TRIMELLITIC ANHYDRIDE
Method no.: |
98 |
|
|
|
|
Matrix: |
Air |
|
|
|
|
Target concentration: |
40 µg/m3 |
|
|
|
|
Procedure: |
Samples are collected open face on glass fiber
filters coated with veratrylamine
(3,4-dimethoxybenzylamine) and
di-n-octyl phthalate. Samples are extracted with
aqueous ammonium hydroxide and analyzed by HPLC using a UV
detector. |
|
|
|
|
Recommended air volume and sampling rate: |
480 L at 2.0 L/min |
|
|
|
|
Reliable quantitation limit: |
0.623 µg/m3 |
|
|
|
|
Standard error of estimate at the target
concentration: (Section 4.7.) |
6.4% |
|
|
|
|
Status of method: |
Evaluated method. This method has been subjected to
the established evaluation procedures of the Organic Methods
Evaluation Branch. |
|
|
|
|
Date: November 1992 |
Chemist: Yihlin Chan |
Organic Methods Evaluation Branch OSHA Salt Lake Technical
Center Salt Lake City, UT 84165-0200
1. General Discussion
1.1. Background
1.1.1. History
Over the years, many authors have reported air sampling and
analytical procedures for trimellitic anhydride (TMA). Purnell and
Warwick (1980, Ref. 5.1.) collected TMA on glass fiber filters,
extracted with aqueous sodium hydroxide, and analyzed by HPLC.
Palassis et al. (1981, Ref. 5.2.) collected TMA on DM-800
(PVC-copolymer) membrane filters, extracted with methanol, converted
TMA to trimethyl ester with boron trifluoride, and analyzed by
GC/FID. Geyer et al. (1986, Ref. 5.3.) also used glass fiber
filters, but extracted the samples with 0.05 M sodium hydroxide and
analyzed by HPLC using acidified mobile phase. A similar method was
published by Ledbetter et al. (1987, Ref. 5.4.) involving glass
fiber filters, acetonitrile/water extraction, and HPLC or GC/FID
analysis. The current (1990) NIOSH Method (Ref. 5.5.) was based on
the procedure of Palassis et al. However, all of these procedures
are susceptible to interference from trimellitic acid that is
present in the sampled air because none of them differentiates TMA
from trimellitic acid.
Rushing et al. (1982, Ref. 5.6.) presented an analytical method
for simultaneously determining TMA and trimellitic acid, whereby a
sample was dissolved in anhydrous ether and treated with
diazomethane. Under anhydrous conditions the anhydride functional
group was left intact and TMA was converted to monomethyl ester
whereas trimellitic acid was converted to trimetyl ester. However,
this procedure can not be applied to air samples because TMA will
react with water in the air to form trimellitic acid even in the
solid state at room temperature (Ref. 5.7.). TMA deposited on the
sampling filter will continually undergo hydrolysis as more air is
drawn through the filter.
OSHA has been using a partially evaluated method whereby TMA is
collected in 2-propanol bubblers. TMA is converted to mono-2-propyl
esters (two isomers) while trimellitic acid is not affected. They
are separated by HPLC. Problems with this procedure are that the use
of a bubbler is inconvenient, and trace amounts of water in
2-propanol, either present originally or collected during sampling,
may hydrolyze a portion of the TMA to the acid before it is
converted to the ester.
The method presented here uses coated filters for collecting
airborne TMA. Glass fiber filters are coated with veratrylamine in
order to derivatize TMA in situ. di-n-octyl
phthalate is added to improve the contact between the reactants. A
high sampling rate (2 L/min) is recommended in order to obtain
reasonable detection limits with short sampling times. Trimellitic
acid does not interfere because it does not react with
veratrylamine. The derivatized TMA (TMAVA) is stable. The sampler
has a capacity (at 80% relative humidity and 25°C) of 300 µg
or about 15 times the target concentration at the recommended air
volume. Two isomers of TMAVA are formed in about 1:1 ratio. They are
analyzed by HPLC, eluted either as a single peak or two separate
peaks, depending on the column used.
1.1.2. Toxic effects (This section is for information only and
should not be taken as the basis of OSHA policy.) (Refs. 5.8.-5.10.)
TMA causes severe respiratory irritation and sensitization.
Exposure may result in noncardiac pulmonary edema, immunological
sensitization, and irritation of the pulmonary tract, eyes, nose,
and skin. Repeated inhalation of TMA dust or fume over a period of
weeks to years can cause an allergic reaction: TMA binds to a
protein (human serum albumin) forming an antigen. In susceptible
individuals, the body then forms one or more types of antibodies
specific to the TMA-antigen. Upon re-exposure, the antibodies react
with the TMA-antigen and an allergic reaction occurs. TMA is listed
in the Table Z-1-A of the Code of Federal Regulations with a Final
Rule Limit of 0.04 mg/m3 TWA. ACGIH, in
its Notice of Intended Change, has set the TLV for TMA at 0.04
mg/m3 ceiling.
The pulmonary tract, eyes, nose, and skin all present a moist
environment, therefore it is not unreasonable to suspect that the
hydrolysis product, trimellitic acid, may be a contributor to the
toxic effects attributed to TMA. Despite the fact that this is not
established, much less addressed in the literature, the exposure
burden to trimellitic acid may be useful supplemental information.
Although this method has not been evaluated for trimellitic acid,
the analytical conditions presented allow the detection and
quantitation of the acid.
1.1.3. Workplace exposure (Refs. 5.1., 5.8.-5.9. and 5.11.)
Trimellitic anhydride is used as a curing agent for epoxy and
other resins. It is also used in vinyl chloride plasticizers,
various polymers and polyesters, agricultural chemicals, dyes and
pigments, paints and coatings, pharmaceuticals, surface active
agents, numerous modifiers and intermediates, and specialty
chemicals. A number of epoxy resin and surface coating systems,
containing between 2-10% TMA, are available as dry powder
formulations and are intended for application either by
electrostatic dry powder spraying or by dipping pre-heated articles
into fluidized beds. Primary occupational exposure to TMA may occur
from inhalation of airborne dust and fume when bulk material is
handled or during the application of dry powder formulations to
surfaces. In 1978, NIOSH estimated that approximately 20,000 U.S.
workers were at risk of exposure to trimellitic anhydride in its
various applications. The NIOSH 1972 National Occupational Hazard
Survey found 475 workers out of 3515 employed in nonmetallic mineral
products and engine electrical equipment industries were exposed to
TMA. The NIOSH 1982 survey found 97 workers of the total payroll of
269 in the printing ink industry were exposed.
1.1.4. Physical properties and other descriptive information
TMA |
(Refs. 5.12.-5.14.) |
|
|
|
|
CAS no.: |
552-30-7 |
synonyms: |
1,2,4-benzenetricarboxylic acid
1,2-anhydride; anhydro trimellic acid;
1,2,4-benzenetricarboxylic acid anhydride;
1,2,4-benzenetricarboxylic acid, cyclic
1,2-anhydride; 1,2,4-benzenetricarboxylic
anhydride; 4-caroxyphthalic anhydride;
1,3-dihydro-1,3-dioxo-5-isobenzofurancarboxylic
acid; 1,3-dioxo-5-phthalancarboxylic acid;
NCI-C56633; 5-phthalanacarboxylic
acid, 1,3-dioxo-; TMA; TMAN; trimellic acid
anhydride; trimellic acid 1,2-anhydride; trimellitic acid
cyclic 1,2-anhydride; trimellitic anhydride |
structural formula: |
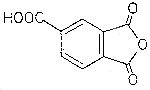 |
molecular wt: |
192.13 |
melting point: |
161-163.5°C |
boiling point: |
240-245°C at 1.9 kPa (14 mmHg); 390°C at 101.3
kPa (760 mmHg) |
appearance: |
white solid |
vapor pressure: |
5.3 × 10-7kPa (4 ×
10-6 mmHg) at 25°C; 0.3 kPa at
200°C; 2 kPa at 250°C; 11 kPa at 300°C |
flash point: |
227°C by the closed-cup method |
solubility: |
at 25°C, in g/100 g solvent: carbon
tetrachloride 0.002; ligroin 0.06; mixed xylenes 0.4;
dimethylformamide 15.5; acetone 49.6; ethyl acetate 21.6;
2-butanone 36.5; cyclohexanone 38.4 |
|
|
|
|
Derivatives (mixture of two
isomers) (personal observations) |
|
|
|
|
chemical name: |
N-(2,4-dicarboxybenzoyl)-N-(3,4-dimethoxybenzyl)amine
N-(2,5-dicarboxybenzoyl)-N-(3,4-dimethoxybenzyl)amine |
synonyms: |
TMAVA |
mixture melting point: |
133-138°C |
solubility: |
soluble in dilute ammonium hydroxide, methanol
(reacts slowly), acetone, chloroform |
appearance: |
white crystalline solid |
molecular wt: |
359.35 |
structural formula: |
|
 |
The analyte air concentrations throughout this method are based on
the recommended sampling and analytical parameters.
1.2. Limit defining parameters
1.2.1. Detection limit of the analytical procedure
The detection limit of the analytical procedure is 0.30 ng per
injection (10-µL injection of a 0.030 µg/mL solution).
This is the amount of analyte that will produce a peak with a height
that is approximately 5 times the baseline noise. (Section 4.1.)
1.2.2. Detection limit of the overall procedure
The detection limit of the overall procedure is 0.106 µg
per sample (0.221 µg/m3). This is
the amount of analyte spiked on the sampling device that, upon
analysis, produces a peak similar in size to that of the detection
limit of the analytical procedure. (Section 4.2.)
1.2.3. Reliable quantitation limit
The reliable quantitation limit is 0.299 µg per sample
(0.623 µg/m3). This is the smallest
amount of analyte which can be quantitated within the requirements
of a recovery of at least 75% and a precision (±1.96 SD) of ±25% or
better. (Section 4.3.)
The reliable quantitation limit and detection limits reported in
the method are based upon optimization of the instrument for the
smallest possible amount of analyte. When the target concentration of
analyte is exceptionally higher than these limits, they may not be
attainable at the routine operating parameters.
1.2.4. Instrument response to the analyte
The instrument response over concentration ranges representing
0.5 to 2 times the target concentration is linear. (Section 4.4.)
1.2.5. Recovery
The recovery of TMAVA from samples used in a 16-day ambient
storage test remained above 99%. (Section 4.5.)
1.2.6. Precision (analytical procedure)
The pooled coefficient of variation obtained from replicate
determinations of analytical standards at 0.5, 1 and 2 times the
target concentration is 0.032. (Section 4.6.)
1.2.7. Precision (overall procedure)
The precision at the 95% confidence level for the 16-day ambient
temperature storage test is ±12.5%. (Section 4.7.) This includes an
additional ±5% for sampling error.
1.2.8. Reproducibility
Six samples, collected from a test atmosphere of trimellitic
anhydride, and a draft copy of this procedure were given to a
chemist unassociated with this evaluation. The samples were analyzed
after 2 days of storage at room temperature. No individual sample
result deviated from its theoretical value by more than the
precision reported in Section 1.2.7. (Section 4.8.)
2. Sampling Procedure
2.1. Apparatus
2.1.1. A personal sampling pump that can be calibrated within
±5% of the recommended flow rate with the sampling device in line.
2.1.2. A four-piece polystyrene cassette containing two coated
glass fiber filters assembled as shown.
2.1.3. Treated glass fiber filters each coated with 10 mg of
veratrylamine (3,4-dimethoxybenzylamine) and 10 mg of
di-n-octyl phthalate (Kodak). They are prepared
as follows: Weigh 0.4 g of veratrylamine and 0.4 g of
di-n-octyl phthalate in a
scintillation vial. Add 16 mL of methanol and shake well. Place 40
glass fiber filters on a clean glass plate (a regular TLC plate).
Apply 0.4 mL of the methanol solution to each filter. Air dry for 5
minutes. Place filters in a wide-mouth jar. Dry under vacuum at room
temperature overnight. Store the coated filters in a refrigerator
and use within a month. Filters stored longer than this period
developed several small interfering peaks (believed to be
decomposition products of veratrylamine) in the HPLC chromatogram.
2.2. Reagents
No reagents are required for sampling.
2.3. Technique
2.3.1. Prepare the sampler for open-face sampling by removing
the top piece and the end plug from the bottom piece. Attach the
sampler to the sampling pump with a piece of flexible tubing and
place it in the worker's breathing zone with the open face of the
cassette facing down.
2.3.2. Replace the top piece and the end plug after sampling.
Seal each sample with an official Form OSHA-21.
2.3.3. Submit at least one blank with each set of samples. Handle
the blank the same as the other samples except draw no air through
it.
2.3.4. List any potential interferences on the sample data sheet.
2.4. Sampler capacity
Sampling capacity is approximately 300 µg at a sampling rate
of 2.0 L/min. This loading is equivalent to an air volume of 3750 L at
2 times the target concentration. (Section 4.9.)
2.5. Extraction efficiency (Section 4.10.)
2.5.1. The average extraction efficiency of TMAVA from the
treated glass fiber filters is 99%.
2.5.2. Extracted samples remain stable for at least 24 h.
2.6. Recommended air volume and sampling rate
2.6.1. For TWA samples the recommended air volume is 480 L at
2.0 L/min.
2.6.2. For short term samples the recommended air volume is 30 L
at 2.0 L/min (15-min samples).
2.6.3. When short term samples are required, the reliable
quantitation limit becomes larger. For example, the reliable
quantitation limit is 9.97 µg/m3
when 30 L of air is collected.
2.7. Safety precautions (sampling)
Attach the sampling equipment to the worker in such a manner that
it will not interfere with work performance or safety. Follow all
safety practices applicable to the work area.
3. Analytical Procedure
3.1. Apparatus
3.1.1. An HPLC equipped with a UV detector. A BAS 200 HPLC
(Bioanalytical Systems) and Waters WISP auto-sampler were used in
this evaluation.
3.1.2. An HPLC column capable of separating TMAVA from any
interferences. An Asahipak C4P-50 column (4.6 × 250 mm) (a polymeric
based C4 column, obtained from Keystone Scientific) was used in this
evaluation. A Nova-pak C18 column (8 × 100 mm) (Millipore Waters)
was used in the alternate HPLC conditions.
3.1.3. An electronic integrator or other suitable means of
measuring detector response. A Waters 860 Networking Computer System
was used in this evaluation.
3.1.4. Sample vials, 4-mL glass, with
poly(tetrafluoroethylene)-lined caps.
3.2. Reagents
3.2.1. Trimellitic anhydride. Trimellitic anhydride, 97%, was
obtained from Aldrich. The bottle was 10 years old, and the TMA
content was analyzed to be 93.5%.
3.2.2. Water, HPLC grade. Water was obtained from a Millipore
Milli-Q water purification system.
3.2.3. Extraction solution, 0.02 N ammonium hydroxide. The
extraction solution was prepared by diluting 5.28 mL of concentrated
ammonium hydroxide to 4 L with water.
3.2.4. Acetonitrile, HPLC grade. Acetonitrile, Optima grade, was
obtained from Fisher Scientific.
3.2.5. Phosphoric acid. Phosphoric acid, Baker Analyzed Reagent
grade, was obtained from J T Baker.
3.2.6. Veratrylamine. Veratrylamine, 97%, was obtained from
Aldrich.
3.2.7. Ethyl acetate. Ethyl acetate, B&J Brand High Purity
Solvent, was obtained from Baxter.
3.2.8. Toluene. Toluene, B&J Brand High Purity Solvent, was
obtained from Baxter.
3.2.9. Acetone. Acetone, B&J Brand High Purity Solvent, was
obtained from Baxter.
3.3. Standard preparation
3.3.1. Synthesis of TMAVA:
Dissolve TMA (97%, 1.98 g, 0.01 mole) in 50 mL of ethyl acetate.
Dilute veratrylamine (97%, 1.72 g, 0.01 mole) with 20 mL of ethyl
acetate. With constant stirring, slowly add the TMA solution to the
veratrylamine solution. Sonicate the mixture for 1 h. Collect the
resulting white precipitate. The yield of the first crop should be
approximately 81%. Recrystallize from acetone/toluene. Melting point
(capillary tube): 133°C-138°C.
3.3.2. Prepare stock standards by
weighing 10-20 mg of TMAVA in 10-mL volumetric flasks and diluting
to volume with the extraction solution. Apply a factor of 0.5347 to
the weight of TMAVA to convert it to that of TMA. For example, 10 mg
of TMAVA dissolved in 10 mL will give a standard stock solution
representing 534.7 µg/mL of TMA.
(MW TMA)/(MW TMAVA) = 192.13/359.35
= 0.5347
3.3.3. Alternately, TMA of known purity may be weighed and
derivatized with excess veratrylamine in acetonitrile. Weigh 10-15
mg of TMA in a 10-mL volumetric flask. Add 2 mL of acetonitrile and
2 drops of veratrylamine. Sonicate for 15 min. Add the extraction
solvent to mark.
3.3.4. Prepare analytical standards by diluting the stock
standards with extraction solvent. A 6.4 µg/mL standard
solution corresponds to the target concentration.
3.3.5. Prepare a sufficient number of analytical standards to
generate a calibration curve. Analytical standard concentrations
must bracket sample concentrations.
3.4. Sample preparation
3.4.1. Transfer the two filters to separate 4-mL glass vials.
3.4.2. Add 3.0 mL of the extraction solution to each vial.
3.4.3. Cap the vials and shake them on a mechanical shaker for 30
min.
3.5. Analysis
3.5.1. HPLC conditions
column: |
Asahipak C4P-50 |
eluent: |
acetonitrile/water/phosphoric acid,
25/75/0.1 |
flow rate: |
0.8 mL/min |
injection vol: |
10 µL |
UV detector: |
205 nm |
alternate l: |
232 nm |
ret. times: |
trimellitic acid 7.1 min TMAVA 12.8
min |
Figure 3.5.1. Chromatogram of a mixture of TMAVA (6.27
µg/mL) and trimellitic acid (6.12 µg/mL). Key: (1)
trimellitic acid, (2) TMAVA.
3.5.2. Alternate HPLC conditions
column: |
Novapak C18 |
eluent: |
acetonitrile/water/phosphoric acid,
22.5/77.5/0.1 |
flow rate: |
1.0 mL/min |
injection vol: |
10 µL |
UV detector: |
205 nm |
alternate l: |
232 nm |
ret. times: |
trimellitic acid 1.75 min TMAVA isomers 5.2
min and 6.6 min |
Figure 3.5.2. Chromatogram of a mixture of TMAVA (6.27
µg/mL) and trimellitic acid (6.12 µg/mL) under the
alternate analytical conditions. Key: (1) trimellitic acid, (2) and
(3) TMAVA isomers.
3.5.3. Construct a calibration curve using an external standard
method by plotting micrograms per milliliter versus detector
response of standards. If the two isomers are separated, sum the
peak areas.
3.6. Interferences (analytical)
3.6.1. Any compound that absorbs at 205 nm and has a similar
retention time as the analyte is a potential interference.
Generally, chromatographic conditions can be altered to separate an
interference from the analyte.
3.6.2. Retention time on a single column is not considered proof
of chemical identity. Additional means of identification could
involve: analysis using an alternate HPLC column, detection at
another wavelength (peak ratioing), and GC/MS. The mass spectrum
obtained from GC/MS showed the base peak at m/e 297, representing
the cyclic imide, apparently produced through decarboxylation and
cyclization in the GC.
3.7. Calculations
The analyte amount for a sample is obtained from the calibration
curve in terms of micrograms per milliliter uncorrected for extraction
efficiency. The analyte amount is corrected by subtracting the amount
found in the blank. The air concentration is obtained by using the
following equation.
where |
A |
= |
micrograms of analyte per milliliter (blank
corrected) |
|
B |
= |
extraction volume |
|
C |
= |
liters of air sampled |
|
D |
= |
extraction efficiency |
3.8. Safety precautions (analytical)
3.8.1. Restrict the use of all chemicals to a fume hood.
3.8.2. Avoid skin contact and inhalation of all chemicals.
3.8.3. Wear safety glasses, gloves and a lab coat at all times
while working with chemicals.
4. Backup Data
4.1. Detection limit of the analytical procedure
The injection size recommended in the analytical procedure (10
µL) was used in the determination of the detection limit of the
analytical procedure. The detection limit of 0.30 ng on-column was
determined by analyzing a dilute standard of TMAVA (0.030
µg/mL). This amount gave a peak with a height about 5 times the
height of the baseline noise.
Figure 4.1. Detection limit of the analytical procedure. Key: (1)
TMAVA.
4.2. Detection limit of the overall procedure
The detection limit of the overall procedure was determined by
analyzing filters liquid spiked with 0.106 µg of TMAVA. This
amount corresponds to an air concentration of 0.221
µg/m3. The injection size listed in
the analytical procedure (10 µL) was used in the determination
of the detection limit of the overall procedure.
Table 4.2. Detection Limit of the Overall
Procedure
|
µg |
µg |
percent |
spiked |
recovered |
recovered |
|
0.106 |
0.118 |
111.3 |
0.106 |
0.132 |
124.5 |
0.106 |
0.184 |
173.6 |
0.106 |
0.114 |
107.5 |
0.106 |
0.098 |
92.5 |
0.106 |
0.118 |
111.3 |
|
4.3. Reliable quantitation limit
The reliable quantitation limit was determined by analyzing filters
liquid spiked with 0.299 µg of TMAVA. This amount corresponds
to an air concentration of 0.623
µg/m3. The recovery of the analyte
from the spiked samples was greater than 75% with a precision of ±25%
or better.
Table 4.3. Reliable Quantitation Limit
|
µg |
µg |
percent |
spiked |
recovered |
recovered |
|
0.299 |
0.296 |
99.0 |
0.299 |
0.293 |
98.0 |
0.299 |
0.292 |
97.7 |
0.299 |
0.294 |
98.3 |
0.299 |
0.285 |
95.3 |
0.299 |
0.283 |
94.6 |
|
mean =
97.2% |
SD =
1.8% |
precision =
3.5% |
|
4.4. Instrument response to the analyte
The instrument response to TMAVA over the range of 0.5 to 2 times
the target concentration was determined from multiple injections of
analytical standards. The response is linear with a slope of 2.08 ×
104 area counts per microgram per
milliliter.
Table 4.4. Instrument Response
|
× target concn |
0.5× |
1.0× |
2.0× |
µg/mL |
3.21 |
6.42 |
12.83 |
|
area counts |
61041 |
131012 |
265178 |
|
66302 |
134085 |
266730 |
|
63616 |
136377 |
264288 |
|
65737 |
137022 |
262804 |
|
65851 |
121815 |
261018 |
|
65042 |
126993 |
265654 |
|
65042 |
126993 |
265654 |
|
mean |
64598 |
131217 |
264279 |
|
Figure 4.4. Calibration curve for TMAVA.
4.5. Storage data
Storage samples were prepared from a test atmosphere of TMA
aerosol. The generation of TMA aerosol is described in detail in
Section 4.9. Thirty-six samples were collected from the chamber in two
sessions. Six samples were analyzed immediately. The rest of the
samples were divided into two groups: 15 were stored in a refrigerator
at 5°C, and the other 15 were stored in a closed drawer at about 22°C.
Six samples, three from each group, were analyzed at intervals over a
period of sixteen days. The average concentration of the day 0
samples, which was 53.6 µg/m3, was
set at 100% (no loss due to storage). The recovery of the analyte from
the samples stored at ambient temperature remained above 98.9% (from
the regression line).
Table 4.5. Storage Test
|
days of storage |
% recovery (ambient) |
|
%
recovery (refrigerated) |
|
0 0 3 6 9 14 16 |
102.2 98.7 94.3 101.3 105.5 98.7 96.4 |
98.2 104.8 104.1 109.5 102.0 98.9 92.8 |
97.3 98.7 95.2 99.9 100.4 100.8 97.8 |
|
102.2 98.7 102.7 98.2 111.6 97.5 93.6 |
98.2 104.8 94.0 111.6 99.6 97.3 96.8 |
97.3 98.7 108.3 103.4 100.4 99.2 102.9 |
|
Figure 4.5.1. Storage test at ambient temperature.
Figure 4.5.2. Storage test at reduced temperature (5°C).
4.6. Precision (analytical method)
The precision of the analytical procedure is defined as the pooled
coefficient of variation determined from replicate injections of
analytical standards representing 0.5, 1, and 2 times the target
concentration. The coefficients of variation are calculated from the
data in Table 4.4. The pooled coefficient of variation is 0.032.
Table 4.6. Precision of the Analytical Method (Based on
the Data of Table 4.4.)
|
× target concn |
0.5× |
1.0× |
2.0× |
µg/mL |
3.21 |
6.42 |
12.83 |
|
SD1 |
1979 |
5913 |
2074 |
CV |
0.031 |
0.045 |
0.008 |
|
1 - in area
counts |
4.7. Precision (overall procedure)
The precision of the overall procedure is determined from the
storage data. The determination of the standard error of estimate
(SEE) for a regression line plotted through the graphed storage data
allows the inclusion of storage time as one of the factors affecting
overall precision. The SEE is similar to the standard deviation,
except it is a measure of dispersion of data about a regression line
instead of about a mean. It is determined with the following equation:
where |
n |
= |
total number of data points |
|
k |
= |
2 for linear regression |
|
k |
= |
3 for quadratic regression |
|
Yobs |
= |
observed percent recovery at a given time |
|
Yest |
= |
estimated percent recovery from the regression
line at the same given time |
An additional 5% for pump error is added to the SEE by the addition
of variances. The precision at the 95% confidence level is obtained by
multiplying the SEE (with pump error included) by 1.96 (the
z-statistic from the standard normal distribution at the 95%
confidence level). The 95% confidence intervals are drawn about their
respective regression line in the storage graph as shown in Figure
4.5.1. The data for Figure 4.5.1. were used to determine the SEE of
±6.39% and the precision of the overall procedure of ±12.5%.
4.8. Reproducibility data
Six samples were collected from a test atmosphere of trimellitic
anhydride aerosol at 25°C and 80% RH. A draft copy of this method and
the samples were submitted to a chemist unassociated with this
evaluation for analysis. All of the sample results were within the
range of ±12.5%, the precision of the overall procedure.
Table 4.8. Reproducibility Data
|
µg/m3 |
µg/m3 |
percent |
percent |
expected |
found |
found |
deviation |
|
40.9 |
40.8 |
99.8 |
-0.2 |
40.9 |
41.4 |
101.2 |
+ 1.2 |
40.9 |
40.9 |
100.0 |
0.0 |
40.9 |
41.0 |
100.2 |
+ 0.2 |
40.9 |
40.4 |
98.8 |
-1.2 |
40.9 |
40.7 |
99.5 |
-0.5 |
|
4.9. Sampler capacity
The sampler capacity was assessed by sampling from a dynamically
generated test atmosphere of TMA at 25°C and 80% RH. The test
atmosphere of TMA aerosol was generated by pumping an ethyl acetate
solution of TMA at a rate of 0.8 mL/min through a TSI Model 3076
atomizer (TSI Incorporated, St. Paul, MN), where it was dispersed with
an air stream of 3.5 L/min. The aerosol passed through an
electrostatic charge neutralizer and was mixed with a dilution air
stream of 97 L/min (25°C, 80% RH). The diluted aerosol flowed into a
chamber containing 18 sampling ports. Each port was fitted with a
sampler. After an appropriate equilibration time, sampling was started
at 2 L/min. Three samplers were removed every hour. Both the front and
the back filters were analyzed for TMAVA and trimellitic acid. Many
experiments were run, with different concentrations of TMA feed
solution ranging from 60 µg/mL to 1500 µg/mL (actual TMA
content of the feed solution was 93.5%, with 6.5% trimellitic acid).
The "total" aerosol concentration (sum of trimellitic acid and
trimellitic anhydride) obtained ranged from 0.08 to 2.3
mg/m3. No TMAVA or trimellitic acid was
detected on the back filter after 6 h of sampling at a total
concentration of 2.3 mg/m3. The front
filters contained TMAVA and trimellitic acid in a ratio of 90/10
indicating that the aerosol contained approximately 90% trimellitic
anhydride and 10% trimellitic acid. Apparently some of the TMA (about
3.5%) in the feed solution was hydrolyzed by the humid air during the
short path from the atomizer to the test chamber. This 90/10 ratio
remained constant at lower concentrations, but began to decrease at
higher concentrations and longer sampling time, indicating that some
of the TMA collected on the filter at later stages failed to be
derivatized. The plot of the amount of TMAVA collected against the
total amount collected (TMAVA and trimellitic acid) showed that the
"failure point" occurred at about 300 µg of TMAVA. Beyond this
point, some of the TMA deposited on the filter was hydrolyzed by the
water in the air before it could react with the derivatizing agent.
This failure point is equivalent to 3750 L at 2 times the target
concentration.
Figure 4.9. Sampler capacity. Data from five different runs
covering high and low concentration ranges.
4.10. Extraction efficiency and stability of extracted samples
4.10.1. Extraction efficiency
To determine the extraction efficiency, six glass fiber filters
were liquid spiked with TMAVA at the target concentration. These
samples were stored overnight at ambient temperature and then
extracted with the extraction solvent and analyzed. The average
recovery was 99.0%.
Table 4.10.1. Extraction Efficiency
|
sample no. |
µg spiked |
µg recovered |
% recovery |
|
1 |
19.09 |
19.21 |
100.6 |
2 |
19.09 |
18.84 |
98.7 |
3 |
19.09 |
18.67 |
97.8 |
4 |
19.09 |
19.12 |
100.2 |
5 |
19.09 |
17.94 |
94.0 |
6 |
19.09 |
19.54 |
102.4 |
|
mean |
|
99.0 |
|
4.10.2. Stability of extracted samples
The stability of extracted samples was ascertained by reanalyzing
the above samples 24 h later with fresh standards. The samples were
stored at room temperature and were not recapped. The average
recovery was 99.2%.
Table 4.10.2. Stability of Extracted Samples
|
initial recovery (%) |
recovery after 24 h (%) |
percent change |
|
100.6 |
100.4 |
-0.2 |
98.7 |
100.1 |
+ 1.4 |
97.8 |
99.7 |
+ 1.9 |
100.2 |
99.9 |
-0.3 |
94.0 |
97.4 |
+ 3.4 |
102.4 |
97.6 |
-4.8 |
|
5. References
5.1. Purnell, C.J. and C.J. Warwick, J. High Resolut.
Chromatogr. Chromatogr. Commun., 1980, 3, 482-484.
5.2. Palassis, J., J.C. Posner, E. Slick and K. Schulte, Am.
Ind. Hyg. Assoc. J., 1981, 42(11), 785.
5.3. Geyer, R., R.C. Jones, and N. Mezin, J. High Resolut.
Chromatogr. Chromatogr. Commun., 1986, 9(5),
308-309.
5.4. Ledbetter, A.D., C.L. Leach, N.S. Hatoum and J-C. Roger,
Am. Ind. Hyg. Assoc. J., 1987, 48(1), 35-38.
5.5. NIOSH Manual of Analytical Methods, 3rd ed., U.S.
Department of Health and Human Services, Center for Disease Control,
National Institute of Occupational Safety and Health; DHHS (NIOSH)
Publication No. 90-121, U.S. Government Printing Office, Washington,
DC, 1990; Method No. P&CAM 322.
5.6. Rushing, L.G., J.R. Althaus, and H.C. Thompson, Jr., J.
Anal. Toxicol., 1982, 6, 290-293.
5.7. Towle, P.H., et al., in Kirk-Othmer Encyclopedia of
Chemical Technology, Standen, A., Ed., 2nd ed., John Wiley &
Sons, New York, NY, 1968; Vol. 15, p 473.
5.8. "Notice of Intended Change - Trimellitic Anhydride", Appl.
Occup. Environ. Hyg., 1991, 6(7), 625.
5.9. Current Intelligence Bulletin 21: Trimellitic Anhydride
(TMA), U.S. Department of Health, Education, and Welfare, Center
for Disease Control, National Institute of Occupational Safety and
Health, DHEW (NIOSH) Publication No. 78-121, U.S. Government Printing
Office, Washington, DC, 1978.
5.10. "Table Z-1-A -- Limits for Air Contaminants", Code of
Federal Regulations, Title 29; 1910.1000, U.S. Office of the
Federal Register National Archives and Records Administration,
Washington, DC; 1991.
5.11. OSHA Computerized Information System Database, OSHA Regulated
Substances (PEL Standard) Profiles, Trimellitic Anhydride, Revision
Date: 08/15/88, OSHA SLTC, Salt Lake City, UT.
5.12. Merck Index, Budavari, S., Ed., 11th ed., Merck &
Co., Rahway, NJ, 1989; p 1386.
5.13. Registry of Toxic Effects of Chemical Substances,
Sweet, D.V., Ed.,1985-86 edition, U.S. Department of Health and Human
Services, DHHS (NIOSH) Publication No. 87-114, Government Printing
Office, Washington, DC, 1987; Vol. 1, p 851.
5.14. Bemis, A.G., et al., in Kirk-Othmer Encyclopedia of
Chemical Technology, Grayson, M., et al., Ed., 3rd ed., John Wiley
& Sons, New York, NY, 1982; Vol. 17, p 764.
|