IODINE IN WORKPLACE ATMOSPHERES (IMPREGNATED ACTIVATED
BEADED CARBON)
Method Number: |
ID-212 (This method supersedes ID-177) |
|
Matrix: |
Air |
|
OSHA Permissible Exposure Limits Final
Rule Limit*: |
0.1 ppm (Ceiling) |
|
Transitional Limit: |
0.1 ppm (Ceiling) |
|
Collection Device: |
An air sample is collected using a calibrated
sampling pump and a glass tube containing impregnated activated
beaded carbon (IABC). A modified sampling tube (MST) can be used to
preclude any iodide-containing particulate, if
necessary. Loss of iodine using IABC has been noted when sampling
in relative humidities (RHs) > 50%. See Special Precautions
below. |
|
Recommended Sampling Rate: |
0.5 liter per minute (L/min) |
|
Recommended Minimum Sampling Time: |
5 min |
|
Analytical Procedure: |
The sampling medium is desorbed using an aqueous
solution containing 1.5 mM sodium carbonate
(Na2CO3) and 1.5
mM sodium bicarbonate (NaHCO3). An aliquot
of this solution is analyzed for iodine (as iodide, I-)
by an ion chromatograph equipped with a pulsed electrochemical
detector (PED). |
|
Detection
Limit Qualitative: Quantitative: |
0.0004 ppm as I2 (2.5-L
air sample) 0.0010 ppm as I2 (2.5-L air
sample) |
|
Precision and Accuracy Validation
Range: CVT(pooled): Bias: Overall
Error: |
0.05 to 0.20
ppm 0.045 -0.025 ±11.5% |
|
Method Classification: |
Interim Method (See Special Precautions below) |
|
Special Precautions: |
1) Loss of iodine has been noted when sampling in
>50% RH. See Sections 2 and 4.6. for details. The loss in
relation to humidity is concentration-dependent. Due to the
dependence on humidity, this method is considered an interim
procedure until alternate sampling can be explored further.
2) Samples should be shipped for laboratory analysis as soon as
possible. |
|
Chemist: |
James C. Ku |
|
Date: |
May, 1994 |
* The U.S. Court of Appeals, Eleventh Circuit, has ruled that Final
Rule Limits of 29 CFR 1910.1000 be vacated. The Transitional Rule Limits
are currently in effect and in the case of iodine the limits are identical
in value. The Final Rule definition of a "Ceiling" has been retained (See
Federal Register, Vol. 58, No. 124, Wednesday June 30, 1993 p.35339 for
further details regarding the ceiling definition).
Commercial manufacturers and products mentioned in this method
are for descriptive use only and do not constitute endorsements
by
USDOL-OSHA.
Similar products from other sources can be substituted.
Branch of Inorganic Methods Development OSHA Salt Lake
Technical Center Salt Lake City, Utah
1. Introduction
This method describes the sample collection and analysis of airborne
iodine (I2). Samples are taken in the breathing
zone of workplace personnel, and analysis is performed by ion
chromatography (IC) equipped with a pulsed electrochemical detector (PED).
1.1. History
Previously, iodine vapor in the workplace atmosphere was collected
in a 1% sodium bisulfite solution and analyzed by an ion specific
electrode (ISE) technique (5.1.). This method was considered
inadequate due to the instability of I2 in
bisulfite solution. Two stopgap methods were later developed, in which
any iodine present in the air was collected in 0.01 N sodium hydroxide
solution contained in a midget fritted glass bubbler (MFGB). These
samples were then analyzed by ISE (5.2.) or IC equipped with an
electrochemical detector (ED) (5.3.). Because bubblers are
inconvenient to use as personal samplers due to spillage or breakage,
it was desirable to develop a solid-sorbent sampling method. A method
was developed which collected I2 in the air
using activated charcoal impregnated with an alkali metal hydroxide.
The base-impregnated charcoal converted I2
to iodide (I-) and iodate (IO3-)
which was then desorbed using a weakly basic solution. An aliquot of
the solution was analyzed for I- by IC or ISE.
Unfortunately, background levels of I- (up to 5 µg)
found in the impregnated charcoal were considered unacceptable (5.4.).
Impregnated activated beaded carbon (IABC), previously developed
(5.5., 5.6.) at the OSHA Salt Lake Technical Center (OSHA-SLTC), was
used to replace impregnated charcoal sampling tubes (ICST) used for
the collection of I2. The IABC has a
significantly lower background level of I- (< 0.008
µg). This current method was evaluated using IABC as the
collection medium.
1.2. Principle
Iodine is collected using IABC sorbent contained in a glass tube.
The collected I2 is converted to
I- and IO3- by the treated
sorbent based on the following chemical reaction:
3I2 + 6OH¯---> 3H2O + 5I¯ +
IO3¯
The resultant I- is analyzed by IC-PED. A stoichiometric
conversion factor is used to calculate the amount of
I2 collected. The same mechanism is used for
iodine collection in impingers containing 1.5 mM sodium carbonate and
1.5 mM sodium bicarbonate solutions. These solutions are used for
sampling when the relative humidity >50%.
1.3. Advantages and Disadvantages
1.3.1. This method has adequate sensitivity for determining
compliance with the OSHA Ceiling Permissible Exposure Limit (PEL)
for I2 exposure.
1.3.2. The method is simple, rapid, and easily automated.
1.3.3. The method is specific and can determine the
I2 (as I-) in the presence of
other halogen-containing substances.
1.3.4. The solid sorbent sampling tube used to collect
I2 is small, portable, and contains no
liquid. The tube used to collect only iodine vapor is identical to
that used to collect sulfur dioxide in OSHA Method No. ID-200. A
modified sampling tube is also available for collecting
particulates. The modified tube is similar to the one also
recommended in OSHA Method No. ID-200; however, the foam used in the
modified SO2 sampling device must be
removed before sampling iodine. See Section 2 for further details.
1.3.5. Desorption and preparation of samples for analyses involve
simple procedures and equipment.
1.3.6. The amount of I2 (as
I-) can also be analyzed and confirmed by an ISE
technique. This ISE technique is listed as an Appendix to this
method.
1.3.7. The I- contaminant (background) levels of the
IABC sorbent are extremely low, especially when compared to the
sampling media previously used in OSHA Method No. ID-177.
1.3.8. One major disadvantage of the method is that lower
recoveries are noted when samples are taken at high humidities. A
30% loss in recovery was noted at 80% RH when the
I2 concentration was near 0.5 × PEL (see
Section 4.6.). Due to this humidity problem, the method is
considered an interim method until more suitable sampling media can
be developed or the humidity problem rectified.
1.3.9. Another disadvantage is the skilled maintenance required
for the analytical detector. As specified in Section 3.2.1., the
detector is equipped with two electrodes, a silver working electrode
and a silver/silver chloride reference electrode. The silver working
electrode must be polished before it is installed in the
amperometric cell. It is also necessary to polish the working
electrode whenever a high background current, decreased sensitivity,
or other degradation in detector output is observed. Polishing is a
time-consuming process requiring skill and care. Recently developed
silver/silver chloride reference electrodes require little, if any,
maintenance.
1.4. Method Performance
A synopsis of the method performance is presented below. Further
information can be found in Section 4.
1.4.1. This method was validated over the concentration range of
0.05 to 0.20 ppm. An air volume of 2.5 L and a flow rate of 0.5
L/min were used.
1.4.2. The qualitative detection limit was 0.0027 µg/mL or
0.008 µg (as I-) when using a 3-mL solution
volume. This corresponds to 0.0004 ppm I2
for a 2.5-L air volume.
1.4.3. The quantitative detection limit was 0.009 µg/mL or
0.03 µg (as I-) when using a 3-mL solution volume.
This corresponds to 0.001 ppm I2 for a
2.5-L air volume. A 50-µL sample loop and a
detector setting of 0.1 microampere (µA) full-scale output
were used.
1.4.4. The sensitivity of the analytical method, when using the
instrumental parameters listed in Section 3.6.3., was calculated
from the slope of a linear working range curve (0.1 to 5.0
µg/mL I-). The sensitivity was 2.5 × 106 area
units per 1 µg/mL. A Dionex Series 4500i ion chromatograph
with AI450 computer software was used (Dionex, Sunnyvale, CA).
1.4.5. The performance of this method was significantly better
than OSHA Method No. ID-177 for I2 (5.4.).
1.4.6. The total pooled coefficients of variation
(CVT), bias, and total overall error (OE)
are as follows:
CVT (pooled) = 0.045;
bias =
-0.025;
OET
= ±11.5%
1.4.7. The collection efficiency at 2 × PEL was 100%. Samples
were collected from a generated test atmosphere of 0.20 ppm
I2 for 5 min.
1.4.8. Breakthrough tests were performed at concentrations of
0.75 ppm I2. No breakthrough was found for
a sampling time of 30 min and an average sample flow rate of 0.5
L/min.
1.4.9. Samples can be stored at ambient (20 to 25°C) temperature
on a lab bench for a period of 29 days. Results show the mean sample
recovery after 29 days of storage was within ±10% of results at Day
0; however, a loss over time was noted and samples should be
analyzed as soon as possible. There was no significant
difference in results for samples stored at room temperature, in a
refrigerator, or freezer.
1.5. Interferences
1.5.1. Other gaseous or particulate iodide compounds may
interfere in the analysis of I2 if
collected on the IABC. A modified sampling tube (MST) should be used
to collect any iodide-containing particulate if suspected to be a
problem.
1.5.2. Any substance that has the same retention time as
I-, when using the ion chromatographic operating
conditions described in this method, is an interference. Changing
the chromatographic separation conditions (detector settings,
column, eluent flow rate, and strength, etc.) may circumvent the
interference.
1.6. Uses
Industrial uses and products of iodine (5.7.):
unsaturation indicator |
x-ray contrast media |
dyes |
catalysts |
production of iodides and iodates |
pharmaceuticals |
process engraving and lithography |
iodized salt |
preservatives |
photography |
disinfectants |
food and feed additive |
special lubricants for titanium and
stainless steel parts |
1.7. Physical and Chemical Properties (5.8.)
Iodine exists as dense crystalline grayish-black plates or granules
and has a metallic luster and characteristic odor. Iodine readily
sublimes, producing a violet vapor.
Iodine (CAS No. 7553-56-2)
Chemical formula |
I2 |
Formula weight |
253.8 |
Melting point |
113.5°C |
Boiling point |
184.4°C |
Vapor pressure |
0.0410 kPa (0.309 mmHg) at 25°C |
Vapor density |
4.98 times that of air |
Solubility |
Soluble in alcohol, carbon disulfide,
chloroform, toluene, ether, carbon tetrachloride, glycerol,
and alkaline iodide solutions. Slightly soluble in
water. |
Combustibility |
Noncombustible |
1.8. Toxicology
Information listed within this section is a synopsis of current
knowledge of the physiological effects of I2
and is not intended to be used as a basis for OSHA policy.
1.8.1. Iodine is considered a greater physiological irritant and
more corrosive than bromine or chlorine (5.9.). Occupational routes
of exposure for I2 are inhalation, skin
contact, and eye contact.
1.8.2. Symptoms of I2 exposure (5.10.,
5.11., 5.12.)
Inhalation: |
Nasal passage irritation, headache, tightness
in chest, chronic pharyngitis, rhinitis, possible pulmonary
edema. |
|
Skin: |
Rash, cutaneous hypersensitivity, skin
burns. |
|
Eyes: |
Burning, stinging sensations, blepharitis,
lacrimation. |
1.8.3. Excretion:
Iodine absorbed by the lungs is physiologically converted to
iodide and eliminated primarily in the urine.
2. Sampling (See Interferences, Section 1.5., and Notes in
Section 2.1.2. before sampling.)
Wipe samples are normally not taken for iodine. If wipe sampling is
necessary, the ability to perform this will have to be conducted on a
case-by-case basis. Contact the OSHA-SLTC for further sampling
information.
2.1. Equipment - Air Samples
2.1.1. Calibrated personal sampling pumps capable of sampling
within ±5% of the recommended flow rate of 0.5 L/min are used.
2.1.2. Solid sorbent sampling tubes are prepared using glass
tubes, glass wool plugs, and IABC. Commercially available sampling
tubes consist of glass tubes packed with 100-mg IABC
front and 50-mg backup sections (Cat. No. 226-80, SKC Inc., Eighty
Four, PA). The IABC is held in place with glass wool and a stainless
steel retainer clip.
Notes: a) IODIDE PARTICULATE: If there is reason to
suspect the sampled air could contain iodide particulate, a
modified sampling tube (MST) should be used to exclude the
particulate. See Section 2.1.6. for more details. Most
industrial operations that use iodine in their processes do not
normally also use iodide salts.
b) RELATIVE HUMIDITY: If the relative humidity is
>50%, impinger samplers should be used. A 20% loss of
iodine at 80% RH (25°C) and 1 × PEL has been noted when using SKC
Cat. no. 226-80 tubes. It is unknown what loss of iodine occurs
above 80% RH. Please note the following equipment is used:
1) Midget impingers, (order no. 7531, Ace Glass Co.,
Vineland, NJ).
2) Sample shipment vials: Scintillation vials, 20-mL (part
no. 74515 or 58515, Kimble, Div. of Owens-Illinois Inc., Toledo,
OH) with polypropylene or Teflon® cap
liners.
3) Collection solution: 1.5 mM Na2
CO3 + 1.5 mM
NaHCO3 Dissolve 0.159 g sodium
carbonate (Na2
CO3) and 0.126 g sodium bicarbonate
(NaHCO3) in 1-L deionized water. Use
at least reagent grade chemicals.
2.1.3. A stopwatch and bubble tube or meter are used to calibrate
pumps.
2.1.4. A battery-operated or sling psychrometer, or a water vapor
detector tube is used to measure the relative humidity prior to
sampling.
2.1.5. Various lengths of polyvinyl chloride (PVC) tubing are
used to connect sampling media to pumps.
2.1.6. Sampling in presence of iodide-containing
particulates. Filter media normally used for collecting or
precluding particulate (i.e. polyvinyl chloride, mixed-cellulose
ester, etc.) should not be used as prefilters due to the
possibility of reaction with iodine. If the workplace air being
sampled is suspected of containing particulate which could interfere
(i.e. iodides), a MST device containing a
Teflon® filter as shown below should be
used to exclude particulate. (Note: If impingers are used, the IABC
and glass wool are removed from the rear of the MST and only the
glass jacket/ Teflon® filter and retaining
rings are connected in front of the impinger.) The sampled air
should always travel in the direction shown below:
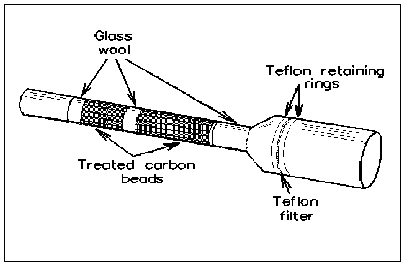
< --- < ---- < Sample Flow < --- <
----
Type II - Modified Sampling Tube (MST)
Note: This MST (Forrest Biomedical, Salt Lake City, UT) is the
same sampling device (Type II) discussed in OSHA Method ID-200
(5.6.) for sulfur dioxide with one exception: The foam normally used
as spacers in the tube are replaced with glass wool. Foam can absorb
the iodine.
2.2. Equipment - Bulk Samples
Scintillation vials, 20-mL (part no. 74515 or 58515, Kimble, Div.
of Owens-Illinois Inc., Toledo, OH) with polypropylene or
Teflon® cap liners. If possible, submit bulk
samples in these vials. Tin or other metal cap liners should not be
used because the metal and iodine may react.
2.3. Sampling Procedure - Air Samples
The following flow chart is an overview of the sampling protocol
for iodine.
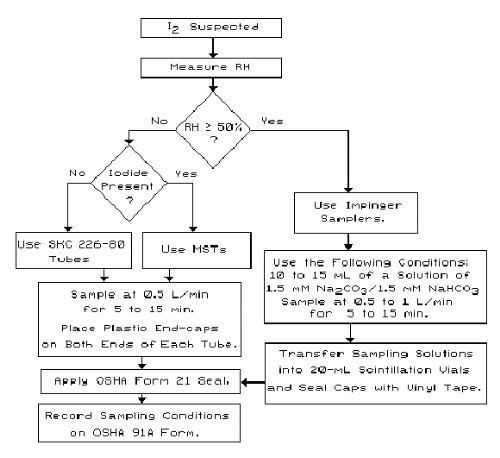 Overview of I2 Sampling
Procedures |
2.3.1. Determine the humidity at the sampling site using a
psychrometer, detector tube, or other suitable device. Loss of
iodine has been noted at high humidities. This loss is
concentration-dependent, and at iodine levels near the PEL the loss
in recovery is approximately 20%. An alternate method employing
impinger solutions should be used when sampling in high humidities
(>50% RH) as described above. See Section 4.6. for further
details regarding the humidity- and concentration-dependent loss of
iodine.
2.3.2. Connect the sampling tube (or impinger) to the calibrated
pump. If sampling tubes are used, make sure sampled air enters the
large section (100 mg) of IABC first. Place the sampling device on
the employee such that air is sampled from the breathing zone.
2.3.3. Use a flow rate of 0.5 L/min and a sampling time between 5
to 15 min. Take additional samples as necessary.
2.3.4. After sampling, place plastic end caps tightly on both
ends of the tube and apply OSHA Form 21 seals in such a way as to
secure the end caps. If impingers were used, transfer solutions to
20-mL scintillation vials and apply seals. Record the sampling
conditions such as sampling time, air volume, etc. on the OSHA 91A
form. When other compounds are known or suspected to be present in
the air, record such information and transmit with the samples.
2.3.5. Use the same lot of IABC tubes for blank and collected
samples. Handle the blank sorbent tube (or solution if impingers are
used) in exactly the same manner as the sample tubes except that no
air is drawn through it. Submit at least one blank tube for each
batch of ten samples.
2.4. Sampling Procedure -Bulk Samples
Bulk samples can be taken to assist in resolving any potential
interferences or to confirm the presence of free iodine in the
workplace.
2.4.1. Take a representative sample of the bulk material in the
workplace. Transfer the bulk material into a 20-mL scintillation
vial and seal the cap with vinyl or electrical tape. Securely wrap
an OSHA-21 seal length-wise from vial top to bottom.
2.4.2. The type of bulk sample should be stated on the OSHA 91A
and cross-referenced to the appropriate air sample(s).
2.5. Shipment
2.5.1. Immediately send the samples to the laboratory with the
OSHA 91A paperwork requesting iodine analysis.
2.5.2. Ship any bulk samples separately from air samples. Enclose
Material Safety Data Sheets if available. Check current shipping
restrictions and ship to the laboratory by the appropriate method.
3. Analysis
Note: If the instrumentation in Section 3.2.1. is unavailable,
samples can be prepared and analyzed using an ion specific electrode
(ISE) technique. Directions are given in the Appendix of this method.
Due to the greater specificity of an IC-PED, this ISE procedure is
only recommended if an IC-PED system is unavailable.
3.1. Safety Precautions
3.1.1. Refer to appropriate IC instrument manuals, PED
maintenance manual (especially for electrode maintenance), and any
Standard Operating Procedures (SOP) for proper instrument operation
(5.13.).
3.1.2. Observe laboratory safety regulations and practices.
3.1.3. Some chemicals are corrosive. Use appropriate personal
protective equipment such as safety glasses, goggles, face shields,
gloves, and lab coat when handling corrosive chemicals.
3.2. Equipment
3.2.1. Ion chromatograph (Model 4000i or 4500i Dionex,
Sunnyvale, CA) equipped with a pulsed electrochemical detector (PED)
containing a silver working electrode and silver/silver chloride
reference electrode.
[Note: A combination PED/conductivity detector (Dionex, part no.
42039) was used to validate this method. The conductivity detector
is not used for this method; however, having both detectors present
in one package is advantageous because of increased applications.]
3.2.2. Automatic sampler (Dionex Model AS-1) and sample vials
(0.5 mL).
3.2.3. Laboratory automation system: Ion chromatograph interfaced
with a data reduction system (AI450, Dionex).
3.2.4. Separator and guard columns, anion (Model HPIC-AS5 and
AG5, Dionex).
3.2.5. Disposable syringes (1 mL).
3.2.6. Syringe prefilters, 0.5-µm pore size (part no. SLSR
025 NS, Millipore Corp., Bedford, MA).
Note: Some syringe prefilters are not cation- or anion-free.
Tests should be performed with blank solutions first to determine
contamination and suitability with the analyte.
3.2.7. Miscellaneous volumetric glassware: Micropipettes,
pipettes, volumetric flasks, Erlenmeyer flasks, graduated cylinders,
and beakers.
3.2.8. Scintillation vials, glass, 20-mL.
3.2.9. Equipment for eluent degassing (vacuum pump, ultrasonic
bath).
3.2.10. Analytical balance (0.01 mg).
3.3. Reagents - All chemicals should be at least reagent grade.
3.3.1. Principal reagents:
Sodium carbonate
(Na2CO3) Sodium
bicarbonate (NaHCO3) Sodium
nitrate (NaNO3) Potassium iodide
(KI) Potassium iodate
(KIO3) Deionized water (DI
H2O) |
3.3.2. Desorbing solution (1.5 mM
Na2CO3 + 1.5 mM
NaHCO3):
Dissolve 0.318 g
Na2CO3 and 0.252
g NaHCO3 in 2.0 L DI
H2O.
3.3.3. Eluent (0.02 M NaNO3):
Dissolve 3.40 g NaNO3 in 2.0 L DI
H2O. Sonicate this solution and degas
under vacuum for 15 min before use.
3.3.4. Iodide (I-) stock standard (100 µg/mL):
Dissolve and dilute 0.1308 g of KI to 1.0 L with DI
H2O. Prepare monthly.
3.3.5. Iodide (I-) standard solutions, 10, 1, and 0.1
µg/mL:
Pipette appropriate volumes of the 100 µg/mL I-
stock standard into volumetric flasks and dilute to the mark with
desorbing solution. Prepare monthly.
3.3.6. Iodate (IO3-) stock standard
(100 µg/mL):
Dissolve and dilute 0.1224 g of KIO3 to
1.0 L with DI H2O. Prepare monthly (Note:
This standard is only used if confirmation of iodine is necessary in
addition to the iodide analysis. Dilute to concentrations in Section
4.12. with desorbing solution. See Sections 4.11. and 4.12. for more
details.).
3.4. Working Standard Preparation - Prepare monthly.
Prepare I- working standards in desorbing solution. A
suggested scheme for preparing a series of working standards using
10-mL final solution volumes is shown below:
Working Std |
Std Solution |
Aliquot |
Eluent Added |
(µg/mL) |
(µg/mL) |
(mL) |
(mL) |
|
0.1 |
0.1 |
* |
* |
0.2 |
1.0 |
2.0 |
8.0 |
0.5 |
1.0 |
5.0 |
5.0 |
1.0 |
1.0 |
* |
* |
2.0 |
10.0 |
2.0 |
8.0 |
5.0 |
10.0 |
5.0 |
5.0 |
|
*
Already prepared in Section 3.3.5. |
3.5. Sample Preparation
IABC samples: Follow Sections 3.5.1. to 3.5.3. below.
Impinger samples: Follow Section 3.5.4. only.
Note: If the MST device discussed in Section 2.1.6. is used, the
prefilter is not analyzed for iodine.
3.5.1. Carefully remove and discard the rear glass wool plug
from each glass tube without losing any IABC sorbent.
Note: The sorbent should always be removed from the glass tube
via the opposite end of collection (i.e. 50-mg IABC backup section
is removed first). This will minimize the possibility of
contamination from any collected particulate.
3.5.2. Carefully transfer each IABC section from a sample tube
into a separate 25-mL Erlenmeyer flask or 20-mL scintillation vial.
3.5.3. Pipette 3.0 mL of desorbing solution into each flask.
Note: Alternate sample volumes can be used and are dependent on
the analytical sensitivity desired. For most industrial hygiene
samples, 3-mL volumes will allow for detection of iodine within the
range of standards specified. Cap each flask or vial tightly and
allow each solution to sit for at least 60 min. Occasionally swirl
each solution.
3.5.4. Impinger samples: Measure and record the solution volume
of each sample using individual graduated cylinders.
3.6. Analysis
3.6.1. Pipette or pour a 0.5- to 0.6-mL portion of each standard
or sample solution into separate automatic sampler vials. Place a
filtercap into each vial. The large filter portion of the cap should
face the solution.
3.6.2. Load the automatic sampler with labeled samples,
standards, and blanks.
3.6.3. Set up the ion chromatograph in accordance with the SOP
(5.13.).
Note: An SOP is a written procedure for a specific instrument. It
is suggested that SOPs be prepared for each type of instrument used
in a lab to enhance safe and effective operation.
Typical operating conditions for a Dionex 4000i or 4500i with a
PED and an automated sampler are listed below:
Ion Chromatograph |
|
|
Eluent: |
0.02 M NaNO3 |
Column temperature: |
ambient |
Anion precolumn: |
AG5 |
Anion separator column: |
AS5 |
Amperometry Output range: |
0.1 µA |
Sample injection loop: |
50 µL |
|
Pump |
|
|
Pump pressure: |
900
psi |
Flow rate: |
2 mL/min |
|
Chromatogram |
|
|
Run time: |
5 min |
Peak retention time: |
3.00 min for
I- |
3.6.4. Follow the SOP for further instructions regarding analysis
(5.13.).
3.7. Calculations
3.7.1. After the analysis is completed, retrieve the peak areas
or heights. Obtain hard copies of chromatograms from a printer. An
example chromatogram of a solid sorbent sample collected at an
iodine concentration of approximately 2 × PEL for 5 min is shown
below:
3.7.2. Prepare a concentration-response curve by plotting the
peak areas or peak heights versus the concentration of the
I- standards in µg/mL.
3.7.3. Perform a blank correction for each IABC front and backup
section. Subtract the µg/mL I- blank value (if
any) from each sample reading if blank and sample solution volumes
are the same. If a different solution volume is used, subtract the
total µg blank value from each total µg sample value.
3.7.4. Calculate the air concentration of
I2 (in ppm) for each air sample:
A = (µg/mL I-) × (Sol Vol) × (GF)
ppm I2 = |
(A) × (mol vol)
(AV) × (mol wt) |
Where:
A |
= µg I2 |
µg/mL I- |
= Amount found (from calibration curve) |
Sol Vol |
= Solution volume (mL) from Section 3.5.3. (or
3.5.4.) |
GF |
= Gravimetric factor =
3I2/5I- = 6/5 = 1.2 |
Mol Vol |
= Molar volume (L/mol) = 24.45 (25°C and 760
mmHg) |
AV |
= Air volume (L) |
Mol Wt |
= Molecular weight for
I2 = 253.8
(g/mol) |
3.8. Reporting Results
Add the backup section ppm I2 result (if
any) to the front section result for each IABC sample. Report results
to the industrial hygienist as ppm I2.
4. Backup Data
This method has been validated for a 2.5-L, 5-min sample taken at a
flow rate of 0.5 L/min. The method validation was conducted near the
OSHA Ceiling PEL of 0.1 ppm I2. The sampling
media used during the validation consisted of two-section tubes packed
with 100-mg of IABC for the front and 50 mg for the backup sections.
Tubes were obtained commercially from SKC (Lot no. 810, Cat. no. 226-80,
SKC Inc., Eighty Four, PA).
The validation consisted of the following experiments and discussion:
1. An analysis of 20 spiked samples was performed (7 samples each
at 2 × and 1 ×, and 6 samples at 0.5 × the Ceiling PEL) to evaluate
desorption efficiency (DE).
2. A sampling and analysis of 18 samples (6 samples each at 2 ×, 1
×, and 0.5 × Ceiling PEL) collected from dynamically generated test
atmospheres at 50% RH to determine bias and overall error.
3. A determination of the sampling media collection efficiency at
approximately 2 × Ceiling PEL).
4. A determination of potential breakthrough.
5. An evaluation of storage stability at room (20 to 25°C),
refrigerator (0 to 4°C), and freezer (-10 to -14°C)
temperatures for 80 collected samples.
6. A determination of any significant effects on results when
sampling at different humidities.
7. A determination of the qualitative and quantitative detection
limits for I-.
8. Comparison of sampling methods: IABC versus Impinger.
9. Evaluation of a prefilter/cassette assembly and a modified
sampling tube for use during sampling.
10. Evaluation of the previous OSHA sampling device, an impregnated
charcoal sampling tube (SKC, Lot 411, Cat. No. 226-67).
11. Confirmation of iodine using the disproportionation product
iodate (IO3-).
12. A determination of the qualitative and quantitative detection
limits for IO3-.
13. Summary.
A generation system was assembled, as shown in Figure 1, and used for
all experiments except the analysis and detection limit determinations.
All samples were analyzed by IC-PED. All known concentrations of
generated test atmospheres were calculated from the
I2 diffusion rate.
All results were calculated from concentration-response curves and
statistically examined for outliers. In addition, the analysis (Section
4.1.) and sampling and analysis results (Section 4.2.) were tested for
homogeneity of variance. Possible outliers were determined using the
Treatment of Outliers Test (5.14.). Homogeneity of variance was
determined using Bartlett's test (5.15.). Statistical evaluation was
conducted according to the Inorganic Methods Evaluation Protocol
(5.16.). The overall error (OE) (5.16.) was calculated using the
equation:
OEi% = ±(|biasi| +
2CVi) × 100% (at the 95% confidence level)
Where i is the respective sample pool being examined.
Block Diagram of the Laboratory Generation
System
Figure 1
4.1. Spiked Sample Analysis
Twenty samples were prepared by adding known amounts of
I- (as KI) stock solution to the IABC tubes to determine
desorption efficiencies (DEs) for the analytical portion of the
method.
4.1.1. Procedure: Sampling tubes containing IABC were
spiked using a 25-µL syringe (Hamilton
Microliter®/Gastight®
Syringe, Hamilton Co., Reno, NV). Spikes were 2.25, 4.50, and 9.00
µg I-. These levels correspond approximately to
0.5, 1, and 2 × the Ceiling PEL for a 5-L air sample collected at a
0.5-L/min flow rate. [Note: 5 L (10-min sample) was used as an
intermittent point between a 5 to 15-min sample. The spiked sample
analysis test is conducted first to determine analytical merits of
the method. It was unknown whether this method could collect iodine
as a 5-min sample when this test was conducted and 10-min was chosen
from past experience.]
4.1.2. Results: Desorption efficiencies are presented in
Table 1. As shown, the average DE is very close to 1.0. No DE
corrections are necessary for I2
collection using IABC tubes.
Table 1 Iodine (as I-) Analysis - Desorption
Efficiency (DE)
Level |
N |
Mean DE |
SD |
CV1 |
0.5 × PEL |
6 |
1.048 |
0.072 |
0.069 |
1 × PEL |
7 |
0.997 |
0.017 |
0.017 |
2 × PEL |
7 |
1.001 |
0.023 |
0.023 |
All Levels |
20 |
1.015 |
0.042 |
0.041* |
* = CV1 (pooled)
4.2. Sampling and Analysis
To determine the precision and accuracy of the method, known
concentrations of I2 were generated, samples
were collected and then analyzed.
4.2.1. Procedure:
1) Test atmospheres of I2 were
generated using a permeation/diffusion chamber (Model 450
Dynacalibrator, Metronics, Santa Clara, CA) and a dynamic
generation system. To generate I2 vapor,
I2 resublimed crystal was placed in a
diffusion tube, and heated to 70 ± 0.1°C. The
I2 vapor was diluted with filtered,
humidified air using the system shown in Figure 1 and as discussed
below.
2) Dynamic generation system A Miller-Nelson Research Inc.
flow, temperature, and humidity control system (Model HCS-301,
Monterey, CA) was used to control and condition the dilution
airstream. All generation system fittings and connections were
Teflon®. The
I2 concentrations were varied by
adjusting the dilution airstream volume. The dilution airstream
was adjusted using the mass flow controller of the
Miller-Nelson system. For this experiment, the system
was set to generate test atmospheres at 50% RH and 25°C.
3) The total flow rate of the generation system was measured
using a dry test meter.
4) Solid-sorbent samples were taken from the sampling manifold
using constant-flow pumps.
Gilian® Gil-Air SC pumps (Gilian
Instrument Corp., W. Caldwell, NJ) were used. Pump flow rates were
approximately 0.5 L/min and sampling time was 5 min. Generation
system concentrations were approximately 0.5, 1, and 2 times the
OSHA Ceiling PEL.
4.2.2. Results: The results are shown in Table 2. The
spiked sample (Table 1) and test atmosphere sample (Table 2) results
each passed the Bartlett's test and were pooled to determine a
CVT for the sampling and analytical
method.
Table 2 Iodine Sampling and Analysis - Ceiling PEL
Determination
Level |
N |
Mean |
SD |
CV2 |
OE (±%) |
0.5 × PEL |
6 |
0.987 |
0.045 |
0.046 |
10.5 |
1 × PEL |
6 |
0.942 |
0.033 |
0.035 |
12.8 |
2 × PEL |
6 |
0.997 |
0.043 |
0.043 |
8.90 |
All Levels |
18 |
0.975 |
- |
0.042* |
10.9** |
* = CV2 (pooled) ** =
OE2
The total pooled coefficients of variation
(CVT), bias, and total overall error (OET)
are as follows:
CVT (pooled) = 0.045;
bias = -0.025;
OET
= ±11.5%
(Note: "T" values include data from
Section 4.1. and are calculated using equations specified in
references 5.15. and 5.16.)
4.3. Collection Efficiency
Procedure: Six commercially-prepared sampling tubes were
used for collection at a concentration of approximately 2 × the OSHA
Ceiling PEL for 5 min at 0.5 L/min (50% RH and 25°C). The amounts of
I2 vapor collected in the first section (100
mg of sorbent) and second section (50 mg) were determined. The
collection efficiency (CE) was calculated by dividing the amount of
I2 collected in the first section by the
total amount of I2 collected in the first
and second sections.
Results: The results in Table 3 show a CE of 100%. No
I2 was found in the second sorbent section
for the CE experiment and indicates the sorbent can adequately collect
iodine near the PEL.
Table 3 Collection Efficiency (2 × PEL, 25°C & 50%
RH)
|
|
-----------ppm
I2----------- |
|
Sample No. |
First Section |
Second Section |
% Collection Efficiency |
|
1 |
0.201 |
ND |
100.0 |
2 |
0.185 |
ND |
100.0 |
3 |
0.194 |
ND |
100.0 |
4 |
0.210 |
ND |
100.0 |
5 |
0.192 |
ND |
100.0 |
6 |
0.196 |
ND |
100.0 |
|
Notes: |
(a) Sampled at approximately 0.5
L/min for 5 min. |
|
(b) Samples desorbed using a
sample solution volume of 3.0 mL |
|
(c) ND = None detectable
(<0.0004 ppm
I2) | |
4.4. Breakthrough
(Note: Breakthrough is defined as >5% loss of analyte through
the sampling media at 50% RH)
Procedure: The same procedure as the CE experiment (Section
4.3.) was used with two exceptions: The generation concentration was
increased to a level approximately 7 × the Ceiling PEL, and samples
were taken at approximately 0.5 L/min for 30 min.
The amount of breakthrough for each sampling tube was calculated by
dividing the amount collected in the second section by the total
amount of I2 collected in the first and
second sections.
Results: No breakthrough of I2
into the second section was found, and indicates the sorbent has
adequate retention of iodine at concentrations higher than expected in
industrial workplaces. Results are shown in Table 4.
Table 4 Breakthrough Study (25°C and 50% RH)
|
|
--------ppm
I2 Found---------- |
|
Sample No. |
1st Section |
2nd Section |
% Breakthrough |
|
1 |
0.766 |
ND |
0 |
2 |
0.762 |
ND |
0 |
3 |
0.775 |
ND |
0 |
4 |
0.765 |
ND |
0 |
5 |
0.735 |
ND |
0 |
6 |
0.747 |
ND |
0 |
|
Notes: |
(a) |
Sampled at approximately 0.5
L/min for 30 min |
|
(b) |
Due to the large concentration
generated and the analytical sensitivity, the front IABC
sections of sampling tubes were desorbed using larger
sample solution volumes of 20.0 mL. The 2nd sections were
desorbed using the recommended volume of 3 mL. |
|
(c) |
ND = None detectable (<0.0004
ppm
I2) | |
4.5. Storage Stability
Procedure: Two tests were conducted to assess storage
stability. The first was a preliminary study of room temperature
storage (20 to 25°C) after I2 collection.
Twenty-four samples were taken near the OSHA Ceiling PEL of 0.1 ppm.
After collection, all samples were stored under normal laboratory
conditions (20 to 25°C) on a lab bench and were not protected from
light. Six samples were initially desorbed and analyzed, then six
samples were desorbed and analyzed after various periods of storage
(5, 15, and 30 days).
In order to assess if sample storage is temperature-dependent for
iodine samples, an additional test was conducted to determine if
refrigeration could improve recoveries. This test was conducted by
generating 56 samples, including 6 control samples (used for day 0).
The samples were separated into 3 groups, consisting of 5 or 6 samples
per storage period. A group was stored at either room (20 to 25°C),
refrigerator (0 to 4°C), or freezer (-10 to -14°C) temperatures. The
same analytical procedure as the previous storage test was used.
Samples were analyzed after 0, 5, 15, and 29 days.
Results: As shown in Table 5a, the results of the
preliminary test conducted at room temperature show the mean of
samples analyzed after 30 days displayed a 12% loss when compared to
the value of day 0.
Table 5a - Preliminary Test Storage Stability - Iodine (1 ×
PEL, 25°C, and 50% RH)
Day |
N |
Mean |
SD |
CV |
Recovery (%) |
0 |
5 |
0.114 |
0.005 |
0.045 |
99.1 |
5 |
6 |
0.109 |
0.004 |
0.037 |
94.8 |
15 |
6 |
0.096 |
0.007 |
0.073 |
83.5 |
30 |
6 |
0.100 |
0.003 |
0.027 |
87.0 |
Table 5b shows the results of the second study at different
temperatures. The recovery shows 9.5% less of the value of day 0 after
a 29-day storage at room temperature, and losses of 15.5% and 14.7% at
refrigerator and freezer temperatures, respectively. Therefore, an
improvement in recoveries was not noted when samples are stored at
reduced temperatures. A significant reduction in recovery over 30 days
was not noted using the previous charcoal treated sampling media in
OSHA Method No. ID-177 (5.4.) or in the bicarbonate/carbonate
solutions used as impinger collection or as analytical standards. The
carbon bead used for this collection procedure appears to be
responsible for the loss and further work will have to be performed to
determine the extent and mechanism.
Table 5b - Storage Stability Room, Refrigerator, and
Freezer Temperatures (Known I2
Concentration = 0.116 ppm at 50% RH)
Day |
Temperature |
N |
Mean |
SD |
CV |
Recovery (%) |
0 |
Room |
6 |
0.114 |
0.003 |
0.025 |
98.3 |
5 |
Room |
5 |
0.109 |
0.009 |
0.081 |
94.0 |
Refrigerator |
5 |
0.109 |
0.008 |
0.075 |
94.0 |
Freezer |
5 |
0.108 |
0.007 |
0.063 |
93.1 |
15 |
Room |
6 |
0.101 |
0.008 |
0.074 |
87.1 |
Refrigerator |
5 |
0.102 |
0.004 |
0.042 |
87.9 |
Freezer |
5 |
0.101 |
0.003 |
0.034 |
87.1 |
29 |
Room |
6 |
0.103 |
0.004 |
0.035 |
88.8 |
Refrigerator |
6 |
0.096 |
0.004 |
0.047 |
82.8 |
Freezer |
6 |
0.097 |
0.008 |
0.086 |
83.6 |
Figure 2 shows results from both studies and linear curve fits of
the recovery data over time. The loss over time shows that samples
should be analyzed as soon as possible, preferably within 1 or 2 weeks
after sampling.
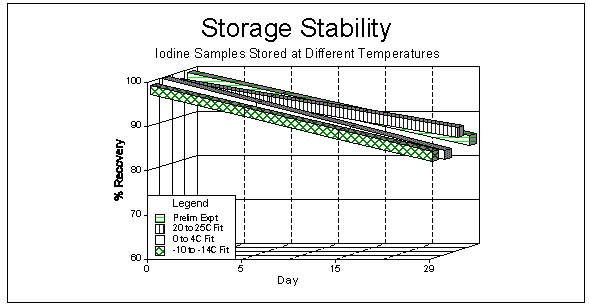
Figure 2
4.6. Humidity Study
Procedure: A study was conducted to determine any effect on
results when samples are collected at different humidities. Samples
were taken using the generation system and procedure described in
Section 4.2. Test atmospheres were generated at 25°C and at
approximately 0.5, 1, and 2 × the OSHA Ceiling PEL. Relative
humidities of 25%, 50%, and 80% were used at each concentration level
tested. All tests were conducted by taking IABC samples side-by-side
with impinger samples containing an aqueous collecting solution
mixture of 1.5 mM
Na2CO3 and 1.5 mM
NaHCO3. Impingers were used at first instead
of bubblers to minimize any back pressure which could result from
sampling rates of approximately 1 L/min and dual sampling trains. Two
impingers in series were thought to be necessary for iodine
collection; however, after a few experiments it was determined iodine
collection efficiency using one impinger was adequate.
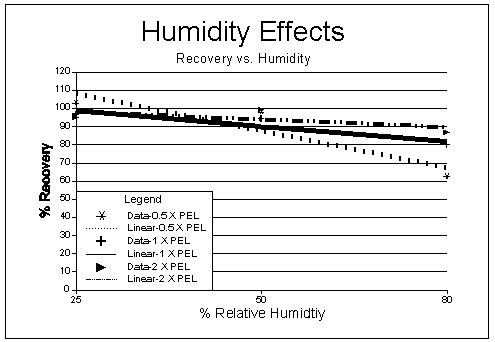 Figure
3
Results: Results of the humidity tests are listed in Table 6
(results of impinger samples taken at 80% RH are also shown for
comparison) and shown in Figures 3 through 5. An F test was used to
determine if any significant effect occurred when sampling at
different RHs. As shown, at the 99% confidence level, the calculated F
values are larger than critical F values (5.16.) for all the
concentrations tested, and a significant difference in results
occurred across the RH ranges tested. Figures 3 and 5 show a
dependence on RH occurs and samples collected at higher RHs tend to
display lower recoveries.
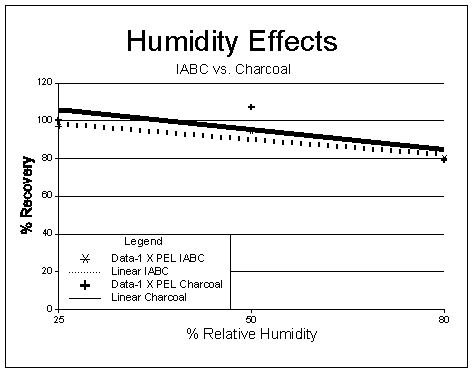 Figure
4
The loss over humidity levels appears to follow a linear trend as
shown in Figures 3 and 4. Figure 4 shows an almost identical loss
occurs when using the treated charcoal sampler listed in OSHA Method
No. ID-177 (5.4). A dependence on concentration is also readily
apparent when examining the recoveries for Figure 5. This loss versus
concentration appears to follow a logarithmic function (concentrations
above 2 × PEL are extrapolated). Loss of iodine is more readily
evident at low concentration and high RHs than higher concentrations
and high RHs. The lower recoveries were not readily evident at low
concentrations when samples were collected in impingers containing
weakly basic solutions. Tests were not conducted above 80% RH due to
difficulties associated with generating higher humidity levels in the
laboratory. It is unknown what losses will occur at RH levels above
80%. If low concentration and high humidity situations are anticipated
(>50% RH) prior to sampling, sample collection using
impingers will give increased recoveries; however, the inconvenience
of collection using these devices is a serious disadvantage.
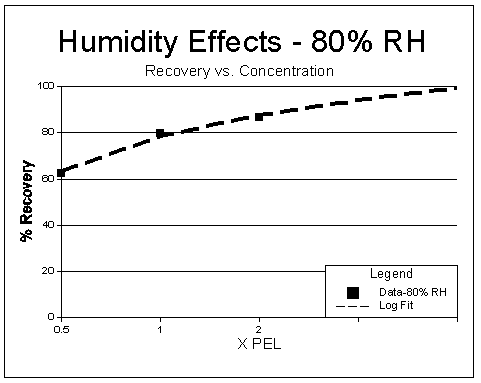 Figure
5
Although impingers were used for this test, bubblers will most
likely give better results than impingers due to increased dispersion
of the sample into the bubbler solution. The increased collection
efficiency of bubblers over impingers for the same substance and
collection solution has been demonstrated in previous studies of
formaldehyde (5.18.). As previously discussed in Section 1, two
stopgap methods were developed using bubblers containing basic
collection solutions. Adequate recoveries were noted using this
approach. Further testing of bubblers may be necessary to demonstrate
improved collection of iodine over impingers.
Table 6 Humidity Test - Iodine - 25°C
Level |
% RH |
N |
Mean |
SD |
CV |
Taken |
Recovery (%) |
Fcrit |
Fcalc |
0.5 × PEL |
25 |
6 |
0.063 |
0.008 |
0.134 |
0.061 |
103 |
6.36 |
33.5 |
50 |
6 |
0.049 |
0.002 |
0.046 |
0.050 |
98.0 |
80 |
6 |
0.037 |
0.005 |
0.129 |
0.059 |
62.7 |
80* |
3 |
0.058 |
0.005 |
0.086 |
0.061 |
95.1 |
|
|
1 × PEL |
25 |
6 |
0.116 |
0.006 |
0.050 |
0.120 |
96.7 |
6.52 |
10.5 |
50 |
5 |
0.113 |
0.004 |
0.039 |
0.120 |
94.2 |
80 |
6 |
0.092 |
0.014 |
0.152 |
0.115 |
80.0 |
80* |
3 |
0.109 |
0.002 |
0.018 |
0.115 |
94.8 |
|
|
2 × PEL |
25 |
6 |
0.210 |
0.014 |
0.068 |
0.221 |
95.0 |
6.36 |
14.0 |
50 |
6 |
0.196 |
0.009 |
0.043 |
0.197 |
99.4 |
80 |
6 |
0.184 |
0.008 |
0.042 |
0.212 |
86.8 |
80* |
3 |
0.183 |
0.004 |
0.022 |
0.212 |
86.3 |
|
|
*Samples were taken with impingers containing collecting solution
(1.5 mM
Na2CO3/NaHCO3),
which was same as desorbing solution used in preparing working
standards (see Section 3.4.).
4.7. Qualitative and Quantitative Detection Limit Study
A modification of the National Institute for Occupational Safety
and Health (NIOSH) detection limit calculations (5.19., 5.20.) was
used to calculate detection limits.
Note: For this experiment, a comparison of samples with and without
the sampling media present was used to determine limits, and a
separate recovery study was not conducted as mentioned in the NIOSH
protocol. The recovery study was not conducted so as not to confound
the difficulty of generating very low concentration samples with the
comparison of spiked samples with and without the sampling media.
Procedure: Two sets of low concentration samples were
prepared by spiking desorbing solutions (Section 3.3.2.) with aliquots
of aqueous standards prepared from KI (Section 3.3.4.) at five
different concentrations. One set of samples was spiked at five
different levels without the IABC sorbent present while the other set
included IABC in each solution prior to spiking. Both sets of samples
were analyzed using a 50-µL sample injection loop and a PED
setting of 0.1 µA.
Results: The IABC spiked sample results are shown in Table 7
for qualitative and quantitative detection limits, respectively. Both
sets of samples gave virtually identical detection limits, indicating
in this case, sampling media did not have a significant effect on the
detection limit. The qualitative detection limit is 0.003 µg/mL
as I- at the 99.8% confidence level. The quantitative
detection limit is 0.009 µg/mL as I-. Using a 2.5-L
air volume and a 3-mL sample solution volume, the qualitative and
quantitative detection limits are 0.0004 ppm and 0.001 ppm,
respectively as I2.
Table 7 Qualitative and Quantitative Detection
Limits
|
|
--------------------I2 (as
µg/mL, I-) Level------------------- |
|
0.002 |
0.005 |
0.010 |
0.020 |
Sample No. |
PA |
PA |
PA |
PA |
|
1 |
3,244 |
5,918 |
18,190 |
36,081 |
2 |
3,501 |
9,682 |
18,624 |
37,305 |
3 |
2,598 |
6,929 |
20,428 |
35,622 |
4 |
3,002 |
10,842 |
20,398 |
38,262 |
|
PA = Integrated
Peak Area (as
I-) The blank
and 0.001 µg/mL integrated peak areas were all equal to
zero. |
|
The response of the low-level calibration samples were plotted
to obtain the linear regression equation (Y = mX + b), and the
predicted responses ( i) at
each X.
Using the equations: |
Sy |
= |
[S( i -
Yi)2/(N -
2)]½ |
|
Q1 |
= |
(3Sy + B - b)/m |
|
Q2 |
= |
3.33 Q1 |
Where:
B |
= |
the mean blank response |
b |
= |
intercept of the regression |
m |
= |
analytical sensitivity or slope as calculated
by linear regression |
Sy |
= |
the standard error of the regression |
N |
= |
the number of data points |
Q1 |
= |
qualitative detection limit |
Q2 |
= |
quantitative detection
limit |
B = 0; b = -546.3833; m = 1,887,623;
Sy = 1,496; N = 16 and Y = b + mX =
-546.3833 + 1,887,623X
Therefore, |
|
Q1 = (3Sy + B - b)/m
= 2.667 × 10-3 µg/mL as
I- |
|
 |
8.00 × 10-3 µg
as I- (3-mL sample volume). |
|
 |
3.70 × 10-4 ppm
I2 (2.5-L air
volume). |
Q2 = 3.33 Q1 = 1.23 × 10-3 ppm
I2 (2.5-L air volume).
Using the International Union of Pure and Applied Chemistry (IUPAC)
approach as discussed in prior methods (5.20.) gave a detection limit
(Q2) of 5.5 × 10-4 ppm
I2 when using the data presented above.
4.8. Comparison of Sampling Methods
Procedure: In order to compare the performance of this
method, the IABC and impinger samples were collected side-by-side from
the generation system at approximately 1 × PEL. The impinger
collection solution is specified in Section 4.6. All samples were
analyzed by IC-PED.
Results: Table 8 shows the results of comparison study. As
shown, the IABC and impinger results are in good agreement.
Table 8 Comparison Study - IABC vs Impinger (Known
Concentration = 0.115 ppm I2) (25°C, and
50% RH)
|
N |
Mean |
SD |
CV |
Recovery, % |
IABC |
6 |
0.113 |
0.004 |
0.035 |
98.3 |
Impinger |
6 |
0.111 |
0.002 |
0.019 |
96.5 |
Notes: |
(a) |
Sampling Time = 5 min |
|
(b) |
Flow Rate = 0.525 L/min for IABC
samples. =
0.942 L/min for impinger samples. |
|
(c) |
Sample solution volume for desorbing IABC samples
= 3.0 mL Sample solution volume for impinger samples = 10.0
mL |
4.9. Evaluation of a Prefilter and a Modified Sampling Tube
As previously discussed, particulate iodide compounds may interfere
with the determination of iodine in workplace atmospheres. Past
research regarding aerosols (5.21.) has indicated that particulate in
the air sampled may penetrate any glass wool plugs and the sorbent
when using conventional sampling tubes. Different types of prefilters
have been be used to assist in capturing particulate before entry into
the sampling tube. A study was conducted to evaluate the possibility
of I2 reacting with a prefilter/cassette or
a MST device to capture iodides or other particulate.
Procedure: Evaluations were performed using either IABC
sampling tubes with prefilter sampling assemblies (5-F pore size,
25-mm diameter PVC filter/carbon-filled polypropylene cassette), or
MSTs with Teflon® filter [similar to Type II
tubes for SO2 (OSHA Method No. ID-200)
without polyurethane foam] for particulate and vapor collection.
A test was conducted by taking six IABC samples without prefilters
side-by-side with six IABC samples connected to prefilters. Another
test was performed by taking six IABC samples side-by-side with six
MSTs. All samples were taken at a flow rate of about 0.5 L/min for 5
min. The generation system concentration was approximately at the
Ceiling PEL for iodine.
Results: The results of the comparison of IABC samples
taken, with and without prefilters, and MSTs are displayed in Table 9.
As shown, a difference in the amount of I2
collected was noted between the prefilter/IABC and IABC, and not noted
between MST and IABC. The PVC prefilter/cassette does appear to
slightly react with I2 when using the
sampling conditions stated in Section 2. The PVC filter/cassette
assembly is not recommended for particulate sample collection
when also sampling I2. The MST device may be
used for collection of I2. Glass wool is
used for separation in the sampling tube rather than foam. Some foams
will absorb or react with iodine and subsequently contribute to lower
recoveries.
Table 9 Comparison Study - Known Concentration = 0.105 ppm
I2 With/Without Prefilter and Modified
Sampling Tube (25°C and 50% RH)
|
N |
Mean |
SD |
CV2 |
Recovery, % |
IABC (WOPF) |
6 |
0.103 |
0.004 |
0.036 |
98.1 |
IABC (WPF) |
6 |
0.077 |
0.004 |
0.050 |
73.3 |
MST |
6 |
0.100 |
0.005 |
0.054 |
95.2 |
Notes: |
|
(a) |
IABC (WOPF) |
= |
Impregnated activated beaded carbon without
a prefilter/cassette assembly. |
IABC (WPF) |
= |
Impregnated activated beaded carbon with a
prefilter/cassette assembly. |
MST |
= |
Modified sampling tube as described in
Section 2.1.6.. | |
(b) |
The MST device: The dimensions of the front
portion of the glass jacket are 12-mm o.d., 10-mm i.d., and
25-mm long and is used to retain the
Teflon®
particulate-collecting filter. The second part of
the glass tube contains the two sorbent sections for
I2 collection (100 mg IABC front and
50 mg backup). The dimensions of the second part are 6-mm o.d.,
4-mm i.d., and 50-mm long. After sampling, both sampling tube
ends are sealed with plastic caps. |
(c) |
Teflon® prefilter
analyzed after sampling contained 0.008 ± 0.001 ppm as
I2. |
(d) |
Sampling Time = 5 min Flow Rate = 0.526 to
0.544 L/min |
(e) |
Sample Solution Volume for Desorption = 3.0
mL |
4.10. Evaluation of Impregnated Charcoal Sampling Tube (OSHA Method
No. ID-177) vs. the IABC tube
Procedure: A side-by-side test using the previous OSHA
sampling device for I2 was conducted. The
prior device was a glass tube containing base-impregnated charcoal
(SKC Inc., Cat. No. 226-67) and glass wool plugs. Lot number 411 was
chosen for the test. The I2 vapor was
collected by taking six impregnated charcoal sampling tubes (ICST)
side-by-side with six IABC tubes using the generation system and
sampling conditions are stated as follows for both sampling media:
(a) |
Sampling Time |
= |
15 min |
(b) |
Flow Rate |
= |
0.526 to 0.544 L/min |
(c) |
Desorption Vol |
= |
3.0 mL |
Results: Results are listed in Table 10. As shown, the
average blank value for SKC lot no. 411 contains 5.50 µg of
I2. This is equivalent to 0.21 ppm of
I2 if a 2.5-L air volume is used in
calculations, and indicates serious contamination of this lot. Table
10 also shows results of I2 collected in
these tubes with/without blank correction.
Table 10 Evaluation of Impregnated Charcoal Sampling
Tube (Known Concentration = 0.105 ppm
I2) (25°C and 50% RH)
|
N |
Mean |
SD |
CV |
Recovery, % |
ICST (BT) |
6 |
5.50 µg |
0.37 µg |
0.067 |
- |
ICST (WOBC) |
6 |
0.162 ppm |
0.010 ppm |
0.060 |
154.3 |
ICST (WBC) |
6 |
0.096 ppm |
0.010 ppm |
0.107 |
91.4 |
IABC (BT) |
6 |
ND |
- |
- |
- |
IABC |
6 |
0.103 ppm |
0.004 ppm |
0.036 |
98.1 |
Notes: |
(a) |
ICST (BT) |
= |
Blank Impregnated Charcoal Sampling Tube |
|
(b) |
ICST (WOBC) |
= |
Impregnated Charcoal Sampling Tube without blank
correction. |
|
(c) |
ICST (WBC) |
= |
Impregnated Charcoal Sampling Tube with blank
correction. |
|
(d) |
IABC (BT) |
= |
Blank Impregnated Activated Beaded Carbon
tube |
|
(e) |
ICSTs were taken from SKC lot
411. |
|
(f) |
ND |
= |
None detectable (<0.01 µg
I2) |
As shown, the IABC and impregnated charcoal recoveries are similar,
provided blank corrections are made to the impregnated charcoal
results.
4.11. Confirmation of I2 from
IO3- Peak
The collected I2 is converted to
I- and IO3- by the IABC sorbent
as shown by the chemical reaction discussed in Section 1.2. If
IO3- can also be analyzed, additional
evidence of the presence of I2 can be
obtained.
Procedure: A previous analysis using IC has demonstrated
that the IO3- peak had interferences,
presumably from the KOH used to impregnate the sorbent, and from other
anions, such as fluoride (F-), and chlorite (ClO2-). To analyze
IO3-, an alternate analytical procedure was
used to minimize interference problems. In order to demonstrate the
disproportionation product IO3-,
I2 samples were prepared by dissolving small
amounts of pure I2 (U.S.P., J.T. Baker
Chemical Co., NJ) in the collecting solution (1.5 mM
Na2CO3 and 1.5 mM
NaHCO3). Two different detectors
(conductivity or UV) were tried for analysis of
IO3-. Samples were analyzed for
IO3- using each detector separately.
Typical operating conditions for a Dionex 4000i or 4500i with a
conductivity or UV detector and an automated sampler are listed below:
Ion Chromatograph - IO3-
Analysis
Eluent: |
1.0 mM
Na2CO3/1.0
mM NaHCO3 |
Column temperature: |
ambient |
Anion precolumn: |
AG5 |
Anion separator column: |
AS5 |
Anion self-regeneration suppressor: |
ASRS-1 (4 mm)* |
Conductivity output range: |
1 µS* |
UV output range: |
0.1 AU** |
Wavelength: |
200 nm** |
Rise time: |
5.0 s** |
Sample injection loop: |
50 µL |
*Conductivity detector only **UV detector only
Pump - IO3- Analysis
Pump pressure: |
900
psi |
Flow rate: |
2 mL/min |
Chromatogram - IO3- Analysis
Run time: |
4 min |
Peak retention time: |
1.2 min for
IO3- |
Results: A 10 µg/mL IO3-
standard and an I2 sample using conductivity
and UV detectors are presented in Figure 3.
uS = MicroSiemens AU = Absorbance Unit
Figure 3
The preliminary determination of IO3-
using either detector appears satisfactory; however low sensitivity
for IO3- was evident. A further study to
determine detection limits was also conducted as discussed in Section
4.12.
4.12. Qualitative and Quantitative Detection Limit Study for Iodate
Procedure: Low concentration samples of
IO3- were prepared by spiking desorbing
solutions (Section 3.3.2.) with aliquots of aqueous standards prepared
from KIO3 (Section 3.3.6.). These samples
were analyzed using a 50-µL sample injection loop and a
conductivity detector setting of 0.1 MicroSiemens (FS). The modified
NIOSH method previously discussed in Section 4.7. was used.
Results: The results are shown in Table 11 for qualitative
and quantitative detection limits, respectively. The qualitative
detection limit is 1.01 µg/mL as IO3-
at the 99.8% confidence level. The quantitative detection limit is
3.36 µg/mL as IO3-. Using a 2.5-L air
volume and a 3-mL sample solution volume, the qualitative
limit is 0.17 ppm and the quantitative limit is 0.57 ppm as
I2.
Table 11 Qualitative and Quantitative Detection
Limits
|
|
----------------------IO3-
Level------------------ |
|
1.0 µg/mL |
2.0 µg/mL |
3.0 µg/mL |
Sample No. |
PA |
PA |
PA |
|
1 |
7.73 |
20.36 |
34.02 |
2 |
7.65 |
23.77 |
31.51 |
3 |
7.42 |
16.63 |
32.85 |
4 |
11.74 |
20.68 |
27.65 |
5 |
6.21 |
17.09 |
30.25 |
6 |
10.68 |
18.02 |
37.92 |
|
PA = Integrated Peak Area
(IO3-)/10,000 The blank and 0.1,
0.2 and 0.5 µg/mL integrated peak areas, and their
standard deviations (Std Dev) were all equal to zero. |
|
The response of the low-level calibration samples were plotted to
obtain the linear regression equation (Y = mX + b), and the predicted
responses ( i) at each
X.
Using the equations: |
Sy |
= |
[S( i -
Yi)2/(N -
2)]½ |
|
Q1 |
= |
(3Sy + B - b)/m |
|
Q2 |
= |
3.33 Q1 |
Therefore, |
Q1 |
= |
(3Sy + B - b)/m = 1.01
µg/mL as IO3- |
|
 |
3.04 µg as
IO3- (3-mL sample volume). |
|
 |
0.17 ppm I2
(2.5-L air volume). |
|
Q2 |
= |
3.33 Q1 = 0.57 ppm I2
(2.5-L air volume). |
The ability to confirm the presence of I2
using IO3- is compromised by the low
sensitivity noted here. If there is sufficient quantity of
I2 in the collected air samples, the
IO3- analysis using the conditions specified
in Section 4.11. can be used. Samples could be taken for longer
periods of time to collect sufficient amounts of
IO3- for detection; however, this would
defeat the monitoring criteria that iodine is regulated as a Ceiling
unless separate short- and long-term samples are taken. Also, if a
bulk material is available, the I2 content
could also be examined by assessing both I- and
IO3- results, provided there is sufficiently
high concentration of I2 in the bulk.
4.13. Summary
The validation results indicate the method meets both the NIOSH and
OSHA criteria for accuracy and precision (5.15., 5.16.). Performance
during collection efficiency, breakthrough, and storage stability
tests is adequate. Unfortunately, it appears that recovery is
humidity-dependent and decreases as humidity increases.
Further study is needed to determine the cause; therefore, this method
is considered an interim method. The low recovery at higher RHs is
similar to results found in the previous OSHA method for iodine
(5.4.). At higher RHs, samples can be taken using a collecting
solution/impinger system, especially if low
I2 concentrations are expected; however, the
inconvenience of collection is readily apparent when using bubblers.
Detection limits (as I-) are adequate when samples are
taken for 5 min at 0.5 L/min. In principle, the collected
I2 can also be calculated from an
IO3- analysis using the appropriate
stoichiometric factor. Unfortunately, high detection limits and
interferences limit the application of the
IO3- for the determination of
I2. Confirmation of
I2 can occur if concentrations exceed
detection limits stated in Section 4.12. or more sensitive analytical
technology is developed and used.
5. References
5.1. Occupational Safety and Health Administration Salt Lake
Technical Center: Internal Document. Salt Lake City, UT,
1979.
5.2. Occupational Safety and Health Administration Salt Lake
Technical Center: Determination of Iodine in Workplaces as
Iodide using an Ion Specific Electrode (USDOL/OSHA Method No.
ID-170-SG). Salt Lake City, UT, 1985.
5.3. Occupational Safety and Health Administration Salt Lake
Technical Center: Determination of Iodine in Workplaces as
Iodide using an Ion Chromatograph (USDOL/OSHA-SLCAL Method No.
ID-169-SG). Salt Lake City, UT, 1985.
5.4. Occupational Safety and Health Administration Salt Lake
Technical Center: Iodine in Workplace Atmospheres (Solid
Sorbent) (USDOL/OSHA-SLCAL Method No. ID-177). revised, 1992.
5.5. Occupational Safety and Health Administration Salt Lake
Technical Center: Phosphine in Workplace Atmospheres and Backup
Report (USDOL/OSHA Method No. ID-180). In OSHA Analytical
Methods Manual. 2nd ed. Cincinnati, OH: American Conference of
Governmental Industrial Hygienists, 1991.
5.6. Occupational Safety and Health Administration Salt Lake
Technical Center: Sulfur Dioxide in Workplace Atmospheres
(USDOL/OSHA Method No. ID-200). In OSHA Analytical Methods Manual.
2nd ed. Cincinnati, OH: American Conference of Governmental Industrial
Hygienists, 1991.
5.7. Lewis, R.J., ed.: Hawley's Condensed Chemical
Dictionary. 12th ed. New York: Van Nostrand Reinhold Co., 1993.
5.8. Lide, D.R., ed: CRC Handbook of Chemistry and
Physics. 73rd ed. Boca Raton, FL: CRC Press, Inc., 1992.
5.9. American Conference of Governmental Industrial
Hygienists: Documentation of the Threshold Limit Values and
Biological Exposure Indices. 5th ed. Cincinnati, OH: American
Conference of Governmental Industrial Hygienists, 1986.
5.10. Flury, F. and F. Zernik: Schadliche Gase.
Berlin: Julius Springer, 1931.
5.11. Clayton, G.D. and F.E. Clayton, ed.: Patty's
Industrial Hygiene and Toxicology. 3rd ed. New York: John Wiley
and Sons, 1981.
5.12. Sittig, M.: Handbook of Toxic and Hazardous
Chemicals. Park Ridge, NJ: Noyes Publications, 1981.
5.13. Occupational Safety and Health Administration Salt Lake
Technical Center: Ion Chromatography Standard Operating Procedure
(Ion Chromatographic Committee). Salt Lake City, UT. In progress.
5.14. Mandel, J.: Accuracy and Precision, Evaluation and
Interpretation of Analytical Results, The Treatment of Outliers. In
Treatise On Analytical Chemistry. 2nd ed., Vol. 1, edited by I.
M. Kolthoff and P. J. Elving. New York: John Wiley and Sons, 1978. pp.
282-285.
5.15. National Institute for Occupational Safety and Health:
Documentation of the NIOSH Validation Tests by D. Taylor, R.
Kupel, and J. Bryant (DHEW/NIOSH Pub. No. 77-185). Cincinnati, OH:
National Institute for Occupational Safety and Health, 1977. pp. 1-12.
5.16. Occupational Safety and Health Administration Salt Lake
Technical Center: Evaluation Guidelines of the Inorganic
Methods Branch. In OSHA Analytical Methods Manual. 2nd ed.
Cincinnati, OH: American Conference of Governmental Industrial
Hygienists, 1991. pp. 1-18.
5.17. Dowdy, S. and S. Wearden: Statistics for
Research. New York: John Wiley and Sons, 1983. Chapter 8.
5.18. Septon, J.C. and J.C. Ku: Workplace Air Sampling and
Polarographic Determination of Formaldehyde. Am. Ind. Hyg. Assoc.
J. 43:845-852 (1982).
5.19. Burkart, J.A.: General Procedures for Limit of
Detection Calculations in the Industrial Hygiene Chemistry Laboratory.
Appl. Ind. Hyg. 1:153-155 (1986).
5.20. National Institute for Occupational Safety and Health:
Standard Operating Procedures for Industrial Hygiene Sampling and
Chemical Analysis, SOP 018, Cincinnati, OH: National Institute for
Occupational Safety and Health, Revised Sept., 1992.
5.21. Long, G.L. and J.D. Winefordner: Limit of Detection --
A Closer Look at the IUPAC Definition. Anal. Chem. 55:712A-724A
(1983).
5.22. Fairchild, C.I. and M.I. Tillery: The Filtration
Efficiency of Organic Vapor Sampling Tubes against Particulates.
Am. Ind. Hyg. Assoc. J. 38:277-283 (1977).
Appendix
Analysis of Samples by Ion Specific Electrode
(ISE)
Samples may also be analyzed by ISE or in place of IC; however,
interferences particular to ISE may have to be considered. The following
procedure addresses the analysis of IABC or impinger samples by ISE.
Detection Limit and Range (ISE)
1. The quantitative detection limit is 0.25 µg of iodide in
a 25-mL sample solution. This corresponds to 0.004 ppm iodine for a
7.5-L air volume.
2. The range is from 0.25 µg to 0.25 g iodide based on a
25-mL solution volume. This corresponds to either 0.3 µg to 0.3
g iodine or 0.004 to 4,000 ppm iodine for a 7.5-L air volume.
Interferences [ISE - also see Iodide Ion Specific Electrode
(Model 94-53a) Instruction Manual, Orion Research Inc., Boston, MA or
other manufacturer instruction manuals if a different iodide electrode
is used.]
1. Either sulfide and cyanide, if present in the sampled
atmosphere, will give a negative interference; however, this can be
resolved by adding a nickel (Ni2+) solution
to the samples before analysis.
2. The maximum allowable ratios of interfering ions to iodide are 1
× 106, 5 × 103,
and 1 × 105 moles/L for chloride, bromide,
and thiosulfate, respectively. These are extremely high concentrations
and normally should not be seen when sampling industrial environments.
3. Iodide ions may form complexes with some metal ions which will
ultimately result in lower iodide recoveries. This problem can be
resolved by using a "known (standard) additions" method.
Equipment (ISE)
1. Ion Specific Electrode (ISE) and filling solution, iodide
(Model 94-53a, Orion Research Inc., Cambridge, MA).
2. Single junction reference electrode and filling solution (Model
90-01, Orion Research Inc.).
3. Millivolt/pH meter, capable of relative mV, pH, standard
addition or concentration measurements (Model EA 940 Expandable
Ionanalyzer, Orion Research Inc.).
4. Stirrer, electronic, or magnetic with
Teflon® stirring bars.
5. Miscellaneous laboratory glassware: Volumetric flasks, pipettes,
beakers, disposable beakers, 25-mL Erlenmeyer flasks, etc.
Reagents (ISE - All chemicals should be at least reagent
grade)
Sodium nitrate (NaNO3), Sodium
hydroxide (NaOH), Potassium iodide (KI), Sodium iodide (NaI)
1. Deionized water (DI H2O)
2. Sodium hydroxide, 0.01 N: Dissolve 0.4 g NaOH and dilute to 1-L
with DI H2O.
3. Ionic Strength Adjuster (ISA) - Sodium nitrate, 5 M: Dissolve
42.5 g NaNO3 in 100 mL DI
H2O.
4. Nickel (Ni2+) solution, 1,000
µg/mL: A commercially prepared 1,000 µg/mL solution of
nickel common for atomic absorption purposes can be used.
5. Standard stock solution, 1,000 µg/mL iodide: Place 1.31 g
KI or 1.18 g NaI in a 1-L volumetric flask. Add about 500 mL DI
H2O, swirl to dissolve, and dilute to the
mark with DI H2O.
6. Working iodide standard solutions, 100, 10, 1, and 0.1
µg/mL: Pipette appropriate volumes of 1,000 µg/mL stock
solution into volumetric flasks and dilute to volume with 0.01 N NaOH.
The 100 µg/mL standard is used for known additions as discussed
below.
Analysis (ISE - Known Additions)
Known Additions Spike Preparation:
1. Standard Spike, 100 µg/mL is added to all samples and
standards.
Note: The concentration of this spike should normally be at least
10 times the expected sample concentration. If concentrations of
iodine are expected to be large (> 10 µg/mL) or small
(< 0.2 µg/mL), the spike and standards used
should be adjusted accordingly.
Sample Preparation: For IABC samples follow Steps 1 to 3 below. For
impinger samples, follow Steps 4 and 5 only.
IABC Samples:
1. Carefully remove and discard the rear glass wool plug from each
glass tube without losing any IABC sorbent.
Note: The sorbent should always be removed from the glass tube via
the opposite end of collection (i.e. 50-mg IABC backup section is
removed first). This will minimize the possibility of contamination
from any collected particulate.
Carefully transfer each IABC section from a sample tube and place
into a separate 25-mL Erlenmeyer flask or 20-mL scintillation vial.
2. Add 1 mL of 1,000 µg/mL Ni2+
solution and pipette 24 mL of 0.01 N NaOH into each flask.
3. Cap tightly, shake vigorously, and allow the solution to sit for
at least 1 h.
Impinger Samples Only:
4. Transfer impinger sample solutions to separate 25-mL volumetric
flasks.
5. Add 1 mL of 1,000 µg/mL Ni2+
solution to each flask and dilute to volume with 0.01 N NaOH.
Electrode Check:
1. Set up the mV meter and electrodes according to the
manufacturers instruction manuals or Standard Operating Procedure
(SOP).
2. Place 100 mL DI H2O and 2 mL ISA (5 M
NaNO3) into a 250-mL beaker. Use the
relative mV scale setting on the mV meter and then place electrodes
(reference and iodide) in the solution.
3. Pipet 1.0 mL of the 1,000 µg/mL stock I-
standard into the solution while stirring. Allow reading to stabilize,
then record the mV of the solution.
4. Add 10 mL of the 1,000 µg/mL iodide stock standard while
stirring. Read the mV of the solution when stable. Correct electrode
operation is indicated by a difference of 55 to 59 mV (assuming the
solution temperature is between 20 to 25°C).
Analytical Procedure
1. If available, use a standard additions program intrinsic within
the instrument to calibrate and convert readings directly to
concentration values. If an automated program is not available, record
the mV reading prior to standard addition
(Eo) and after addition
(Es). The "standard addition" normally is a
2.5-mL aliquot of 100 µg/mL iodide working standard (see note
on previous page for information).
2. Rinse the electrodes, blot dry, and place in a 25 mL sample or
working standard solution. Add 0.5 mL of ISA. Allow time for the
reading (Eo) to stabilize.
3. Using a glass or automatic pipet, add 2.5 mL of the 100
µg/mL Standard Spike, and allow time for the reading to
stabilize. Take a final reading (Es or
concentration for automated programs).
4. Analyze a standard in the concentration range of the samples
after every fifth or sixth sample and at the end of the analysis.
Note: The ISE can be affected by changes in temperature. Standards
and samples should be at the same temperature before analyzing.
Fluctuations in the ambient temperature during analysis can sometimes
be compensated for by slope adjustment. Refer to manufacturer
instruction manuals for further details.
Calculations (ISE)
1. Determine the total µg iodine content of each sample and
blank using a concentration-response (concentration units
versus µg) linear regression curve if readings were measured in
concentration units. If mV readings were taken, plot the mV readings
using an appropriate standard additions program. An example of
equations used for standard additions can be found in ISE user
manuals.
2. The concentration of iodine in the air sample is expressed in
ppm:
ppm I2 = |
(24.45) (µg/mL Iodide) (sample
volume, mL) (mole ratio)
(MW) (air volume, L) |
Where:
Sample volume |
25.0 mL |
Mole ratio of I2 to
Iodide |
1.2 |
Molecular weight (MW) of
I2 |
253.8 |
Therefore, for a 25 mL sample volume:
ppm I2 = |
(2.89) (µg/mL Iodide)
(MW) (air volume, L) |
|