3.4.1. Transfer the glass fiber filter
of each cassette to a 4-mL vial.
3.4.2. Pipet 3.0
mL of DMF into each vial and seal with a Teflon-lined
caps.
3.4.3. Shake the vials for 30 minutes on a mechanical
shaker. 3.5. Derivatization of
samples and standards
3.5.1. Transfer 20 µL of each sample
and standard to 4-mL vials containing 2 mL of iso-octane.
3.5.2. Add 25 µL of HFBAnh to each vial.
3.5.3. Cap
the vials and shake for 10 to 15 s to ensure mixing and allow them to
sit at room temperature for 15 min.
3.5.4. Add 1 mL of
filtered water to each vial.
3.5.5. Recap the vials and shake
for 15 s.
3.5.6. After allowing the layers to separate,
transfer the iso-octane (upper) layer to
2-mL vials for analysis by GC. 3.6. Analysis
3.6.1. Instrument conditions
Column: |
DB-5, 1.0 µm film, 10 m x 0.32 mm i.d. |
Injector temperature: |
235 °C |
Column temperature: |
225 °C |
Detector temperature: |
300 °C |
Gas flows: |
Column 8.6 mL/min
hydrogen Make up 42 mL/min nitrogen |
Injection volume: |
1.0 µL |
Split ratio: |
5:1 |
Retention time: |
5.99
min | 3.6.2.
Chromatogram (see Figure 2) 3.7.
Interferences
3.7.1. Any collected compound having a
similar retention time and responds to an ECD is an interference.
3.7.2. Any compound that reacts with HFBAnh is an
interference.
3.7.3. GC conditions may be varied to circumvent
an interference.
3.7.4. Retention time alone is not proof of
chemical identity. Analysis by an alternate GC column and confirmation
by mass spectrometry are additional means of identification.
3.8. Calculations
3.8.1. A calibration curve (figure 3)
is constructed by plotting detector response versus total µg of TGI in
3 mL of volume.
3.8.2. The amount of TGI in a sample is
determined from the calibration curve.
3.8.3. The air
concentration is then determined by the following formula.
mg/m3 =
|
(total µg in
sample)
(air volume in liters) × (extraction
efficiency) | 3.9.
Safety precautions
3.9.1. Avoid skin contact and air
exposure to TGI.
3.9.2. Avoid skin contact with all
solvents.
3.9.3. Wear safety glasses at all times.
4.
Recommendation for further study
The method should be fully
validated.
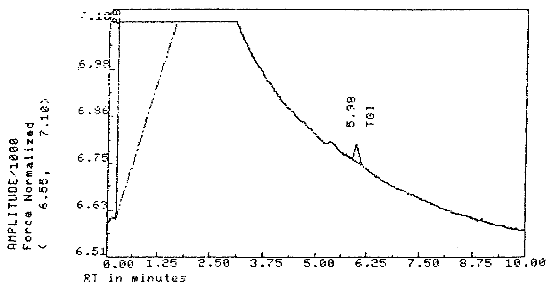 Figure
1 Chromatogram at the Detection Limit
|
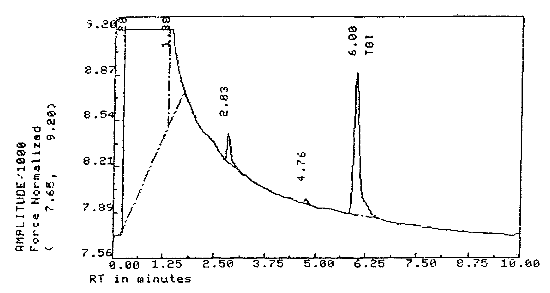 Figure 2 Chromatogram of TGI
|
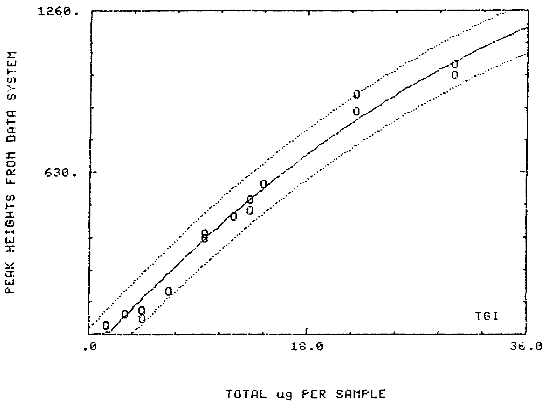 Figure 3 Calibration Curve
| 5. References
5.1. Kirk-Othmer
Encyclopedia of Chemical Technology; John Wiley & Sons: New
York, 1981, Volume 7, PP 400-401.
5.2. Kirk-Othmer Encyclopedia of Chemical Technology;
John Wiley & Sons: New York, 1981, Volume 9, PP 272-277.
5.3. "1,3,5-Triglycidyl Isocyanurate"
Material Safety Data Sheet, Polysciences Inc., Warrington,
Pennsylvania
|