ACRYLIC ACID METHACRYLIC ACID
Method number: |
PV2005 |
|
|
Matrix: |
Air |
|
Target concentration: |
acrylic acid: |
2 ppm (5.9 mg/m3) (ACGIH TLV)
(skin) |
|
methacrylic acid: |
20 ppm (70 mg/m3) (ACGIH TLV) |
|
Procedure: |
Samples are collected by drawing a known volume of air
through two Anasorb 708 tubes connected in series. Samples are
desorbed with 2 mL of methanol for 1 hour with shaking and analyzed
by liquid chromatography using an ultraviolet detector at 210 nm
(LC-UV). |
|
Recommended air volume and sampling rate: |
24 L at 0.1 L/min |
|
Reliable quantitation limit: |
acrylic acid: |
0.00301 ppm (0.00888 mg/m3) |
|
methacrylic acid: |
0.00475 ppm (0.0170 mg/m3) |
|
Status of method: |
Partially Evaluated Method. This method has been
subjected to established evaluation procedures, and is presented for
information and trial use. |
|
|
Date: July, 1996 |
|
Chemist: Mary E.
Eide |
Organic Service Branch I OSHA Salt Lake Technical
Center Salt Lake City, UT 84165-0200
1. General Discussion
1.1 Background
1.1.1 History
There is an OSHA validated method (28) for acrylic acid (Ref.
5.1) and a stop-gap method for methacrylic acid (Ref.
5.2) which use two XAD-8 tubes connected in series for
sampling in the sampling train. SKC is no longer making
XAD-8 tubes, and state that Anasorb 708 tubes are the
equivalent. The purpose of this study was to determine whether the
Anasorb 708 tubes could be substituted for the XAD-8
tubes. The desorption, retention, and storage studies indicate that
the Anasorb 708 tubes are a good substitution for the
XAD-8 tubes.
1.1.2 Toxic effects (This section is for information only and
should not be taken as the basis of OSHA policy.) (Ref. 5.3 and Ref.
5.4)
Acrylic acid is an acute irritant to skin, eyes, and mucous
membranes. Acrylic acid is readily adsorbed through the skin. Rats
exposed to 300 ppm acrylic acid for 5 days/week for 4 weeks showed
nose irritation, lethargy, and reduced weight gain. Mice exposed to
75 ppm acrylic acid 6 hours/day 5 days/week for 13 weeks showed
slight degenerative lesions on the nasal mucous membranes.
Methacrylic acid is a severe contact irritant, and direct contact
can cause blindness and skin ulceration. Rats exposed to 300 ppm
methacrylic acid for 20 days showed slight renal congestion. The
TLVs of 2 ppm for acrylic acid and 20 ppm for methacrylic acid were
established at these levels to prevent injury due to exposure to
these compounds.
1.1.3 Workplace exposure (Ref. 5.3 and 5.4)
Acrylic acid and methacrylic acid are used as a monomers for the
manufacture of resins and polymers, and in organic syntheses. The
U.S. production of acrylic acid and its esters is about 500,000 tons
per year.
1.1.4 Physical properties and other descriptive information (Ref.
5.5 and 5.6)
Acrylic acid |
|
Synonyms:
CAS
number: IMIS: RTECS: DOT: Molecular
weight: Flash point: Boiling point: Melting
point: Odor: Odor threshold: Color: Autoignition
temperature: Density: Molecular formula: Structural
formula: |
Acroleic acid; Ethylene carboxylic acid; Propene acid;
Propenoic acid; Vinyl formic
acid 79-10-7 0117 AS4375000 UN 2218 corrosive
liquid 72.06 68°C
(155°F)(oc) 141°C 14°C acrid 1 ppm colorless
liquid 238°C
(820°F) 1.05204
(g/mL) C3H4O2
 |
|
Methacrylic acid |
Synonyms:
CAS
number IMIS: RTECS: DOT: Molecular
weight: Flash point: Boiling point: Melting
point: Odor: Color: Autoignition
temperature: Density: Molecular formula: Structural
formula: |
alpha-Methacrylic acid;
2-Methylenepropionic acid;
2-Methylpropenoic acid;
2-Methyl-2-propenoic acid
79-41-4 M339 OZ2975000 UN2531 corrosive
liquid 86.09 76°C
(170°F)(coc) 163°C 15°C acrid, like acetic
acid colorless to pale yellow liquid 435°C
(815°F) 1.0153254
(g/mL) C4H6O2
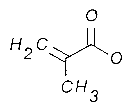 |
The analyte air concentrations throughout this method are based on the
recommended sampling and analytical parameters. Air concentrations listed
in ppm are referenced to 25°C and 101.3 kPa (760 mmHg).
1.2 Limit defining parameters
1.2.1 Detection limit of the overall procedure (DLOP)
The detection limit of the overall procedure for acrylic acid is
0.064 µg per sample (0.001 ppm or 0.00267
mg/m3; and for methacrylic acid is 0.123
µg per sample (0.0015 ppm or 0.00513
mg/m3). This is the amount of analyte
spiked on the sampler that will give a response that is
significantly different from the background response of a sampler
blank.
The DLOP is defined as the concentration of analyte that gives a
response (YDLOP) that is significantly
different (three standard deviations
(SDBR)) from the background response
(YBR).
YDLOP -
YBR =
3(SDBR)
The direct measurement of YBR and
SDBR in chromatographic methods is
typically inconvenient, and difficult because
YBR is usually extremely low. Estimates of
these parameters can be made with data obtained from the analysis of
a series of samples whose responses are in the vicinity of the
background response. The regression curve obtained for a plot of
instrument response versus concentration of analyte will usually be
linear. Assuming SDBR and the precision of
data about the curve are similar, the standard error of estimate
(SEE) for the regression curve can be substituted for
SDBR in the above in the above equation.
The following calculations derive a formula for the DLOP:
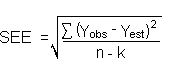
Yobs |
= |
observed response |
Yest |
= |
estimated response from regression curve |
n |
= |
total no. of data points |
k |
= |
2 for a linear regression curve |
At point YDLOP on the regression curve
YDLOP = A(DLOP) +
YBR |
A = analytical sensitivity
(slope) |
Substituting 3(SEE) + YBR for
YDLOP gives
The DLOP is measured as mass per sample and expressed as
equivalent air concentrations, based on the recommended sampling
parameters. Ten samplers were spiked with equal descending
increments of analyte, such that the lowest sampler loading was 0.2
µg/sample. This is the amount, when spiked on a sampler, that
would produce a peak approximately 10 times the background response
for the sample blank. These spiked samplers, and the sample blank,
were analyzed with the recommended analytical parameters, and the
data obtained used to calculate the required parameters (A and SEE)
for the calculation of the DLOP. Values of 5157 and 109.9 were
obtained for A and SEE respectively for acrylic acid. The DLOP for
acrylic acid was calculated to be 0.064 µg/sample (0.001
ppm). Values of 2838 and 116 were obtained for A and SEE
respectively for methacrylic acid. The DLOP for methacrylic acid was
calculated to be 0.123 µg/sample (0.0015 ppm).
Table 1.2.1.1 Detection Limit of the Overall
Procedure for acrylic acid
|
mass per sample |
area counts |
(µg) |
(µV-s) |
|
0.2 |
2048 |
0.4 |
2732 |
0.6 |
3824 |
0.8 |
4865 |
1.0 |
6039 |
1.2 |
6890 |
1.4 |
8103 |
1.6 |
9069 |
1.8 |
10113 |
2.0 |
11127 |
|
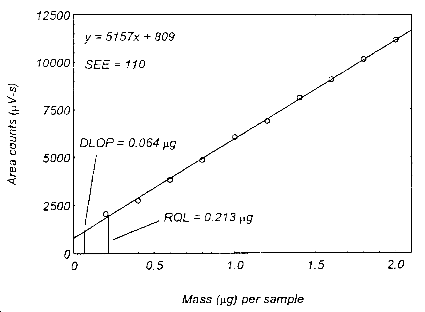 Figure 1.2.1.1. Plot of data to determine the DLOP/RQL
for acrylic acid.
Table 1.2.1.2 Detection Limit of
the Overall Procedure for methacrylic acid
|
mass per sample |
area counts |
(µg) |
(µV-s) |
|
0.2 |
1138 |
0.4 |
1427 |
0.6 |
1985 |
0.8 |
2724 |
1.0 |
3278 |
1.2 |
3730 |
1.4 |
4569 |
1.6 |
4910 |
1.8 |
5455 |
2.0 |
6122 |
|
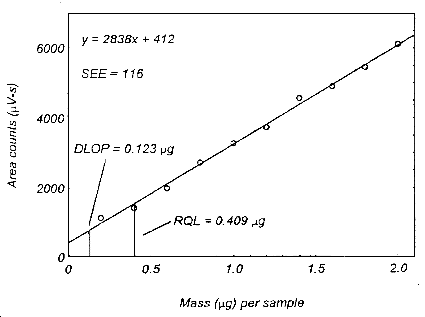 Figure 1.2.1.2. Plot of data to determine the DLOP/RQL
for methacrylic acid.
1.2.2 Reliable quantitation limit (RQL)
The reliable quantitation limit is 0.213 µg per sample for
acrylic acid (0.00301 ppm), and 0.409 µg per sample for
methacrylic acid (0.00475 ppm). This is the amount of analyte spiked
on a sampler that will give a signal that is considered the lower
limit for precise quantitative measurements.
The RQL is considered the lower limit for precise quantitative
measurements. It is determined from the regression line data
obtained for the calculation of the DLOP (Section 1.2.1 ), providing
at least 75% of the analyte is recovered. The RQL is defined as the
concentration of analyte that gives a response
(YRQL) such that
YRQL -
YBR =
10(SDBR)
therefore
The RQL is the lowest loading at which 75% of the analyte, or
more, can be recovered as determined from the regression line of the
plotted data.
Table 1.2.2.1 Reliable
Quantitation Limit
|
mass per sample (µg) |
mass recovered (µg) |
recovery (%) |
|
0.2 |
0.197 |
98.5 |
0.4 |
0.388 |
97.0 |
0.6 |
0.592 |
98.7 |
0.8 |
0.780 |
97.5 |
1.0 |
0.941 |
94.1 |
1.2 |
1.189 |
99.1 |
1.4 |
1.387 |
99.1 |
1.6 |
1.582 |
98.9 |
1.8 |
1.753 |
97.4 |
2.0 |
1.934 |
96.7 |
|
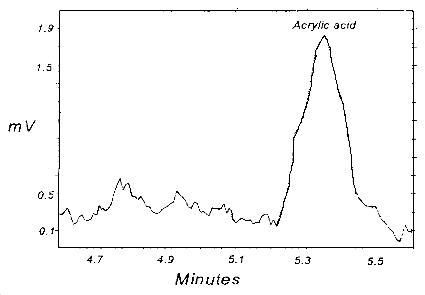 Figure 1.2.2.1 A chromatogram of the RQL for acrylic
acid.
Table 1.2.2.2 Reliable
Quantitation Limit
|
mass per sample (µg) |
mass recovered (µg) |
recovery (%) |
|
0.2 |
0.196 |
98.0 |
0.4 |
0.396 |
99.0 |
0.6 |
0.592 |
98.7 |
0.8 |
0.772 |
96.5 |
1.0 |
0.998 |
99.8 |
1.2 |
1.188 |
99.0 |
1.4 |
1.340 |
95.7 |
1.6 |
1.534 |
95.9 |
1.8 |
1.787 |
99.3 |
2.0 |
1.974 |
98.7 |
|
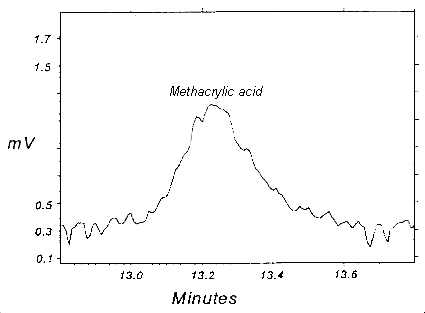 Figure 1.2.2.2 A chromatogram of the RQL for
methacrylic acid.
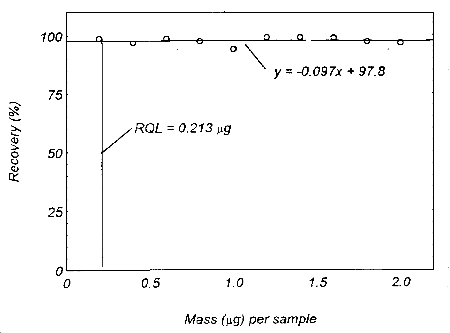 Figure 1.2.2.3 Plot of data to determine the RQL for
acrylic acid.
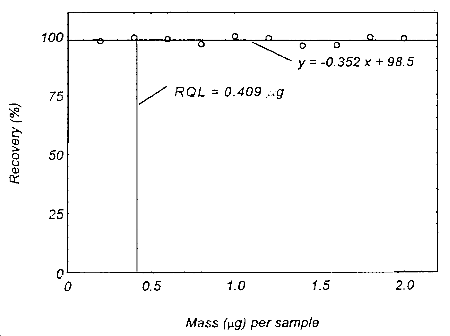 Figure 1.2.2.4 Plot of data to determine the RQL for
methacrylic acid.
2. Sampling Procedure
2.1 Apparatus
2.1.1 Samples are collected using a personal sampling pump
calibrated, with the sampling device attached, to within ±5% of the
recommended flow rate.
2.1.2 Samples are collected with 7 cm × 4 mm i.d. × 6 mm o.d.
glass sampling tubes packed with one section of 100 mg of Anasorb
708 in series. The section is held in place with glass wool plugs,
in each tube. For this evaluation, commercially prepared sampling
tubes were purchased from SKC, Inc. (Fullerton, CA, catalog no.
226-30-8).
2.2 Technique
2.2.1 Immediately before sampling, break off the ends of the
sampling tube. A sampling train is assembled by connecting two tubes
in series using the red plastic end cap, after the sealed end has
been cut off. A small piece of flexible plastic tubing may be
substituted for the cut red plastic end caps. The inside broken ends
of the two Anasorb 708 tubes should be as close together as
possible, after the sampling train is assembled. All tubes should be
from the same lot.
2.2.2 Attach the sampling train to the pump with flexible tubing.
It is desirable to utilize sampling tube holders which have a
protective cover to shield the employee from the sharp, jagged end
of the sampling tube.
2.2.3 Air being sampled should not pass through any hose or
tubing before entering the sampling train.
2.2.4 Attach the sampling train vertically with the outer tube
pointing downward, in the worker's breathing zone, and positioned so
it does not impede work performance or safety.
2.2.5 After sampling for the appropriate time, remove the sample
train and seal each tube with intact plastic end caps. Wrap each
tube separately end-to-end with a Form
OSHA-21 seal.
2.2.6 Submit at least one blank sample with each set of samples.
Handle the blank sampler in the same manner as the other samples
except draw no air through it.
2.2.7 Record sample volumes (in liters of air) for each sample,
along with any potential interferences.
2.2.8 Ship any bulk samples separate from the air samples.
2.2.9 Submit the samples to the laboratory for analysis as soon
as possible after sampling. If delay is unavoidable, store the
samples in a refrigerator.
2.3 Desorption efficiency
2.3.1 The desorption efficiencies of acrylic acid were
determined by liquid-spiking the Anasorb 708 tubes at
loadings of 0.1 to 2 times the target concentration. The loadings on
the tubes were 8, 40, 80, and 160µg of acrylic acid. These
samples were stored overnight at ambient temperature and then
opened, placed into 4 mL vials, desorbed with 2 mL methanol for 1
hour on the shaker, and analyzed by LC-UV. The average desorption
efficiency over the studied range was 98.7%.
Table 2.3.1 Desorption
Efficiency of Acrylic acid
|
Tube # |
% Recovered |
|
0.1 × |
0.5 × |
1.0 × |
2.0 × |
|
8 µg |
40 µg |
80 µg |
160 µg |
|
1 |
98.0 |
98.6 |
98.1 |
99.7 |
2 |
98.4 |
98.5 |
98.2 |
99.5 |
3 |
99.9 |
98.6 |
98.5 |
99.0 |
4 |
98.8 |
99.2 |
98.2 |
99.2 |
5 |
97.0 |
98.6 |
99.0 |
98.8 |
6 |
98.5 |
98.0 |
99.2 |
99.0 |
average |
98.4 |
98.6 |
98.5 |
99.2 |
overall average |
98.7 |
standard deviation |
±0.629 |
|
2.3.2 The desorption efficiencies of methacrylic acid were
determined by liquid-spiking the Anasorb 708 tubes at
loadings of 0.1 to 2 times the target concentration. The loadings on
the tubes were 71, 355, 711, and 1420 µg of methacrylic acid.
These samples were stored overnight at ambient temperature and then
desorbed and analyzed. The average desorption efficiency over the
studied range was 98.6%.
Table 2.3.2 Desorption
Efficiency of Methacrylic acid
|
Tube # |
% Recovered |
|
0.1 × |
0.5 × |
1.0 × |
2.0 × |
|
71 µg |
355 µg |
711 µg |
1420 µg |
|
1 |
96.9 |
98.9 |
98.3 |
98.7 |
2 |
99.1 |
99.6 |
98.8 |
98.7 |
3 |
98.0 |
98.8 |
98.7 |
98.3 |
4 |
97.8 |
98.0 |
98.8 |
99.2 |
5 |
98.0 |
97.2 |
98.6 |
101 |
6 |
99.2 |
98.1 |
98.9 |
98.5 |
average |
98.2 |
98.4 |
98.7 |
99.1 |
overall average |
98.6 |
standard deviation |
±0.810 |
|
2.4 Retention efficiency
The sampling tubes were spiked at the 2 × PEL level, loadings of
160 µg acrylic acid and 1420 µg methacrylic acid,
allowed to equilibrate 4 hours, and then had 24 L humid air (81% RH at
21°C) pulled through them at 0.1 Lpm. They were opened, desorbed, and
analyzed by LC-UV. The retention efficiency averaged
98.9% for acrylic acid and 99.7% for methacrylic acid. There was
little or no acrylic and methacrylic acids found on the back sections
of the tubes.
Table 2.4.1 Retention Efficiency
of Acrylic acid
|
Tube # |
% Recovered |
|
Front section |
Back section |
Total |
|
1 |
99.9 |
0.0 |
99.9 |
2 |
98.6 |
0.1 |
98.7 |
3 |
100 |
0.0 |
100 |
4 |
97.1 |
0.3 |
97.4 |
5 |
98.6 |
0.2 |
98.8 |
6 |
98.4 |
0.1 |
98.5 |
|
|
average |
98.9 |
|
Table 2.4.2 Retention Efficiency
of Methacrylic acid
|
Tube # |
% Recovered |
|
Front section |
Back section |
Total |
|
1 |
100 |
0.0 |
100 |
2 |
95.6 |
2.0 |
97.6 |
3 |
101 |
0.0 |
101 |
4 |
98.7 |
0.0 |
98.7 |
5 |
101 |
0.0 |
101 |
6 |
99.9 |
0.0 |
99.9 |
|
|
average |
99.7 |
|
2.5 Sample storage
The front sections of twelve sampling tubes were each spiked with
80 µg acrylic acid and 711 µg methacrylic acid. Twelve
more tubes were spiked at the same loadings and then had 24 liters of
humid air (81% RH at 22°C) drawn through them at 0.1 Lpm. Six samples
from each group were stored at room temperature (24°C) and the other
six tubes stored at refrigerator temperature (-4°C). Three samples of
each type were analyzed after 7 days and the remaining three samples
of each type after 14 days. The amounts recovered, corrected for
desorption efficiency, indicate good storage stability for the time
period studied and had an average recovery of 99.3% for all acrylic
acid conditions, and 99.4% for all methacrylic acid conditions.
Table 2.5.1 Storage Test for
Acrylic acid
|
Time |
% Recovery |
% Recovery |
% Recovery |
% Recovery |
(days) |
Dry |
Dry |
Humid |
Humid |
|
Refrigerated |
Ambient |
Refrigerated |
Ambient |
|
7 |
100 |
100 |
99.9 |
99.8 |
7 |
99.6 |
99.9 |
100 |
99.1 |
7 |
99.2 |
99.3 |
98.0 |
99.0 |
14 |
98.8 |
100 |
98.1 |
99.6 |
14 |
99.9 |
99.2 |
99.8 |
98.2 |
14 |
99.2 |
99.5 |
99.0 |
97.0 |
average |
99.5 |
99.7 |
99.1 |
98.8 |
|
Table 2.5.2 Storage Test for
Methacrylic acid
|
Time |
% Recovery |
% Recovery |
% Recovery |
% Recovery |
(days) |
Dry |
Dry |
Humid |
Humid |
|
Refrigerated |
Ambient |
Refrigerated |
Ambient |
|
7 |
100 |
100 |
100 |
99.7 |
7 |
99.2 |
99.6 |
100 |
100 |
7 |
99.3 |
99.3 |
100 |
98.8 |
14 |
98.8 |
99.5 |
102 |
98.2 |
14 |
100 |
101 |
98.9 |
97.6 |
14 |
99.5 |
98.2 |
97.0 |
98.6 |
average |
99.5 |
99.6 |
99.7 |
98.8 |
|
2.6 Recommended air volume and sampling rate.
Based on the data collected in this evaluation, 24 L air samples
should be collected at a sampling rate of 0.1 L/min.
2.7 Interferences (sampling)
2.7.1 It is not known if any compounds will severely interfere
with the collection of acrylic and methacrylic acid on the sampling
tubes. In general, the presence of other contaminant vapors in the
air will reduce the capacity of the sampling tubes to collect
acrylic and methacrylic acid.
2.7.2 Suspected interferences should be reported to the
laboratory with submitted samples.
2.8 Safety precautions (sampling)
2.8.1 Attach the sampling equipment to the worker in such a
manner that it will not interfere with work performance or safety.
2.8.2 Follow all safety practices that apply to the work area
being sampled.
2.8.3 Wear eye protection should be worn when breaking the ends
of the glass sampling tubes.
3. Analytical Procedure
3.1 Apparatus
3.1.1 The instrument used in this study was a liquid
chromatograph equipped with an ultraviolet detector, specifically a
Waters 600 E pump and system controller, Waters 717 autosampler, and
Waters 490 E programmable multiwavelength detector.
3.1.2 An LC column capable of separating the analyte from any
interferences. The column used in this study was a LC-8-DB
column, 5µ film thickness, 25 cm long, 4.6 mm I.D.
3.1.3 An electronic integrator or some suitable method of
measuring peak areas.
3.1.4 Four milliliter vials with
TeflonTM-lined caps.
3.1.5 A 100 µL syringe or other convenient size for sample
injection.
3.1.6 Pipets for dispensing the desorbing solution.
3.1.7 Volumetric flasks - 10 mL and other convenient sizes for
preparing standards.
3.2 Reagents
3.2.1 Acrylic acid, Reagent grade.
3.2.2 Methacrylic acid, Reagent grade
3.2.3 Methanol, HPLC grade
3.2.4 Deionized water, the water used in this study was from a
Millipore Milli-Q water purification system.
3.2.5 Phosphoric acid, Reagent grade
3.2.6 Acetonitrile, HPLC grade
3.2.7 The mobile phase was 0.1:4:96 solution of phosphoric acid:
acetonitrile: water.
3.3 Standard preparation
3.3.1 At least two separate stock standards are prepared by
diluting a known quantity of acrylic and methacrylic acids with
methanol. The concentration of these stock standards was 1050
µg/mL acrylic acid and 1015 µg/mL methacrylic acid.
3.3.2 Dilutions of these stock standards were prepared to bracket
the samples. The range of the standards used in this study was from
1.05 to 1050 µg/mL acrylic acid and 1.015 to 1015
µg/mL methacrylic acid.
3.4 Sample preparation
3.4.1 Sample tubes are opened and the front and back section of
each tube are placed in separate 4 mL vials.
3.4.2 Each section is desorbed with 2 mL of methanol.
3.4.3 The vials are sealed immediately and allowed to desorb for
1 hour with constant shaking.
3.5 Analysis
3.5.1 Liquid chromatograph conditions.
Injection size: |
10 µL |
|
Column:
| LC-8-DB, 5µ, 25cm, 4.6 mm I.D. |
|
Mobile phase:
| 96% water 4% acetonitrile 0.1% phosphoric
acid |
|
Detector: |
Waters 490 E programmable multiwavelength
detector at 210 nm. |
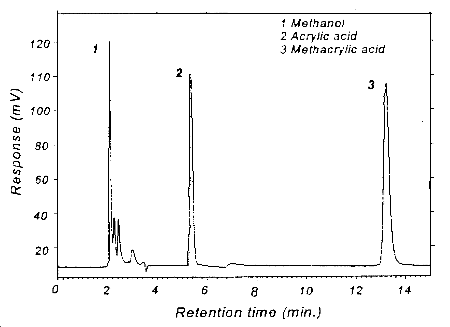 Figure 3.5 A chromatogram of an analytical standard
of 105 µg/mL acrylic acid and 101.5 µg/mL
methacrylic acid.
3.5.2 Peak areas are measured by an integrator or other suitable
means.
3.6 Interferences (analytical)
3.6.1 Any compound that produces a response and has a similar
retention time as the analyte is a potential interference. If any
potential interferences were reported, they should be considered
before samples are desorbed. Generally, chromatographic conditions
can be altered to separate an interference from the analyte.
3.6.2 When necessary, the identity or purity of an analyte peak
may be confirmed by GC-mass spectrometer or by another
analytical procedure.
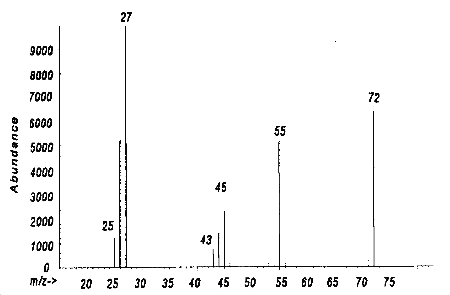 Figure 3.6.2.1 A mass spectrum of acrylic
acid.
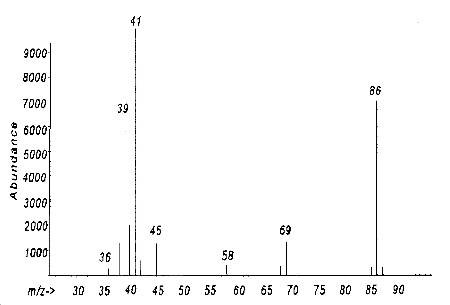 Figure 3.6.2.2 A mass spectrum of methacrylic
acid.
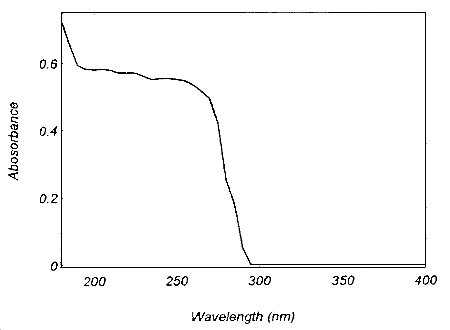 Figure 3.6.2.3 An UV spectra of acrylic
acid.
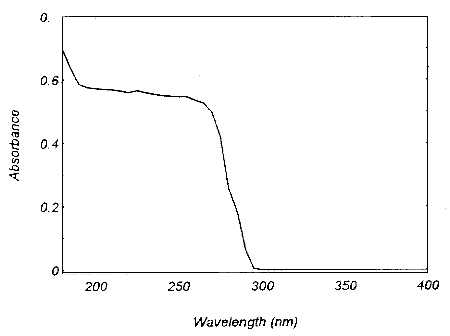 Figure 3.6.2.4 An UV spectra of methacrylic
acid.
3.7 Calculations
3.7.1 The calibration curve was made from at least four
standards at different concentrations bracketing the samples.
3.7.2 The values for the air samples and blanks are obtained from
the calibration curve.
3.7.3 Values (µg) obtained for blanks are subtracted from
air samples.
3.7.4 To calculate the concentration of analyte in the air sample
the following formulas are used:
(µg/m) (desorption volume)
(desorption efficiency) |
= mass of analyte in
sample |
(mass of analyte in sample)
molecular weight |
= number of moles of
analyte |
(number of moles of
analyte) |
(molar volume at 25°C &
760mm) |
= |
volume the analyte
will occupy at 25°C & 760mm |
(volume analyte occupies)
(106)*
(air volume) |
= ppm |
* All units must cancel.
3.7.5 The above equations can be consolidated to the following
formula.
(µg/mL)(DV)(24.46)(106)(g)(mg)
(24 L)(DE)(MW)(1000mg)(1000µg) |
= ppm |
µg/mL |
= concentration of analyte in sample or standard |
24.46 |
= Molar volume (liters/mole) at 25°C and 760 mm |
MW |
= Molecular weight (g/mole) |
DV |
= Desorption volume |
24 L |
= 24 liter air sample |
DE |
= Desorption efficiency |
3.8 Safety precautions (analytical)
3.8.1 Avoid skin contact and inhalation of all chemicals.
3.8.2 Wear safety glasses, gloves and a lab coat at all times
while in the laboratory areas.
4. Recommendations for Further Study
Collection studies should be performed from a dynamically generated
test atmosphere.
5. References
5.1 Cummins, K., Method 28, "Acrylic Acid", Organic Methods
Evaluation Branch, OSHA Salt Lake Technical Center, 1981.
5.2 Eide, M., "Methacrylic Acid", Organic Service Branch I, OSHA
Salt Lake Technical Center, 1988, OSHA SLTC in-house
file.
5.3 Documentation of the Threshold Limit Values and Biological
Exposure Indices, Fifth Edition, American Conference of
Governmental Industrial Hygienists Inc., Cincinnati, OH, 1986, p.14.1.
5.4 Documentation of the Threshold Limit Values and Biological
Exposure Indices, Fifth Edition, American Conference of
Governmental Industrial Hygienists Inc., Cincinnati, OH, 1986, p.362.
5.5 Budavari, S., The Merck Index, Twelfth Edition, Merck
& Co., Inc., Whitehouse Station NJ, 1996, p. 23.
5.6 Budavari, S., The Merck Index, Twelfth Edition, Merck
& Co., Inc., Whitehouse Station NJ, 1996, p. 1015.
|