 |
METHYLENE BIS-(4-CYCLOHEXYLISOCYANATE)
(HMDI) |
 |
Method no.: |
PV2092 |
|
Control no.: |
T-PV2092-01-8804-CH |
|
Matrix: |
Air |
|
Target Concentration: |
0.055 mg/m3 or 0.005 ppm (ACGIH
TLV). |
|
Procedure: |
Samples are collected by drawing known volumes of air
through open-faced cassettes containing glass fiber filters coated
with 1.0 mg of 1-(2-pyridyl) piperazine (1-2PP). Samples are
extracted with 90/10 (V/V) acetonitrile/dimethyl sulfoxide
(ACN/DMSO) and analyzed by high performance liquid chromatography
(HPLC) using an ultraviolet (UV) or fluorescence
detector. |
|
Recommended air volume and sampling
rate: |
60 L at 1 L/min |
|
Detection limit of the overall
procedure (based on the recommended air volume):
|
0.4 µg/m3 |
|
Special requirements: |
If the coated glass fiber filters are to be stored for
any length of time before sampling, they should be kept in a
refrigerator. |
|
Status of method:
|
Stopgap method. This method has been only partially
evaluated and is presented for information and trial use. |
|
Date: April, 1988 |
Chemist: David B. Armitage |
|
|
|
Carcinogen And Pesticide Branch OSHA Analytical
Laboratory Salt Lake City, Utah
1. General Discussion
1.1 Background
1.1.1 History of procedure This evaluation was
undertaken to determine the effectiveness of a 1-2PP coated glass
fiber filter as a sampling device for HMDI. It follows the procedure
developed for methylene bisphenyl isocyanate (MDI). (Ref.
5.1)
1.1.2 Toxic effects (This section is for information only and
should not be taken as the basis of OSHA policy). HMDI
has a low oral toxicity with an LD 50 in rats of 9.9 g/kg. In addition
the chemical is a strong eye and skin irritant. Several other animal
studies are capsulized in the ACGIH document. (Ref.
5.2) Exposure of humans to HMDI has resulted in skin
sensitization, but only rarely in pulmonary sensitization. In this
respect it differs from other isocyanates (i.e., TDI and IPDI).
However it depresses respiration by producing pulmonary irritation.
(Ref. 5.2)
The ACGIH has suggested a change from a
ceiling value of 0.01 ppm to a TLV value of 0.005 ppm, the same as
TDI. This level will continue to prevent pulmonary irritation. (Ref.
5.2)
1.1.3. Potential workplace exposure No estimate of
worker exposure to HMDI could be found. HMDI is used primarily to
produce urethane products which will not yellow on exposure
to light. (Ref. 5.2.)
1.1.4. Physical properties (Ref. 5.2.)
Molecular weight: |
262.35 |
Molecular formula: |
C15H22N2O2
|
CAS #: |
5124-30-1 |
Melting point: |
< -10°C |
Specific gravity: |
1.07 |
Vapor pressure: |
0.4 mmHg at 150°C |
Appearance: |
colorless liquid |
Solubility: |
soluble in acetone. |
Synonyms: |
Desmodur W, HMDI, hydrogenated,
MDI |
Chemical name: |
Methylene
bis- (4-cyclohexylisocyanate) |
Structure:

(Mixture of several stereoisomers which elute as one major
peak)
1.2 Limit defining parameters
The detection limit of the
analytical procedure is 0.055 ng per injection. This is the amount
of analyte which will give a peak whose height is approximately five
times the baseline noise.
2. Sampling procedure
2.1 Apparatus
2.1.1 A personal sampling pump that can be calibrated to
within ±5% of the recommended flow rate with the sampling device
in line.
2.1.2 A three-piece styrene cassette containing a glass fiber
filter coated with 1.0 mg of 1-2PP and an untreated backup
pad.
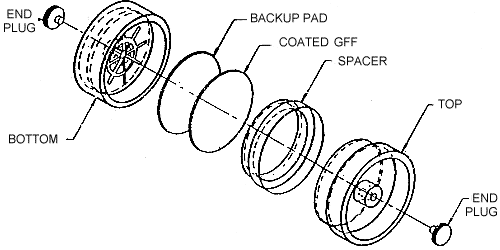
2.2 Glass fiber filter coating procedure Prepare a
solution of 2 mg/mL of 1-2PP in methylene chloride. Spike the glass
fiber filters with 0.5 mL of this solution. Allow the filters to air
dry, and then dry them in a 40°C vacuum oven for an additional 2
hours.
Store coated glass fiber filters in a closed jar at
reduced temperature as a precaution to prevent decomposition of the
1-2PP. Avoid exposure to strong sunlight.
2.3 Sampling
technique
2.3.1 Perform open-faced sampling by removing the top cover (with
small plug in place) from the three-piece cassette and the small plug
from the exit port.
2.3.2 Attach the cassette to the sampling pump with flexible,
plastic tubing such that the open face is vertically downward in the
worker's breathing zone and in such a manner that it does not impede
work performance.
2.3.3 After sampling for the appropriate time, remove the sampling
device and replace the small exit plug and the top cover.
2.3.4 Wrap each sample end-to-end with an OSHA seal (Form
21).
2.3.5 Submit at least one blank with each set of
samples. Handle the blanks the same as the other samples
except draw no air through them.
2.3.6 Submit any bulk samples in a separate container. Do not ship
them with the air samples.
2.4 Extraction efficiency
Nine 1-2PP coated glass fiber
filters were each liquid spiked with 12 µL of a DMSO solution of
HMDI 1-2PP derivative equivalent to 273 µg/mL HMDI. Three of these
filters, along with a blank filter, were extracted with 4.0 mL 90/10
(V/V) ACN/DMSO and then analyzed. The remaining six filters were used in
the retention and storage studies.
Table 2.4 Glass Fiber Filter Extraction Study
|
Filter # |
Amount Spiked |
Amount Recovered |
% Recovery |
|
E1 E2 E3 BL |
3.276 µg 3.276 µg 3.276 µg 0.00 µg |
3.203 µg 3.242
µg 3.262 µg 0.00 µg |
97.8 99.0 99.6 Blank |
|
Average Recovery is 98.8% |
2.5 Retention efficiency
The remaining six spiked
filters each had 60 liters of humid air (65% relative humidity) drawn
through them. Three of these filters were extracted with 4.0 mL
90/10,(V/V) ACN/DHSO and analyzed immediately. The remaining three
filters were stored at room temperature in a drawer for the storage
study.
Table 2.5 Retention Efficiency Study
|
Tube # |
Amount Spiked |
Amount Recovered |
% Recovery |
|
R1 R2 R3 |
3.276 µg 3.276 µg 3.276 µg |
3.260 µg 3.153
µg 3.147 µg
|
99.5 96.2 96.1 |
|
Average Recovery is 97.3% |
2.6 Sample storage
The remaining three spiked
filters were stored for a total of 7 days in a drawer at room
temperature. They were then extracted with 4.0 mL 90/10 (V/V) ACN/DMSO
and analyzed.
Table 2.6 Storage Study
|
Tube # |
Amount Spiked |
Amount Recovered |
% Recovery |
|
ST 1 ST 2 ST 3 |
3.276 µg 3.276 µg 3.276 µg |
3.217 µg 3.234
µg 3.133 µg
|
98.2 98.7 95.6 |
|
Average Recovery is 97.5% |
2.7 Recommended air volume and sampling rate
2.7.1 The recommended air volume is 60 L.
2.7.2 The recommended flow rate is 1 L/min.
2.8. Interferences Compounds such as acid chlorides,
anhydrides, and other isocyanates that react with the 1-2PP may compete
for the derivatizing agent on the glass fiber filter and diminish the
latter's effectiveness.
Suspected interferences should be
reported to the laboratory with submitted samples.
2.9
Safety precautions
2.9.1 Attach the sampling equipment in such a manner that it will
not interfere with work performance or employee safety.
2.9.2 Follow all safety practices that apply to the work area being
sampled.
3. Analytical procedure
3.1 Apparatus
3.1.1 A high performance liquid chromatograph equipped with
a UV or fluorescence detector, and manual or automatic injector.
A Waters M6000A pump, Waters 712 autosampler, Kratos Spectroflow
980 fluorescence detector, and a Waters 440 dual wavelength UV
detector were used in this evaluation.
3.1.2 An HPLC column capable of separating IPDI from any
interferences. A 25 cm × 4.6 mm i.d. Chromegabond 5 micron TMS column
was used in this evaluation.
3.1.3 An electronic integrator or other suitable means of measuring
detector response. A Hewlett-Packard 3357 data system was used in this
evaluation.
3.1.4 Vials, 4-mL glass with polytetrafluoroethylene (PTFE)-lined
septa.
3.1.5 Volumetric flasks, pipets, and syringes for
preparing standards, making dilutions, and performing
injections.
3.2 Reagents
3.2.1 HPLC grade ACN.
3.2.2 HPLC grade water. A Millipore Milli-OQ system was used
to prepare the water in this evaluation.
3.2.3 HPLC grade DMSO
3.2.4 HMDI 1-2PP derivative prepared by D.
Burright.
3.3 Standard preparation Prepare stock standard
solutions by adding DMSO to preweighed amounts of HMDI 1-2PP
derivative. Prepare working range standard solutions by diluting stock
solutions with 90/10 (V/V) ACN/DMSO.
Apply a correction
factor of 0.446 (F.W. of HMDI, 262.35 /F.W. of the 1-2PP derivative,
588.23) to express concentrations in terms of HMDI. Store stock and
dilute standards in a freezer. 3.4 Sample
preparation
3.4.1 Open the styrene cassette and place the coated glass fiber
filter in a 4-mL vial so that the filter is flat against the inside of
the vial. Do not fold or crumple it.
3.4.2 Add 4.0 mL of 90/10 (V/V) ACN/DMSO to each vial.
3.4.3 Seal the vials with PTFE-lined septa and allow them to
extract for one hour. Shake the vials by hand periodically during this
extraction time.
3.5 Analysis
3.5.1 Instrument conditions
Column: |
25 cm × 4.6 mm i.d. Chromegabond
5 micron TMS |
Mobile Phase: |
49.5% ACN/50.5% water, with 0.045 M
ammonium acetate buffer adjusted to pH 5.9 |
Flow rate: |
1 mL/minute |
Fluorescence Detector: |
excitation = 240 nm emission =
370 nm |
UV Detector: |
254 nm |
Retention time: |
11.5 minutes |
Injection volume: |
10 µL |
3.5.2 Chromatogram
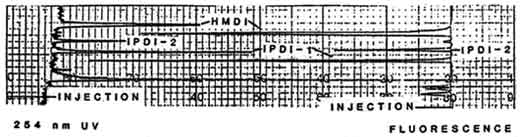
3.6 Interferences
3.6.1 Any compound having a similar retention time to the analyte
is a potential interference. Generally, chromatographic conditions can
be altered to separate an interference from the analyte.
3.6.2 Retention time on a single column is not proof of chemical
identity. Analysis by an alternate HPLC column, detection at another
wavelength, comparison of absorbance response ratios (or comparison of
UV to fluorescence response ratios), and confirmation by mass
spectrometry are additional means of identification.
3.7 Calculations
3.7.1 A calibration curve is constructed by plotting detector
response versus standard concentration.
3.7.2 The concentration of HMDI in a sample is determined from the
calibration curve.
3.7.3 The total HMDI concentration is then determined by the
following formula:

3.8 Safety precautions
3.8.1 Avoid exposure to all standards.
3.8.2 Avoid exposure to all solvents.
3.8.3 Wear safety glasses at all
times.
4. Recommendations for further study
This method should be fully validated.
5. References
5.1 "OSHA Analytical Methods Manual", U.S. Department of Labor,
Occupational Safety and Health Administration, OSHA Analytical
Laboratory: Salt Lake City, UT, Method 47, American Conference of
Governmental Industrial Hygienists (ACGIH): Cincinnati, OH, 1985, ISBN:
0-936712-X.
5.2 "Documentation of the Threshold Limit Values and Biological
Exposure Indices", American Conference of Governmental Industrial
Hygienists Inc., fifth edition, 1986.
|