|
Experimental
procedures that determine, under actual workplace conditions, whether
respirator cartridges are effectively protecting the worker are perhaps
the best measure of cartridge performance. Two procedures which have been included in the American Industrial Hygiene
Association seminar "Respirator Cartridges: How to Set a Replacement
Schedule" are outlined below. You should use these procedures on a systematic and frequent-enough basis to
verify your change schedule estimates. Your change schedule estimates must
be re-evaluated whenever operations change, or when work place conditions
are different than those used by equipment manufacturer's to determine
change schedules.
- Determine the change schedule per manufacturer’s recommendations
or by using one of the methods listed on OSHA’s Web page located at http://www.osha-slc.gov/SLTC/respiratory_advisor/mainpage.html.
- Immediately before changing the cartridges being used based on the
procedures determined in step 1, test for breakthrough using any
sampling method with sufficient sensitivity to detect the chemical of
interest below the Occupational Exposure Limit (OEL). These procedures
should be performed immediately after leaving the work area, and
should not be performed during the next work day. Methods that you may
use include detector tubes, direct reading instruments such as a
photoionization detectors, and charcoal tubes which require laboratory
analysis.
The OEL is normally the health based
workplace permissible exposure limit (PEL) or short term exposure limit
(STEL) required by OSHA standards. In cases where there is no OSHA
workplace exposure limit, use other exposure limits published by the
American Conference of Governmental Industrial Hygienists (ACGIH), the
American Industrial Hygiene Association, or the National Institute of
Occupational Safety and Health.
You can test by using one of the following procedures provide your
evaluate the respiratory hazard(s) to which the
employee is exposed, and use the procedure frequently enough to ensure
that workers are being protected by their respirators under the actual
workplace conditions.
Procedure 1: Using a leak free cartridge holder, adaptors,
inert tubing and tee such as teflon or stainless steel, sampling tube,
and a sampling pump as shown in Figure 1, draw air through the cartridge
being replaced. Perform sampling in a high exposure area so
that an adequate detection limit can be obtained. You can perform
sampling by attaching the sampling tube to the tee using a short piece
of tubing to minimize the "dead space" in the tubing. If
possible, insert the sampling tube directly into the
contaminant air stream in the tee. If breakthrough occurs, the cartridge
is no longer performing as designed and the change schedule should be
shortened. Therefore, shorten the change schedule by one hour and repeat
the test.
Figure 1.
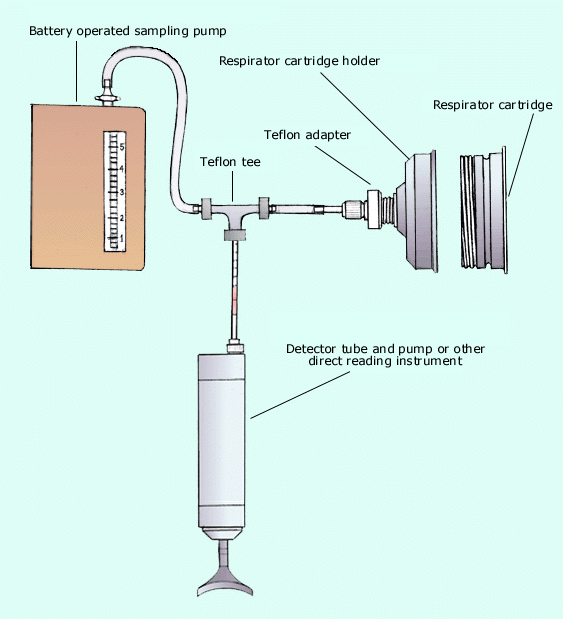
Procedure 2: Place a quantitative fit-testing (QNFT) sampling
adapter between the cartridge and the face piece (Fig. 2). These
adapters are often available through your respirator supplier.
Figure 2.
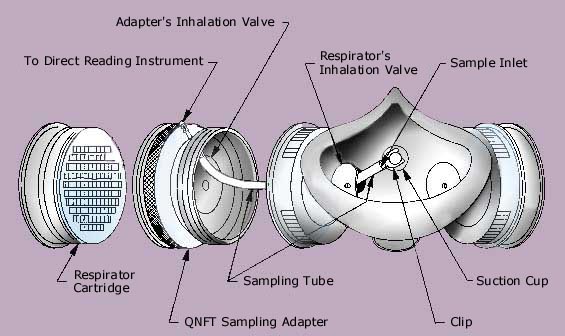
You can connect the direct reading instrument using a short piece of
tubing made of teflon or other inert material to the outer hose
connection on the adapter which, in turn, connects to a small inert
sample tube on the inside of the adaptor. Keep the length of tubing as short as possible to minimize the "dead space" in the
tubing. The sample tube passes through the respirator’s inhalation
valve and is firmly positioned via a small suction cup and clip so that
a sample can be drawn directly from the breathing zone of the respirator
(i.e., between the cartridge and the respirator).
If breakthrough occurs, the cartridge is no longer performing as
designed and the change schedule should be shortened. Therefore, shorten
the change schedule by one hour and repeat the test.
A reading on the instrument may not be due to breakthrough, but may be due to
other reasons such as a poor respirator fit, or exhalation of chemicals
that have been absorbed into through the skin. Check the respirator fit using a positive
and negative pressure test to verify that leakage is not occurring and
verify that any personnel protective equipment, such as gloves, is being
effectively used and that no skin absorption is occurring.
Since use of the QNFT adapter temporarily voids the respirator’s
NIOSH approval, it may be put in place only temporarily during a short equilibration
period before sampling to evaluate the change schedule.
- Reevaluate change schedules if employee exposure may increase
due to: (1) change in operations such as using more raw materials or
higher concentrations, (2) working without local exhaust ventilation
or other ventilation changes occur, (3) employee tasks or durations of
tasks change, or (4) employees experience symptoms of breakthrough
such as odor,
taste, or irritation. For compounds without adequate warning
properties, re-evaluate the change schedule any time an odor
is detected.
- Normally you should sample the toxic agent of interest. Sometimes,
adequate direct reading sampling procedures are not available for the
contaminant. In this case, a sampling method requiring a laboratory
analysis may be required. Or, in some cases, a surrogate may be used.
For example, a solvent carrier may be monitored if a direct reading
instrument is not available for the contaminant of interest. You
should use this variation only when calculations or manufacturer’s
recommendations indicate that the toxic compound of interest has a
longer breakthrough time than the solvent, and therefore the solvent
will break through first.
|