|
This handout is intended to be a resource document for instructors of
occupational safety and health and is not a substitute for any of the provisions of the
Occupational Safety and Health Act of 1970 or for any standards issued by the U.S.
Department of Labor's Occupational Safety and Health Administration. It does not
necessarily reflect the views or policies of the U.S. Department of Labor, nor does
mention of trade names, commercial products, or organizations imply endorsement by the
U.S. Department of Labor. |
Respiratory
Protection
Frequently Asked Questions
Q: What is a respirator?
A: A respirator is a protective
facepiece, hood or helmet that is designed to protect the wearer against a variety of
harmful airborne agents.
Q: When is the use of respirators required?
A: OSHA's respirator standard, 29 CFR
1910.134, requires the use of respirators to protect employees from breathing contaminated
and/or oxygen-deficient air when effective engineering controls are not feasible, or while
they are being instituted. Several other OSHA regulations also require the use of
respirators.
Q: Can any respirator be used?
A: No, respirators shall be selected
on the basis of hazards to which the worker is exposed (i.e., particulates, vapors,
oxygen-deficiency, or combination). Also, OSHA requires the use of certified respirators.
Q: Who certifies respirators?
A: The National Institute for
Occupational Safety and Health (NIOSH).
Q: How can a certified respirator be recognized?
A: On July 10, 1995, 30 CFR Part 11
certification procedures were replaced by 42 CFR Part 84 procedures. Under the 30 CFR Part
11 approval system, manufacturers were required to mark cartridges and filters with an
abbreviated label that included a NIOSH/MSHA approval number ("TC number").
Under the 40 CFR Part 84 approval system, cartridges and filters are no longer marked with
a "TC number". Instead, they are marked with "NIOSH", the
manufacturer's name and part number, and an abbreviation to indicate the cartridge (e.g.,
OV, CL) or filter (e.g., N95, P100) type.
All cartridges and filters are to be supplied with a matrix approval label, usually as
an insert in the box. This label shows the NIOSH approved configurations and includes the
"TC number", component parts, and cautions and use limitations.
Nonpowered particulate respirators that were approved under 30 CFR Part 11 and use the
"old" labeling can be manufactured and sold until July 10, 1998. Distributors
will be able to sell them and end-users will be able to use them until their inventories
are depleted. Samples of approval labels are shown on the following two pages..
Q: Which class of Part 84 respirator should be used where a
particular OSHA standard requires the use of a respirator with HEPA filtration?
A: Where workers are exposed to a
hazard that would require the use of a respirator with HEPA filtration, the appropriate
class of respirator under the 42 CFR Part 84 certification is the Type 100 (N100, R100, or
P100).
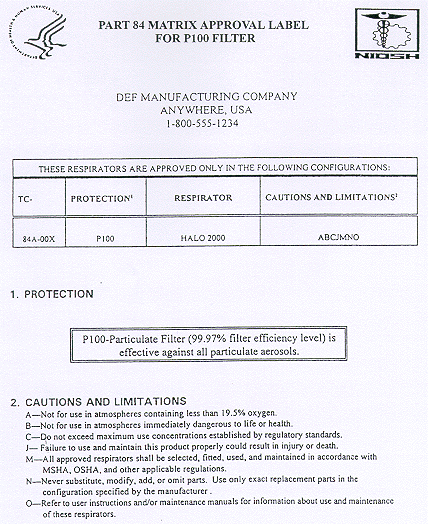
Q: Why is a formal respirator program needed?
A: A respirator program increases the
chances of using a respirator correctly. A respirator will only protect if it is used
correctly. Also, OSHA requires a number of written elements for all respiratory protection
programs.
Q: Who is in charge of the respirator program?
A: The program must be administered by
a trained program administrator who is qualified and knowledgeable in respiratory
protection to run all aspects of the program.
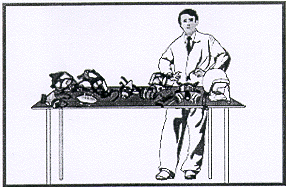
Q: What do employees need to know about the respirator
program?
A: Employers must establish and
implement a written respiratory protection program with worksite-specific procedures and
elements for required respirator use. The provisions of the program include procedures for
selection, medical evaluation, fit testing, training, use and care of respirators.
Q: How is the proper respirator size determined?
A: Proper respirator size is
determined through a fit test. Employees using negative or positive pressure tight-fitting
facepiece respirators must pass an appropriate fit test using the procedures detailed in
OSHA's respirator standard.
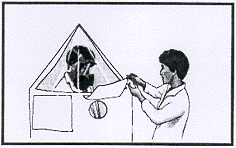
Qualitative Fit Test Chamber
Q: Can employees check the fit of their own respirator?
A: Yes, employees using tight-fitting
facepiece respirators are required to perform a user seal check each time they put on the
respirator. They must use the procedures in Appendix B-1 of 29 CFR 1910.134 or procedures
recommended by the respirator manufacturer that the employer demonstrates are as effective
as OSHA's procedures. Note that a fit test is a method used to select the right
size respirator for the user. A user seal check is a method to verify that the
user has correctly put on the respirator and adjusted it to fit properly, as illustrated
below.
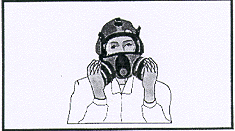
User Seal Check: worker covering inlet and inhaling
(negative pressure check)
Q: When is respirator fit testing required?
A: Fit testing of all negative or
positive pressure tight-fitting facepiece respirators is required prior to initial use,
whenever a different respirator facepiece is used, and at least annually thereafter. An
additional fit test is required whenever there are changes in the user's physical
condition that could affect respirator fit (e.g., facial scarring, dental changes,
cosmetic surgery, or an obvious change in body weight). The employer must be fit tested
with the same make, model, style, and size of respirator that will be used.
Q: What can be done if an employee has a very small face
and has trouble being fit tested for a respirator?
A: Manufacturers make several
different sizes. Respirators may also vary in size from manufacturer to manufacturer.
Users may be able to get a better fit by trying a respirator made by another manufacturer.
In some cases, the use of powered air-purifying respirators may be appropriate. Employers
must help employees find a suitable respirator.
Q: Must employees see a doctor before they use a
respirator?
A: The employer must provide a medical
evaluation to determine the employee's ability to use a respirator before the employee is
fit tested or required to use the respirator in the workplace. Not all workers must be
examined by a doctor. A physician or other licensed health care professional must perform
the medical evaluation using the medical questionnaire contained in Appendix C of 29 CFR
1910.134 or an initial medical examination that obtains the same information.

Q: What maintenance and care is required for respirators?
A:
The employer must provide for the cleaning and disinfecting, storage, inspection, and
repair of respirators used by employees according to the procedures in 29 CFR 1910.134.
Q: Can a respirator be used by more than one person?
How often should it be cleaned and disinfected?
A: Disposable respirators cannot be
disinfected, and are therefore assigned to only one person. Disposable respirators must be
discarded if they are soiled, physically damaged, or reach the end of their service life.
Replaceable filter respirators may be shared, but must be thoroughly cleaned and
disinfected after each use before being worn by a different person, using the procedures
in Appendix B-2 of 29 CFR 1910.134, or equally effective procedures recommended by the
manufacturer.
Q: How long can a particulate respirator be used before it
must be discarded?
A: Respirators with replaceable
filters are reusable, and a respirator classified as disposable may be reused by the same
worker as long as it functions properly. All filters must be replaced whenever they are
damaged, soiled, or causing noticeably increased breathing resistance (e.g., causing
discomfort to the wearer). Before each use, the outside of the filter material should be
inspected. If the filter material is physically damaged or soiled, the filter should be
changed (in the case of respirators with replaceable filters) or the respirator discarded
(in the case of disposable respirators).
Employers must develop standard operating procedures for storing, reusing, and
disposing of respirators that have been designated as disposable and for disposing of
replaceable filter elements.
Q: What is the proper way to store a respirator that is
used routinely?
A: Respirators must be stored to
protect them from damage, contamination, dust, sunlight, extreme temperatures, excessive
moisture, and damaging chemicals. They must also be packed or stored to prevent
deformation of the facepiece and exhalation valve. A good method is to place them in
individual storage bins. Keep in mind that respirator facepieces will become distorted and
the straps will lose their elasticity if hung on a peg for a long time. Check for these
problems before each use.
Storing the respirator in a plastic sealable bag after use is not considered a good
practice. The respirator may be damp after use and sealing prevents drying and encourages
microbial growth. If plastic bags are used, respirators must be allowed to dry before
storage.
Q: Are there any additional requirements for the storage of
emergency respirators?
A: Yes, emergency respirators must be
kept accessible to the work area and stored in compartments or in covers that are clearly
marked as containing emergency respirators, and stored in accordance with any applicable
manufacturer instructions.
Q: What are the employer's obligations when respiratory
protection is not required but employees wear respirators on their own accord?
A: The employer must implement those
elements of the written respiratory protection program necessary to ensure that any
employee using a respirator voluntarily is medically able to use that respirator, and that
the respirator is cleaned, stored, and maintained so its use does not present a health
hazard to the user. Also, employers must provide the voluntary respirator users with the
information contained in Appendix D of 29 CFR 1910.134.
Employers are not required to include in a written respiratory program those employees
whose only use of respirators involves the voluntary use of filtering facepieces (dust
masks).
Q: Is training required before a respirator is used?
A: Yes, training must be provided to
employees who are required to use respirators. The training must be comprehensive,
understandable, and recur annually, and more often if necessary. This training should
include at a minimum:

Why the respirator is necessary and how improper fit, use, or maintenance can
compromise its protective effect
Limitations and capabilities of the respirator
Effective use in emergency situations
How to inspect, put on and remove, use and check the seals
Maintenance and storage
Recognition of medical signs and symptoms that may limit or prevent effective
use
General requirements of OSHA's respirator standard, 29 CFR 1910.134
Q: What can be done if employees find it difficult to talk
with co-workers when wearing a respirator?
A: Some respirators may interfere with
speech more than others. Devices that enhance speech communication are available. Ask your
program administrator if there are alternatives.
Q: If employees have a beard or moustache, is their
respirator still effective?
A: Tight-fitting facepiece respirators
must not be worn by employees who have facial hair that comes between the sealing surface
of the facepiece and the face or that interferes with valve function. Respirators that do
not rely on a tight face seal, such as hoods or helmets, may be used by bearded
individuals.
Q: Can employees wear glasses while wearing a respirator?
A: Yes, but if an employee wears
corrective glasses or goggles or other personal protective equipment, the employer must
ensure that such equipment is worn in a manner that does not interfere with the seal of
the facepiece to the face of the user. Kits are available from all respirator
manufacturers that allow the mounting of prescription lenses inside the respirator.
Contact lenses can be worn with any type of respirator, but their use is not recommended
in dusty atmospheres while wearing a half-mask facepiece.
Q: If employees get a rash when they wear a respirator with
a latex seal, how can this be prevented?
A: Users might have an allergy or
sensitivity to the latex or its additives used in the manufacture of some respirators.
Changing to a respirator using a silicone-based compound for the face seal, or a
respirator that doesn't have a face seal (like a hooded PAPR) may solve the problem.
Employers must help employees find a respirator that does not cause this problem. |